The LPCVD (Low-Pressure Chemical Vapor Deposition) method is a specialized technique used in the semiconductor industry for depositing thin films onto substrates. Unlike traditional CVD processes, LPCVD operates under low-pressure conditions, which enhances gas diffusion and improves the uniformity and quality of the deposited films. This method is particularly effective for applications requiring high precision, such as semiconductor manufacturing, where uniform film thickness and low contamination are critical. LPCVD eliminates the need for carrier gases, reduces particle contamination, and enables faster gas transport rates, making it a preferred choice for advanced thin-film deposition.
Key Points Explained:
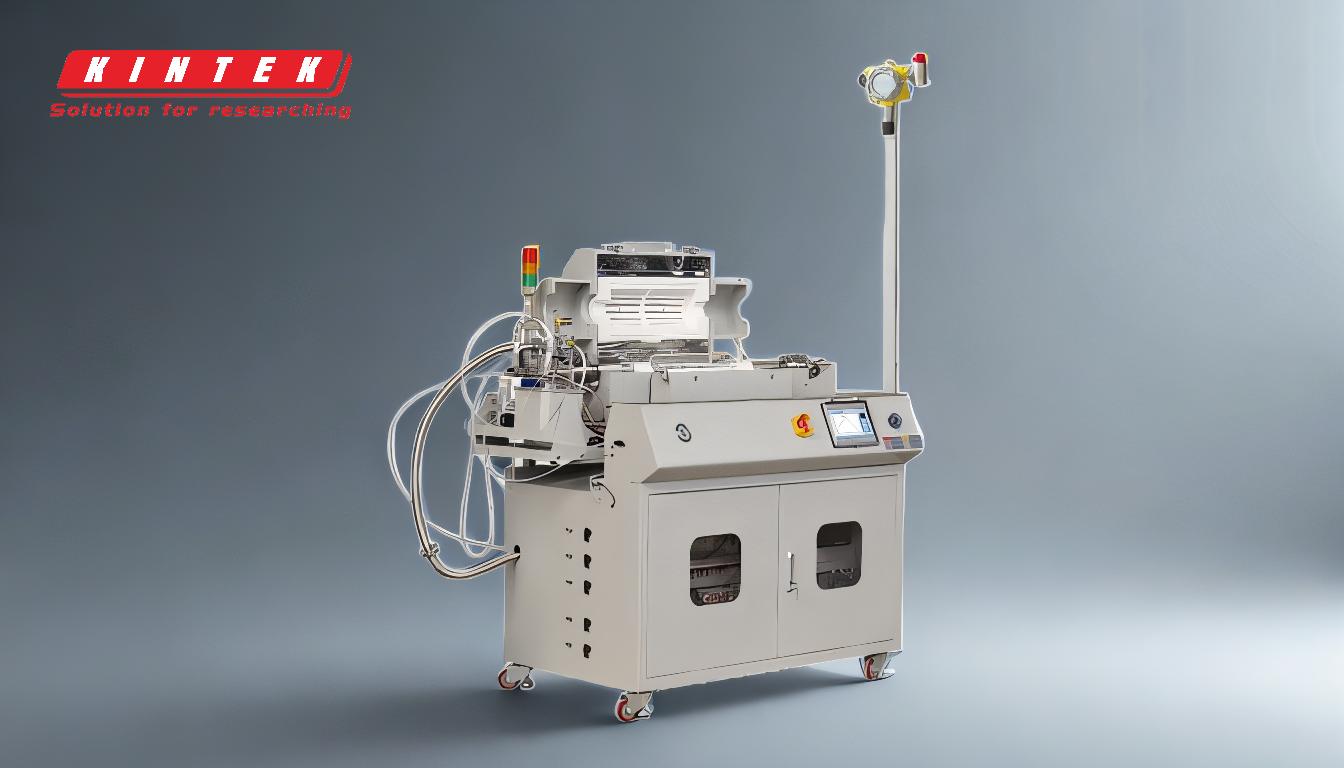
-
Definition of LPCVD:
- LPCVD stands for Low-Pressure Chemical Vapor Deposition. It is a variant of the CVD process that operates under reduced pressure conditions. This method is widely used in the semiconductor industry to deposit thin films with high precision and uniformity.
-
How LPCVD Works:
- In LPCVD, a gas is introduced into a reaction chamber containing a substrate. The chamber is heated to high temperatures, typically ranging from 500°C to 900°C, depending on the material being deposited.
- The low-pressure environment enhances the gas diffusion coefficient and increases the mean free path of gas molecules. This improves the uniformity of the film deposition and allows for better coverage of complex structures, such as trenches and vias.
-
Advantages of LPCVD:
- Improved Film Uniformity: The low-pressure environment ensures that the gas molecules are evenly distributed, leading to uniform film thickness and resistivity.
- Enhanced Trench Coverage: LPCVD is particularly effective for filling trenches and other complex geometries, making it ideal for semiconductor applications.
- Faster Gas Transport: The low-pressure conditions allow for quicker removal of impurities and reaction by-products, improving the overall quality of the deposited film.
- Reduced Contamination: By eliminating the need for carrier gases, LPCVD minimizes particle contamination, which is critical for high-purity applications.
-
Applications of LPCVD:
- LPCVD is extensively used in the semiconductor industry for depositing thin films of materials such as silicon dioxide (SiO₂), silicon nitride (Si₃N₄), and polysilicon. These films are essential for manufacturing integrated circuits, MEMS (Micro-Electro-Mechanical Systems), and other microelectronic devices.
-
Comparison with Other CVD Methods:
- Atmospheric Pressure CVD (APCVD): Unlike LPCVD, APCVD operates at atmospheric pressure, which can lead to less uniform films and higher contamination levels.
- Plasma-Enhanced CVD (PECVD): PECVD uses plasma to enhance the chemical reactions, allowing for lower deposition temperatures. However, it may not achieve the same level of film uniformity and trench coverage as LPCVD.
-
Key Considerations for LPCVD Equipment:
- Reaction Chamber Design: The chamber must be designed to withstand high temperatures and low pressures while maintaining a uniform gas flow.
- Temperature Control: Precise temperature control is crucial to ensure consistent film deposition and avoid defects.
- Gas Delivery System: The system must deliver gases accurately and uniformly to the reaction chamber to achieve high-quality films.
In summary, LPCVD is a highly effective method for depositing thin films with exceptional uniformity and precision. Its low-pressure operation, combined with high thermal conditions, makes it a cornerstone of modern semiconductor manufacturing and other advanced applications requiring high-quality thin films.
Summary Table:
Aspect | Details |
---|---|
Definition | Low-Pressure Chemical Vapor Deposition (LPCVD) |
Operation | Operates under low pressure, enhancing gas diffusion and film uniformity |
Temperature Range | 500°C to 900°C |
Advantages | Improved film uniformity, enhanced trench coverage, reduced contamination |
Applications | Semiconductor manufacturing, MEMS, microelectronics |
Comparison to APCVD | Better uniformity and lower contamination than APCVD |
Key Equipment Needs | High-temperature reaction chamber, precise temperature control, gas system |
Interested in learning more about LPCVD for your applications? Contact us today to speak with our experts!