An inert atmosphere refers to an environment where reactive gases, particularly oxygen, are replaced with non-reactive gases to prevent oxidation, contamination, or unwanted chemical reactions. This concept is widely used in fields such as engineering, food preservation, and heat treatment to protect sensitive materials and processes. Inert atmospheres are typically created using gases like nitrogen (N₂) and argon (Ar), which are chemically inert and do not react with the materials they surround. This ensures the integrity, quality, and desired properties of the materials being processed or preserved. Applications range from laboratory furnaces to industrial heat-treating processes, where precise control over the environment is critical.
Key Points Explained:
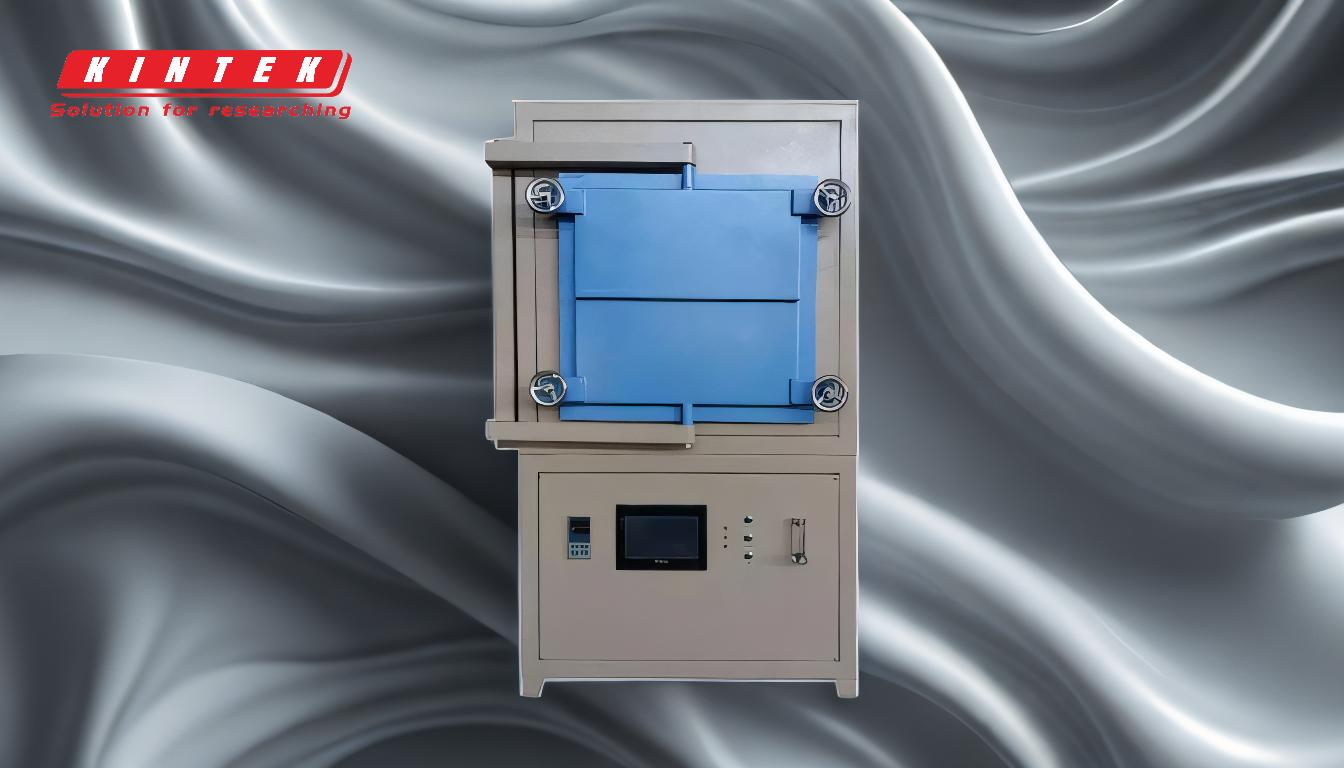
-
Definition of an Inert Atmosphere
- An inert atmosphere is a controlled environment where reactive gases, especially oxygen, are replaced with non-reactive gases to prevent oxidation, contamination, or unwanted chemical reactions.
- It is used to support specific functions, such as protecting materials during heat treatment, preserving food, or conducting sensitive laboratory experiments.
-
Purpose and Importance
- Preventing Oxidation: Inert atmospheres are crucial in processes where materials are prone to oxidation, such as heat-treating metals or preserving food. Oxidation can degrade materials, altering their properties and reducing their quality.
- Maintaining Integrity: By displacing reactive gases, inert atmospheres ensure that materials retain their desired properties, such as strength, durability, and chemical composition.
- Contamination Control: Inert atmospheres prevent contamination from reactive gases, which is essential in high-precision applications like semiconductor manufacturing or pharmaceutical production.
-
Common Inert Gases Used
- Nitrogen (N₂): The most widely used inert gas due to its abundance, cost-effectiveness, and non-reactive nature. It is particularly effective in protecting steel and other metals from oxidation during heat treatment.
- Argon (Ar): Another commonly used inert gas, especially in applications requiring higher purity or where nitrogen might react with certain materials. Argon is often used in welding and high-temperature processes.
-
Applications of Inert Atmospheres
- Heat Treatment: Inert atmospheres are essential in furnaces for heat-treating metals, where they prevent oxidation and ensure the materials maintain their desired properties.
- Food Preservation: Inert gases like nitrogen are used to displace oxygen in food packaging, extending shelf life by preventing spoilage and oxidation.
- Laboratory and Industrial Processes: Inert atmospheres are used in laboratories and industrial settings to protect sensitive samples or materials from exposure to reactive gases.
- Bonding and Curing: Inert atmospheres are employed in processes like bonding and curing, where exposure to oxygen could compromise the quality of the final product.
-
Equipment for Creating Inert Atmospheres
- Inert Gas Atmosphere Furnaces: These furnaces are designed with precision microprocessor-based temperature controls and energy-efficient insulation to maintain optimal conditions for heat treatment and other processes.
- Gas Delivery Systems: Systems that supply and regulate inert gases like nitrogen or argon to create and maintain the desired atmosphere.
- Sealed Environments: Containers or chambers designed to maintain an inert atmosphere, such as glove boxes used in laboratories for handling air-sensitive materials.
-
Benefits of Using Inert Atmospheres
- Enhanced Material Quality: By preventing oxidation and contamination, inert atmospheres ensure that materials retain their desired properties and performance.
- Cost Savings: Efficient use of inert gases and energy-efficient equipment reduces operational costs while maintaining high-quality outcomes.
- Process Control: Precision temperature and gas control systems enable consistent and repeatable results, which is critical in industries like aerospace, automotive, and electronics.
-
Challenges and Considerations
- Gas Selection: Choosing the right inert gas (e.g., nitrogen vs. argon) depends on the specific application and material being processed.
- Cost of Gases: While nitrogen is relatively inexpensive, argon can be more costly, impacting the overall budget for processes requiring high-purity inert atmospheres.
- System Maintenance: Ensuring the integrity of sealed environments and gas delivery systems requires regular maintenance to prevent leaks or contamination.
By understanding the concept, applications, and benefits of inert atmospheres, industries can make informed decisions to protect their materials and processes, ensuring high-quality outcomes and operational efficiency.
Summary Table:
Aspect | Details |
---|---|
Definition | Controlled environment with non-reactive gases replacing oxygen. |
Purpose | Prevent oxidation, maintain material integrity, and control contamination. |
Common Gases | Nitrogen (N₂), Argon (Ar) |
Applications | Heat treatment, food preservation, laboratory processes, bonding/curing. |
Equipment | Inert gas furnaces, gas delivery systems, sealed environments. |
Benefits | Enhanced material quality, cost savings, precise process control. |
Challenges | Gas selection, cost considerations, system maintenance. |
Discover how an inert atmosphere can improve your processes—contact our experts today!