The maximum frequency of induction heaters is influenced by several factors, including the material's conductivity, magnetic properties, size, and thickness. Higher-frequency alternating currents result in lower heating depth penetration, making them suitable for smaller and thinner materials. Materials with higher resistivity heat up more quickly, and magnetic materials generate heat through both eddy currents and hysteresis effects. Understanding these factors helps in selecting the appropriate frequency for specific applications.
Key Points Explained:
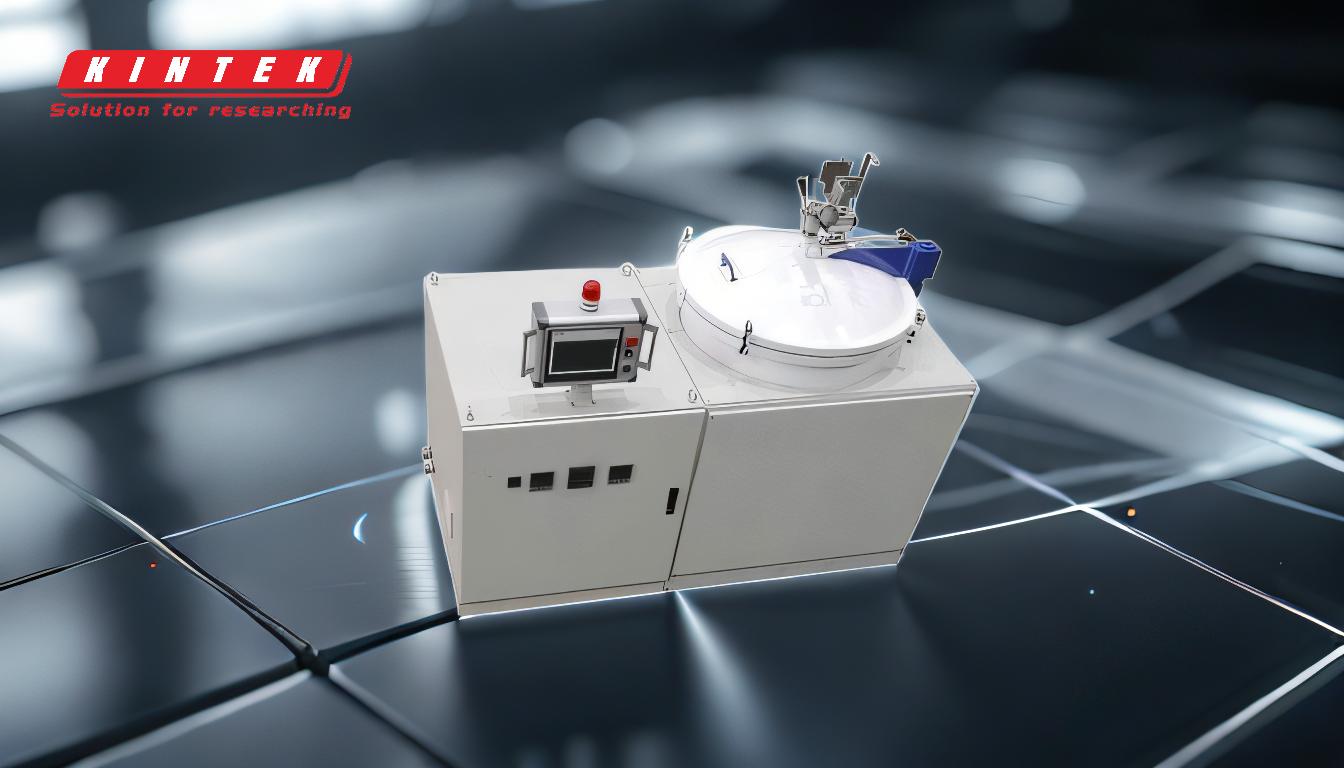
-
Material Conductivity and Resistivity:
- Materials with higher conductivity, such as copper and aluminum, require lower frequencies for effective heating because they allow eddy currents to flow more easily.
- Higher resistivity materials, like steel, heat up more quickly and can benefit from higher frequencies to achieve the desired heating effect.
-
Magnetic Properties:
- Magnetic materials, such as iron and nickel, generate heat through both eddy currents and hysteresis effects. This dual mechanism allows for efficient heating even at lower frequencies.
- Non-magnetic materials rely solely on eddy currents for heating, often necessitating higher frequencies to achieve similar heating rates.
-
Size and Thickness of the Material:
- Smaller and thinner materials heat up faster and require higher frequencies to ensure uniform heating. Higher frequencies result in lower depth penetration, making them ideal for surface heating of thin materials.
- Larger and thicker materials benefit from lower frequencies, which provide deeper penetration and more uniform heating throughout the material.
-
Frequency and Heating Depth:
- The relationship between frequency and heating depth is inversely proportional. Higher frequencies result in shallower heating depths, making them suitable for applications requiring precise surface heating.
- Lower frequencies provide deeper penetration, making them ideal for heating thicker materials or achieving uniform heating throughout the material.
-
Applications and Frequency Selection:
- High-frequency induction heaters (ranging from 100 kHz to several MHz) are commonly used in applications such as surface hardening, brazing, and annealing of thin materials.
- Medium-frequency induction heaters (ranging from 1 kHz to 100 kHz) are suitable for deeper penetration applications, such as through-heating of thicker materials.
- Low-frequency induction heaters (below 1 kHz) are used for very deep penetration applications, such as heating large billets or heavy forgings.
By considering these factors, one can select the appropriate frequency for an induction heater to achieve optimal heating results for specific materials and applications.
Summary Table:
Factor | Effect on Frequency |
---|---|
Material Conductivity | High conductivity (e.g., copper) requires lower frequencies. |
Material Resistivity | High resistivity (e.g., steel) benefits from higher frequencies. |
Magnetic Properties | Magnetic materials (e.g., iron) heat efficiently at lower frequencies. |
Size and Thickness | Smaller/thinner materials need higher frequencies; larger/thicker materials need lower frequencies. |
Frequency and Heating Depth | Higher frequencies = shallow heating; lower frequencies = deeper penetration. |
Applications | High-frequency: surface hardening; Medium-frequency: through-heating; Low-frequency: deep heating. |
Need help selecting the right induction heater frequency? Contact our experts today!