All-ceramic restorations, particularly in the posterior region of the mouth, present a unique set of challenges despite their aesthetic and biocompatibility advantages. While they are ideal for front teeth due to their natural appearance and suitability for patients with metal allergies, their use in the posterior region is limited by their mechanical properties. The major drawback of all-ceramic restorations in the posterior of the mouth is their reduced durability compared to other materials like porcelain-fused-to-metal crowns. This limitation stems from the inherent brittleness of fine ceramics, which makes them more prone to fractures under the high chewing forces exerted in the posterior region. This brittleness can also lead to increased wear on adjacent teeth, further complicating their use in this area.
Key Points Explained:
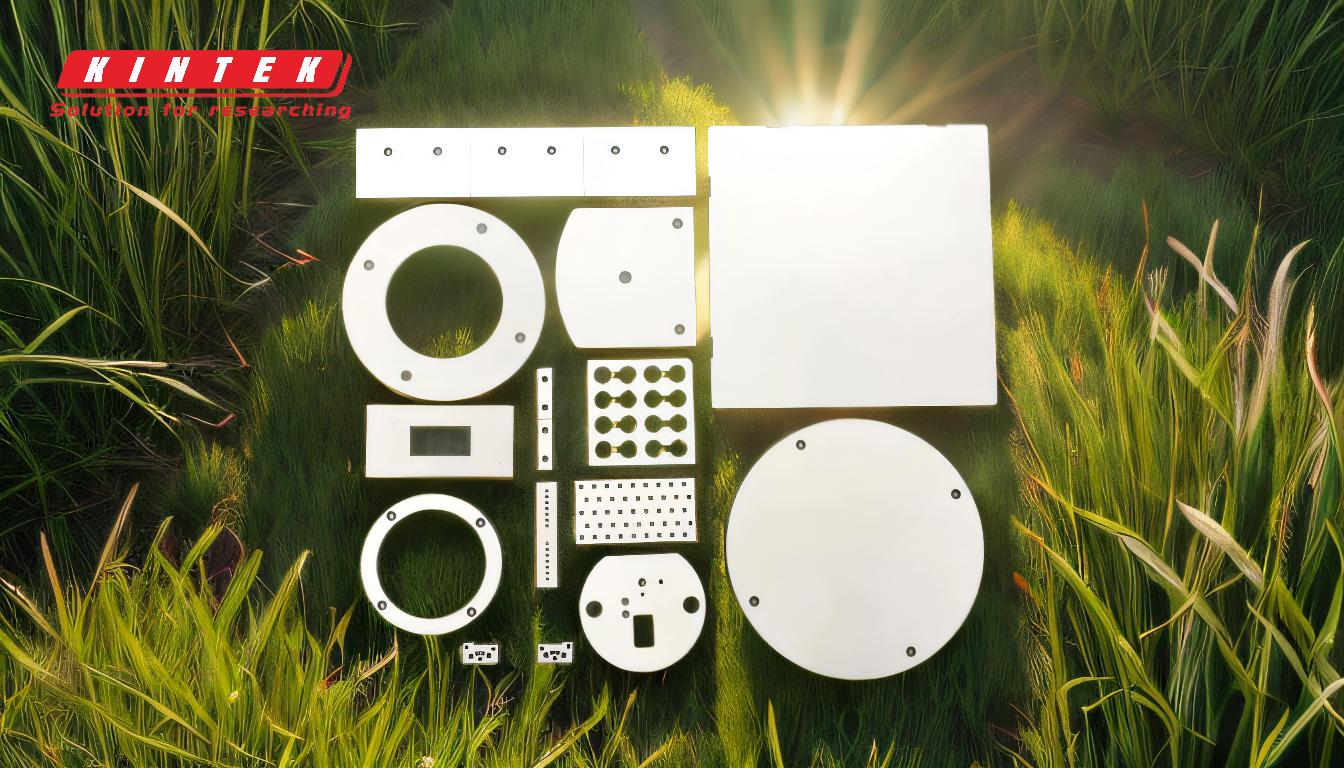
-
Reduced Durability in High-Stress Areas:
- The posterior region of the mouth is subjected to significant chewing forces, which can exceed the mechanical strength of all-ceramic materials. Fine ceramics, while strong, are inherently brittle and less resistant to fracture under these high-stress conditions compared to metal or porcelain-fused-to-metal alternatives. This makes them less suitable for molars and premolars, where durability is critical.
-
Brittleness and Fracture Risk:
- The brittleness of fine ceramics is a significant drawback in posterior restorations. Unlike metal or resin crowns, which can deform slightly under pressure, ceramics are more rigid and prone to cracking or chipping when subjected to sudden or heavy loads. This risk is particularly high in the posterior region, where the forces are more intense and frequent.
-
Increased Wear on Adjacent Teeth:
- All-ceramic restorations can cause more wear on opposing and adjacent teeth compared to metal or resin crowns. The hardness of fine ceramics, while beneficial for resisting wear on the restoration itself, can lead to accelerated wear on natural teeth, especially in the posterior region where occlusal forces are concentrated.
-
Limited Suitability for Posterior Use:
- While all-ceramic restorations are excellent for front teeth due to their aesthetic qualities, their mechanical limitations make them less ideal for posterior teeth. The high chewing forces and complex occlusal patterns in the posterior region demand materials with higher fracture toughness and durability, which ceramics often lack.
-
Alternative Materials for Posterior Restorations:
- For posterior restorations, materials like porcelain-fused-to-metal or high-strength zirconia ceramics are often preferred due to their superior durability and fracture resistance. These materials combine the aesthetic benefits of ceramics with the mechanical strength of metals, making them more suitable for high-stress areas.
In conclusion, while all-ceramic restorations offer significant aesthetic and biocompatibility advantages, their brittleness and reduced durability make them less suitable for the posterior region of the mouth. Fine ceramics, despite their many benefits, are better suited for anterior teeth where the forces are less intense, and aesthetics are a higher priority. For posterior restorations, alternative materials that offer greater strength and durability are often recommended to ensure long-term success and patient satisfaction.
Summary Table:
Key Drawback | Explanation |
---|---|
Reduced Durability in High-Stress Areas | Brittle ceramics are prone to fractures under intense chewing forces in the posterior region. |
Brittleness and Fracture Risk | Rigid ceramics are more likely to crack or chip under heavy loads. |
Increased Wear on Adjacent Teeth | Hard ceramics cause accelerated wear on natural teeth in high-stress areas. |
Limited Suitability for Posterior Use | All-ceramic restorations are better suited for anterior teeth due to lower forces. |
Alternative Materials | Porcelain-fused-to-metal or zirconia ceramics are preferred for posterior use. |
Need help choosing the right dental restoration? Contact our experts today!