The maximum curing time required in a compression molding process depends on several factors, including the type of material being used, the thickness of the part, the curing temperature, and the specific requirements of the application. Generally, curing times can range from a few minutes to several hours. For thermosetting polymers, the curing process involves a chemical reaction that solidifies the material, and this reaction time is critical to achieving the desired mechanical properties. Thicker parts or those requiring higher strength may need longer curing times to ensure complete cross-linking of the polymer chains. Additionally, the curing temperature plays a significant role, as higher temperatures can accelerate the curing process but may also risk thermal degradation of the material. Therefore, the maximum curing time is not a fixed value but is determined by optimizing these variables to achieve the best results for the specific application.
Key Points Explained:
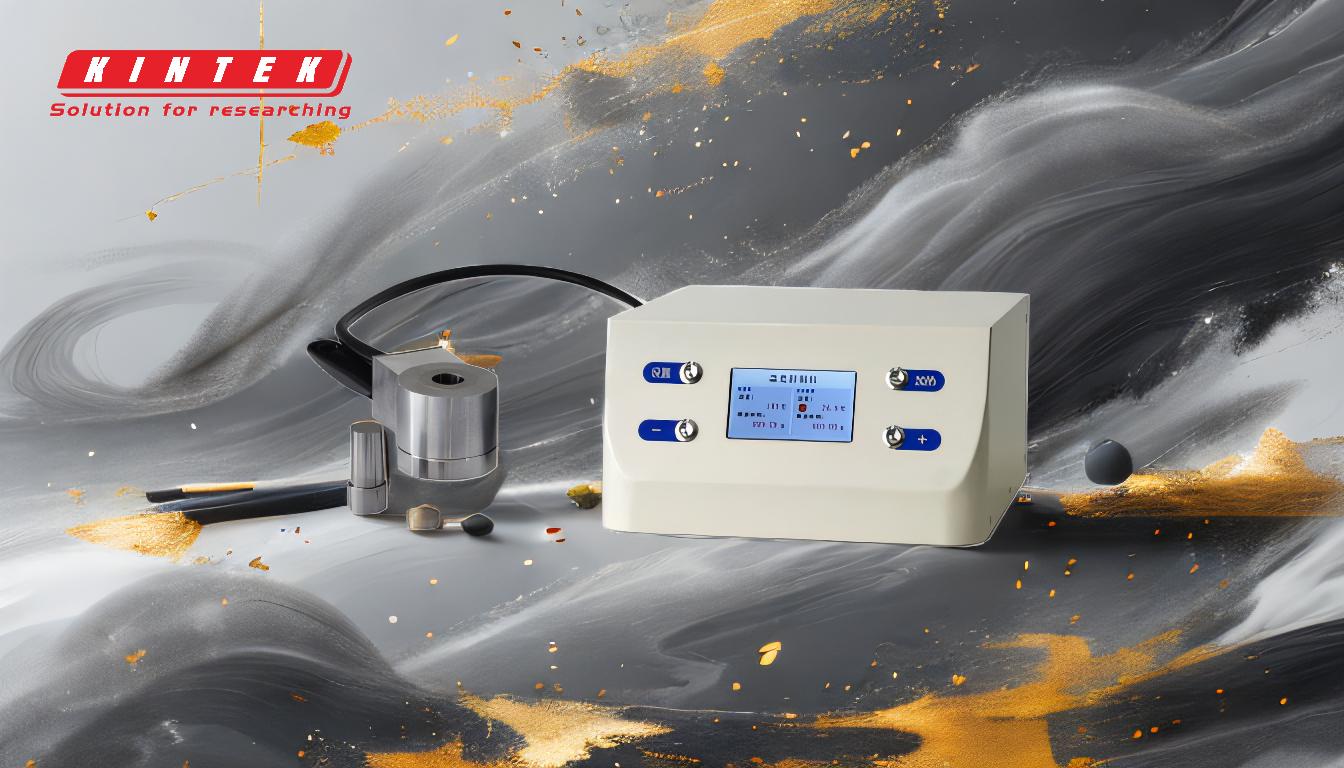
-
Material Type:
- The type of material being molded significantly influences the curing time. Thermosetting polymers, such as epoxy or phenolic resins, require a specific amount of time to undergo the chemical reactions necessary for curing. These materials cannot be remelted or reshaped once cured, making the curing time a critical parameter.
-
Part Thickness:
- Thicker parts generally require longer curing times because heat must penetrate through the entire thickness to ensure uniform curing. Inadequate curing in thicker sections can lead to weak spots or incomplete cross-linking, compromising the part's strength and durability.
-
Curing Temperature:
- The curing temperature is a crucial factor that affects the curing time. Higher temperatures can speed up the curing process by accelerating the chemical reactions. However, excessively high temperatures can cause thermal degradation of the material, leading to defects such as cracking or warping. Therefore, the temperature must be carefully controlled to balance curing speed and material integrity.
-
Application Requirements:
- The specific requirements of the application, such as the desired mechanical properties, dimensional accuracy, and surface finish, also dictate the curing time. For example, parts that need to withstand high stress or harsh environments may require longer curing times to achieve the necessary strength and stability.
-
Optimization:
- Determining the maximum curing time involves optimizing the interplay between material properties, part geometry, curing temperature, and application requirements. This often requires experimentation and testing to find the optimal conditions that produce the best results without compromising the material's properties.
-
Process Monitoring:
- Monitoring the curing process is essential to ensure that the material cures uniformly and completely. Techniques such as differential scanning calorimetry (DSC) or real-time monitoring of temperature and pressure can help in assessing the progress of the curing reaction and making necessary adjustments.
In summary, the maximum curing time in a compression molding process is a variable that depends on multiple factors, including material type, part thickness, curing temperature, and application requirements. Proper optimization and monitoring are essential to achieve the desired material properties and ensure the quality of the final product.
Summary Table:
Factor | Impact on Curing Time |
---|---|
Material Type | Thermosetting polymers (e.g., epoxy) require specific curing times for chemical reactions. |
Part Thickness | Thicker parts need longer curing times to ensure uniform heat penetration. |
Curing Temperature | Higher temperatures speed up curing but risk thermal degradation. |
Application Needs | High-strength or precision parts may require extended curing times. |
Optimization | Balancing factors ensures optimal curing without compromising material properties. |
Process Monitoring | Techniques like DSC help track curing progress for consistent results. |
Need help optimizing your compression molding process? Contact our experts today for tailored solutions!