The main frequency of an induction furnace varies depending on the application, material being melted, and furnace capacity. It typically ranges from utility frequency (50 or 60 Hz) to 400 kHz or higher. Smaller volumes of melts require higher frequencies due to the skin depth effect, which ensures efficient heating and melting. The frequency is also influenced by factors such as the desired stirring effect, melting efficiency, and material properties. Induction furnaces are designed to operate within specific frequency ranges to optimize performance, energy efficiency, and uniformity in melting or heating processes.
Key Points Explained:
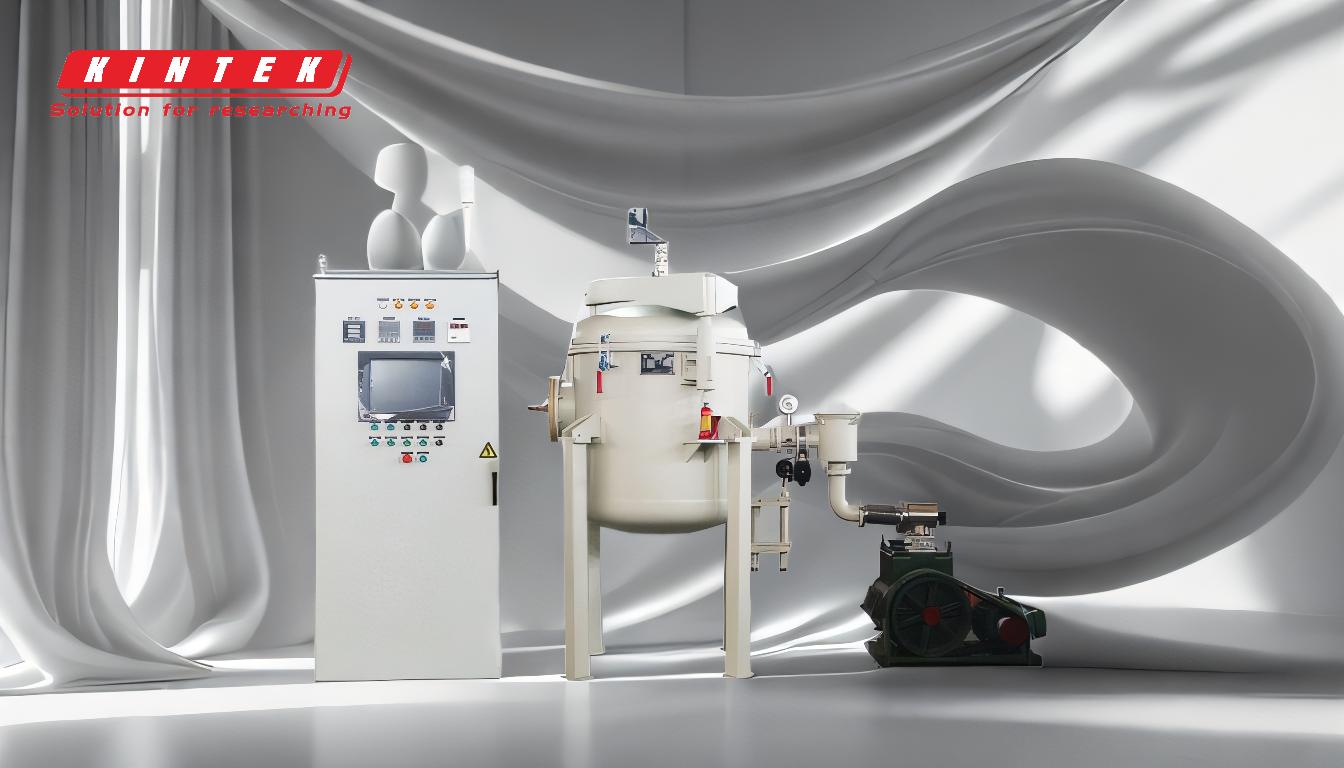
-
Frequency Range of Induction Furnaces:
- Induction furnaces operate across a wide frequency range, from utility frequency (50 or 60 Hz) to 400 kHz or higher.
- The choice of frequency depends on the application, material, and furnace capacity.
-
Factors Influencing Frequency Selection:
- Material Being Melted: Different materials have varying electrical and thermal properties, which affect the optimal frequency.
- Furnace Capacity: Smaller furnaces typically use higher frequencies to ensure efficient heating and melting.
- Skin Depth Effect: Higher frequencies result in shallower penetration of the electromagnetic field, which is ideal for smaller volumes. Lower frequencies are used for larger volumes to induce stirring or turbulence in the metal.
-
Advantages of Higher Frequencies:
- Efficiency: Higher frequencies allow for greater power application in smaller furnaces, improving melting efficiency.
- Uniformity: Higher frequencies ensure uniform heating and melting due to the skin depth effect.
- Reduced Turbulence: Higher frequencies minimize turbulence, which is beneficial for certain materials and processes.
-
Design Flexibility:
- The working frequency of medium-frequency induction furnaces can be adjusted by changing the coil design and compensating capacitor.
- This flexibility allows customization based on factors like melting material, quantity, stirring effect, noise levels, and melting efficiency.
-
Applications and Temperature Capabilities:
- Induction furnaces can reach temperatures of 1800°C or more, making them suitable for melting a wide range of materials.
- The forging heating temperature can reach 1250°C, and the melting temperature can reach 1650°C.
-
Operational Features:
- Automatic Frequency Scanning: Ensures smooth and stable operation by automatically adjusting the frequency.
- Constant Power Control: Maintains consistent voltage and current for optimal performance.
- Comprehensive Protection Systems: Includes over-voltage, over-current, and other safety mechanisms to protect the equipment.
-
Energy Efficiency and Environmental Benefits:
- Induction furnaces are power-saving and environmentally friendly, reducing operational costs.
- They ensure uniform smelting and composition uniformity, improving product quality.
-
Practical Considerations:
- Smaller Furnaces: Typically use higher frequencies for efficient melting of small quantities.
- Larger Furnaces: Use lower frequencies to induce stirring and turbulence, which is beneficial for larger volumes.
In summary, the main frequency of an induction furnace is highly variable and depends on the specific requirements of the melting or heating process. By understanding the factors influencing frequency selection, users can optimize furnace performance for their specific applications.
Summary Table:
Key Aspect | Details |
---|---|
Frequency Range | 50/60 Hz to 400 kHz or higher |
Factors Influencing Choice | Material, furnace capacity, skin depth effect, stirring, and efficiency |
Advantages of High Frequency | Efficient heating, uniform melting, reduced turbulence |
Design Flexibility | Adjustable via coil design and compensating capacitor |
Temperature Capabilities | Up to 1800°C for melting, 1250°C for forging |
Operational Features | Automatic frequency scanning, constant power control, safety mechanisms |
Energy Efficiency | Power-saving, environmentally friendly, uniform smelting |
Ready to optimize your induction furnace performance? Contact our experts today for tailored solutions!