Crucible steel is a type of steel produced by melting iron and carbon together in a crucible, a container designed to withstand extremely high temperatures. Historically, crucibles were made from clay, but modern crucibles can be made from materials like fused quartz, silicon carbide, and boron nitride, each chosen for their specific properties such as thermal shock resistance, durability, and thermal insulation. The process of making crucible steel involves filling the crucible with low-carbon wrought iron and carbon-rich organic materials, then heating it until the iron absorbs the carbon to form steel. Once the reaction is complete, the crucible is broken to retrieve the steel. This method was first used in India to produce wootz steel, a precursor to modern crucible steel.
Key Points Explained:
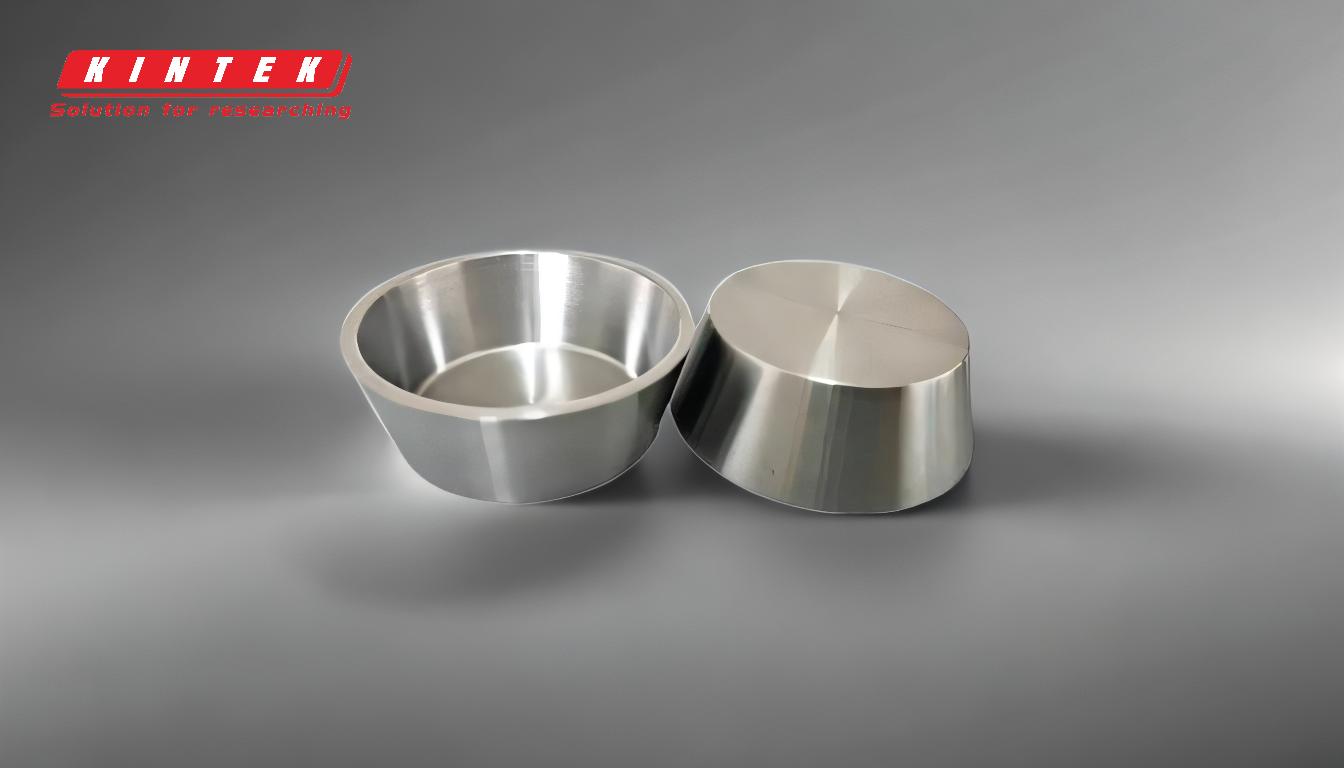
-
Definition of Crucible Steel:
- Crucible steel is a type of steel created by melting iron and carbon together in a crucible. This process allows for precise control over the carbon content, resulting in high-quality steel.
-
Historical Context:
- The earliest examples of crucible steel, known as wootz steel, originated in India. This steel was highly valued for its strength and was used to make weapons like the famous Damascus swords.
-
Materials Used for Crucibles:
- Clay: Historically, crucibles were made from clay due to its availability and ability to withstand high temperatures.
- Fused Quartz: Modern crucibles often use fused quartz because it is resistant to thermal shock, making it ideal for melting metals.
- Silicon Carbide: This material is durable and commonly used in semiconductor production.
- Boron Nitride: Known for its excellent thermal insulation properties, boron nitride is used in high-temperature vacuum furnaces.
-
Process of Making Crucible Steel:
- Filling the Crucible: The crucible is filled with low-carbon wrought iron and carbon-rich organic materials, such as leaves or wood.
- Heating: The crucible is heated to extremely high temperatures, allowing the iron to absorb the carbon.
- Breaking the Crucible: Once the reaction is complete, the crucible is broken to retrieve the steel.
-
Properties of Crucible Steel:
- High Carbon Content: The controlled addition of carbon results in steel with superior hardness and strength.
- Uniform Structure: The melting process ensures a uniform distribution of carbon, leading to consistent quality.
-
Applications of Crucible Steel:
- Historical Uses: Crucible steel was primarily used for making high-quality blades and tools.
- Modern Uses: Today, crucible steel is used in applications requiring high strength and durability, such as in the aerospace and automotive industries.
-
Advantages of Crucible Steel:
- Quality Control: The process allows for precise control over the steel's composition, resulting in high-quality products.
- Versatility: Crucible steel can be tailored to meet specific requirements, making it suitable for a wide range of applications.
-
Challenges in Production:
- High Temperatures: The process requires extremely high temperatures, which can be difficult to achieve and maintain.
- Material Costs: The materials used for modern crucibles, such as fused quartz and boron nitride, can be expensive.
By understanding the materials and processes involved in making crucible steel, one can appreciate the complexity and craftsmanship required to produce this high-quality material. Whether for historical weapons or modern industrial applications, crucible steel remains a testament to the ingenuity of metallurgical science.
Summary Table:
Aspect | Details |
---|---|
Definition | Steel made by melting iron and carbon in a crucible for precise carbon control. |
Historical Context | Originated in India as wootz steel, used for Damascus swords. |
Crucible Materials | Clay (historical), fused quartz, silicon carbide, boron nitride (modern). |
Production Process | Fill crucible with iron and carbon, heat to high temps, break to retrieve steel. |
Properties | High carbon content, uniform structure, superior hardness and strength. |
Applications | Historical: blades and tools; Modern: aerospace, automotive industries. |
Advantages | Precise quality control, versatility for tailored applications. |
Challenges | Requires high temperatures, expensive modern crucible materials. |
Want to learn more about crucible steel or explore its applications? Contact our experts today!