Controlling grain growth during the sintering of ceramics is critical to achieving desired material properties such as mechanical strength, thermal stability, and optical characteristics. Grain growth, if uncontrolled, can lead to larger grains that compromise the material's integrity, reduce its density, and negatively impact its performance. Proper grain size management ensures a uniform microstructure, optimal densification, and the preservation of functional properties. This is achieved through precise control of sintering parameters such as temperature, heating rate, and atmosphere, as well as adherence to material-specific guidelines.
Key Points Explained:
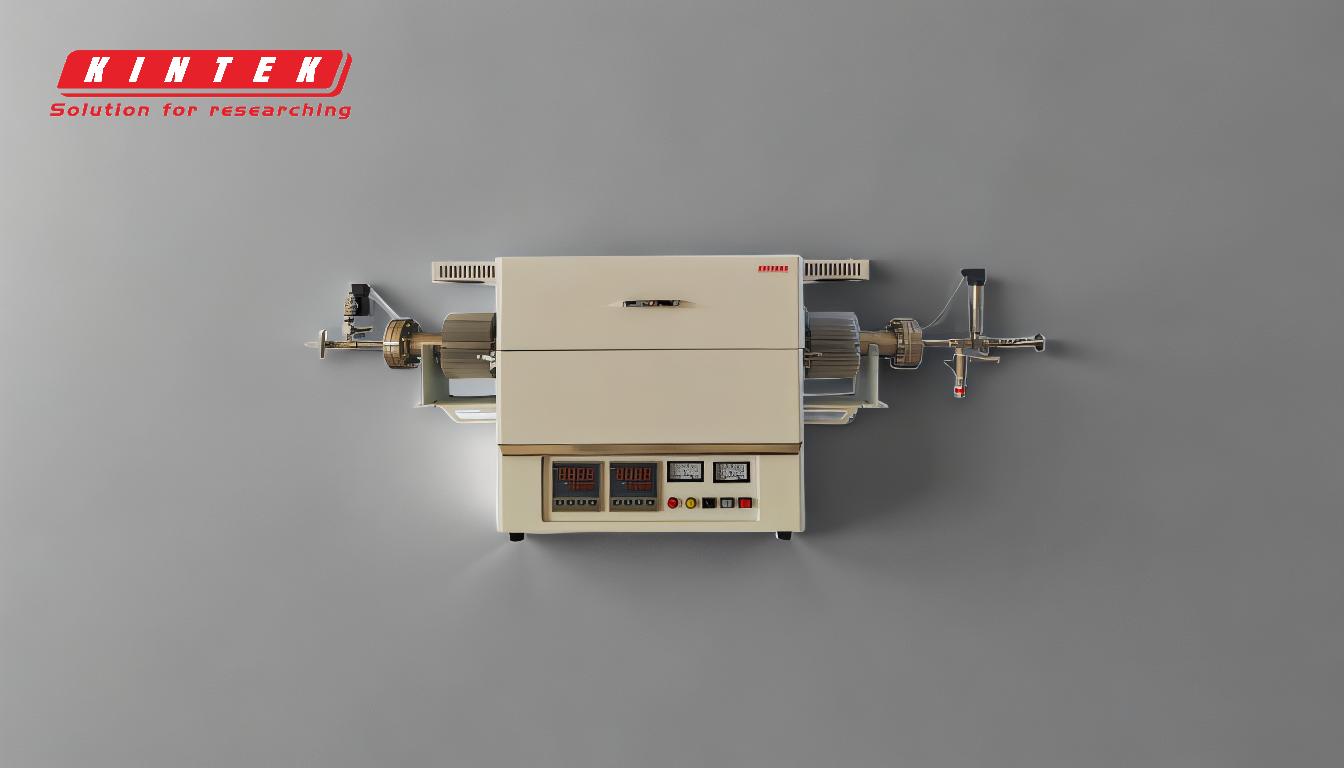
-
Impact of Grain Growth on Material Properties:
- Uncontrolled grain growth during sintering can result in larger grains, which weaken the mechanical properties of ceramics, such as fracture toughness and hardness.
- Larger grains can also reduce the material's density, leading to increased porosity and compromised thermal and electrical properties.
- For example, in zirconia ceramics, excessive grain growth at high temperatures can cause phase instability, cracking, and reduced translucency, which are undesirable for both structural and esthetic applications.
-
Role of Temperature Control:
- Temperature is a critical factor in sintering, as it directly influences grain boundary diffusion and bulk diffusion, which govern grain growth.
- High temperatures can accelerate grain growth, leading to coarser microstructures. Conversely, maintaining optimal sintering temperatures ensures controlled grain growth and uniform densification.
- For instance, sintering zirconia at excessively high temperatures can destabilize its crystalline structure, leading to uncontrolled phase transformations and mechanical failure.
-
Importance of Heating Rate:
- The heating rate during sintering affects the kinetics of grain growth and densification. A slower heating rate allows for more controlled grain growth and better elimination of porosity.
- Rapid heating can lead to uneven densification and exaggerated grain growth, resulting in a non-uniform microstructure and compromised material properties.
-
Influence of Particle Size and Composition:
- Smaller particles and homogeneous compositions promote better densification and controlled grain growth during sintering.
- Smaller particles have higher surface energy, which enhances diffusion and densification, while homogeneous compositions ensure uniform grain growth and microstructure.
- For example, fine-grained powders of advanced ceramics like alumina or silicon nitride are sintered at carefully controlled temperatures to achieve high-density, fine-grained microstructures with superior mechanical properties.
-
Effect of Sintering Atmosphere:
- The sintering atmosphere can influence grain growth by affecting the diffusion mechanisms and chemical reactions at grain boundaries.
- For non-oxide ceramics, a stabilizing atmosphere (e.g., nitrogen or argon) is often required to prevent oxidation and control grain growth.
-
Practical Considerations for Sintering:
- Adhering to the manufacturer’s recommended firing schedule is essential to achieve the desired grain size and material properties.
- Factors such as furnace design, insulation, and whether debinding and sintering are combined also play a role in controlling grain growth and ensuring cost-effective production.
By carefully managing these factors, manufacturers can control grain growth during sintering, ensuring the production of high-performance ceramics with tailored properties for specific applications.
Summary Table:
Factor | Impact on Grain Growth | Key Considerations |
---|---|---|
Temperature Control | High temperatures accelerate grain growth; optimal temperatures ensure controlled growth. | Maintain precise sintering temperatures to avoid phase instability and coarsening. |
Heating Rate | Slow heating promotes uniform densification; rapid heating leads to uneven grain growth. | Use controlled heating rates to eliminate porosity and achieve uniform microstructures. |
Particle Size | Smaller particles enhance densification and control grain growth. | Use fine-grained powders for high-density, fine-grained microstructures. |
Sintering Atmosphere | Atmosphere affects diffusion and chemical reactions at grain boundaries. | Use stabilizing atmospheres (e.g., nitrogen) for non-oxide ceramics. |
Practical Considerations | Adhering to firing schedules and furnace design ensures controlled grain growth. | Follow manufacturer guidelines and optimize furnace parameters for cost-effective production. |
Optimize your ceramic sintering process—contact our experts today for tailored solutions!