The injection molding process is a highly efficient manufacturing method used to produce complex-shaped plastic parts in large quantities. It involves melting plastic material, injecting it into a press mold cavity under high pressure, cooling it to solidify, and then ejecting the finished product. This process is widely used in industries for its precision, repeatability, and ability to produce intricate designs. Below is a detailed step-by-step explanation of the injection molding process.
Key Points Explained:
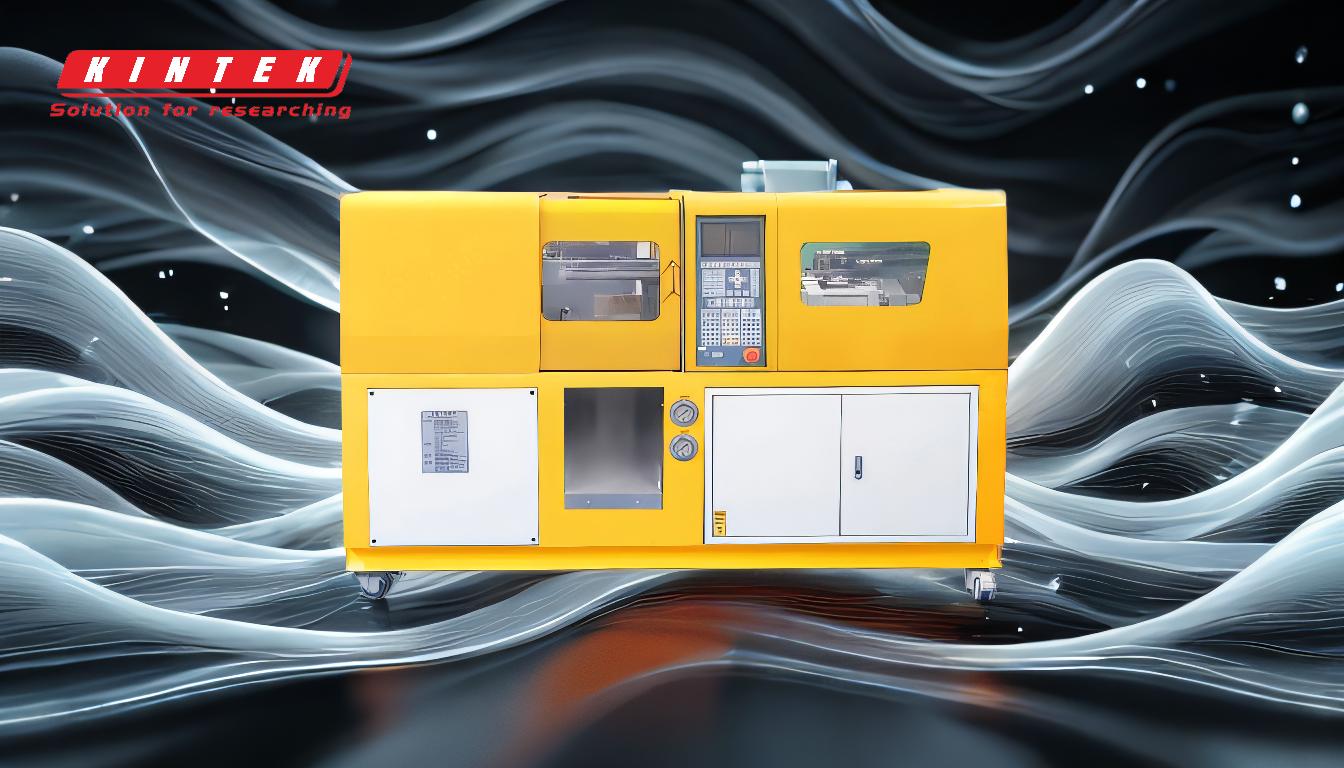
-
Material Preparation and Feeding
- Plastic pellets or granules are fed into the hopper of the injection molding machine.
- The material is then conveyed into the barrel, where it is heated and mixed by a rotating screw.
- The screw ensures uniform melting and homogenization of the plastic material.
-
Melting and Plasticization
- Inside the barrel, the plastic material is heated to its melting point, transforming it into a molten state.
- The screw continues to mix and compress the molten plastic, ensuring consistent viscosity and temperature.
- This step is critical for achieving high-quality molded parts.
-
Injection into the Mold Cavity
- Once the plastic is fully molten, the screw moves forward, acting as a plunger to inject the molten material into the mold cavity.
- High pressure is applied to ensure the material fills every detail of the mold, including intricate geometries.
- The mold is kept closed by a clamping unit to withstand the injection pressure.
-
Cooling and Solidification
- After the mold cavity is filled, the molten plastic begins to cool and solidify, taking the shape of the mold.
- Cooling time depends on the material properties, part thickness, and mold design.
- Proper cooling is essential to prevent defects like warping or sink marks.
-
Mold Opening and Ejection
- Once the part has solidified, the mold opens, and ejector pins push the finished product out of the mold cavity.
- The ejected part is then collected for further processing or packaging.
- The mold closes again, and the cycle repeats for the next part.
-
Post-Processing (if required)
- Some parts may require additional steps such as trimming, painting, or assembly.
- These steps ensure the final product meets the desired specifications and quality standards.
Detailed Explanation:
-
Material Preparation and Feeding
The process begins with the selection of the appropriate plastic material, which is typically in the form of pellets or granules. These materials are loaded into the hopper, which feeds them into the barrel of the injection molding machine. The barrel is equipped with a rotating screw that transports the material forward while heating it to the required temperature. This step ensures that the material is ready for the next phase of melting and plasticization. -
Melting and Plasticization
Inside the barrel, the plastic material is subjected to heat and mechanical shear from the screw. The combination of heat and friction melts the plastic, transforming it into a viscous fluid. The screw's design ensures thorough mixing, eliminating any inconsistencies in the material. This step is crucial because the quality of the molten plastic directly affects the final product's properties, such as strength, surface finish, and dimensional accuracy. -
Injection into the Mold Cavity
Once the plastic is fully molten, the injection phase begins. The screw moves forward, acting as a piston to inject the molten material into the mold cavity. The mold is designed with precision to create the desired shape of the part. High pressure is applied during injection to ensure the material fills all areas of the mold, including fine details and thin sections. The clamping unit holds the mold tightly closed to withstand the high injection pressure, preventing any leakage or deformation. -
Cooling and Solidification
After the mold cavity is filled, the cooling phase begins. The molten plastic starts to cool and solidify, taking the shape of the mold. Cooling time is a critical factor in the injection molding process, as it determines the cycle time and affects the part's quality. Proper cooling ensures that the part solidifies uniformly, minimizing defects such as warping, sink marks, or internal stresses. The cooling system within the mold, often using water channels, helps regulate the temperature and speed up the process. -
Mold Opening and Ejection
Once the part has sufficiently cooled and solidified, the mold opens, and the finished product is ejected. Ejector pins or plates are used to push the part out of the mold cavity. The mold then closes, and the cycle repeats for the next part. This step requires precision to ensure the part is ejected without damage and the mold is ready for the next injection. -
Post-Processing (if required)
Depending on the application, some parts may require additional post-processing steps. These can include trimming excess material (flash), painting or coating for aesthetic purposes, or assembling multiple components. Post-processing ensures the final product meets the required specifications and quality standards.
Conclusion:
The injection molding process is a versatile and efficient method for producing high-quality plastic parts with complex geometries. By following the steps of material preparation, melting, injection, cooling, ejection, and post-processing, manufacturers can achieve consistent and precise results. This process is widely used across industries due to its ability to produce large quantities of parts with minimal waste and high repeatability.
Summary Table:
Step | Description |
---|---|
1. Material Preparation | Plastic pellets are fed into the hopper, heated, and mixed in the barrel. |
2. Melting & Plasticization | The material is melted and homogenized by the screw for consistent viscosity. |
3. Injection into Mold | Molten plastic is injected into the mold cavity under high pressure. |
4. Cooling & Solidification | The plastic cools and solidifies into the desired shape. |
5. Mold Opening & Ejection | The mold opens, and ejector pins push out the finished part. |
6. Post-Processing | Additional steps like trimming or painting may be required for final quality. |
Ready to optimize your manufacturing process? Contact us today to learn more about injection molding solutions!