DC sputtering is a widely used Physical Vapor Deposition (PVD) technique for depositing thin films onto substrates. The process involves bombarding a target material with high-energy ions, typically from an inert gas like argon, causing atoms to be ejected from the target surface. These ejected atoms then travel through a vacuum and deposit onto a substrate, forming a thin film. The mechanism relies on the transfer of momentum from the ions to the target atoms, which is influenced by factors such as ion energy, target material properties, and process conditions. DC sputtering is particularly effective for conductive materials, as it utilizes a direct current (DC) power supply to generate the plasma needed for ion bombardment.
Key Points Explained:
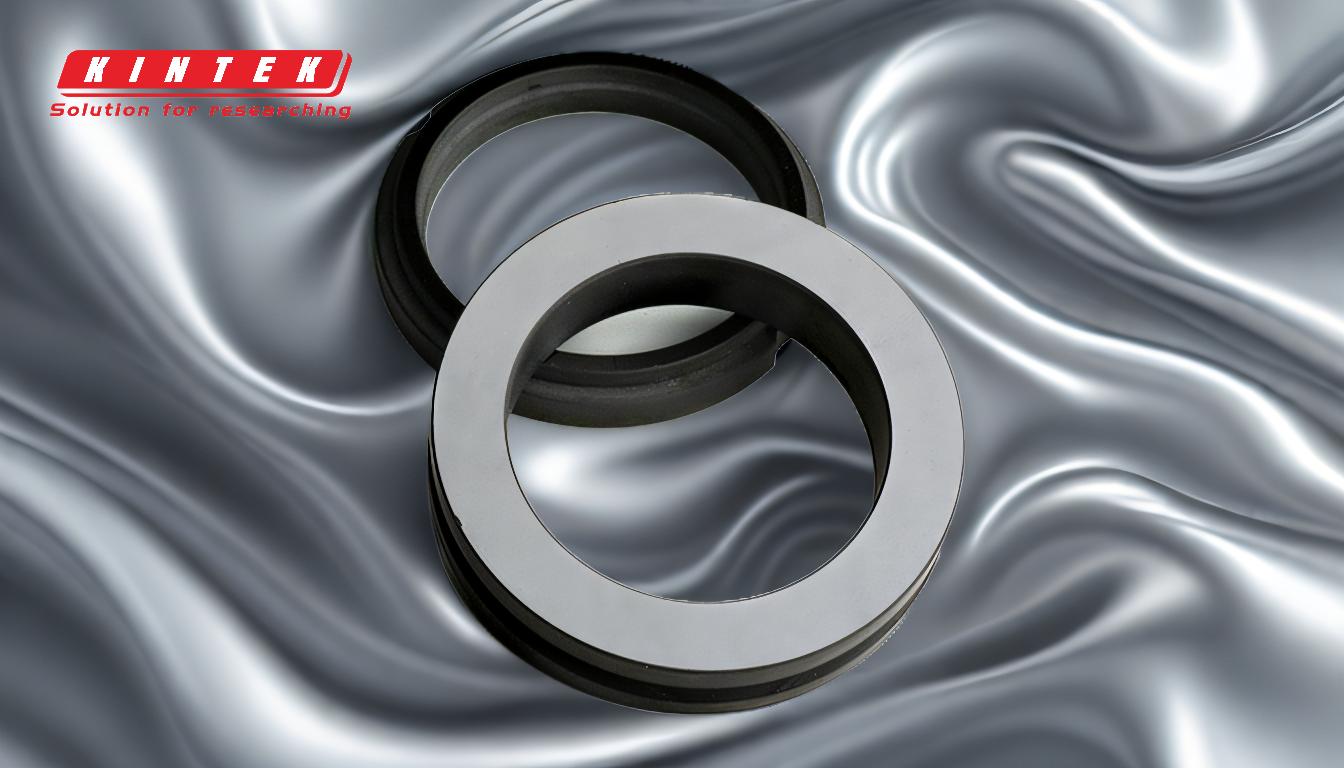
-
Ion Bombardment and Sputtering:
- In DC sputtering, a high-voltage DC power supply is used to create a glow discharge plasma in a vacuum chamber filled with an inert gas, typically argon.
- Positive ions from the plasma are accelerated towards the negatively charged target (cathode) due to the applied voltage.
- When these ions collide with the target, they transfer their kinetic energy to the target atoms, causing them to be ejected from the surface. This process is known as sputtering.
-
Thin Film Formation:
- The sputtered atoms are ejected from the target and travel through the vacuum chamber.
- These atoms then condense onto the substrate, forming a thin film. The film's properties, such as thickness, uniformity, and adhesion, depend on factors like the sputtering rate, substrate temperature, and chamber pressure.
-
Sputtering Rate Calculation:
- The sputtering rate is a critical parameter that determines how quickly material is deposited onto the substrate.
- It can be calculated using the formula:
[
R_{\text{sputter}} = \left(\frac{\Phi}{2}\right) \times \left(\frac{n}{N_A}\right) \times \left(\frac{A}{d}\right) \times \left(\frac{v}{1 + \frac{v^2}{v_c^2}}\right)
]
where:
- (\Phi) is the ion flux density,
- (n) is the number of target atoms per unit volume,
- (N_A) is Avogadro's number,
- (A) is the atomic weight of the target material,
- (d) is the distance between the target and substrate,
- (v) is the average velocity of the sputtered atoms,
- (v_c) is the critical velocity.
-
Process Steps:
- The DC sputtering process typically involves the following steps:
- Vacuuming the Chamber: The deposition chamber is evacuated to a low pressure (around (10^{-6}) torr) to minimize contamination and ensure a clean environment for deposition.
- Introducing Sputtering Gas: An inert gas, such as argon, is introduced into the chamber at a controlled pressure.
- Generating Plasma: A high-voltage DC power supply is applied between the target (cathode) and the substrate (anode), generating a glow discharge plasma.
- Ionization and Acceleration: Free electrons in the plasma collide with argon atoms, ionizing them and creating positive ions. These ions are then accelerated towards the target due to the electric field.
- Sputtering: The accelerated ions collide with the target, ejecting target atoms into the gas phase.
- Deposition: The ejected atoms travel through the vacuum and condense onto the substrate, forming a thin film.
- The DC sputtering process typically involves the following steps:
-
Advantages of DC Sputtering:
- High Deposition Rates: DC sputtering allows for relatively high deposition rates, making it suitable for industrial applications.
- Good Adhesion: The films produced by DC sputtering typically have excellent adhesion to the substrate.
- Versatility: DC sputtering can be used to deposit a wide range of materials, including metals, alloys, and some conductive ceramics.
-
Limitations:
- Material Conductivity: DC sputtering is primarily limited to conductive materials. Non-conductive materials require alternative techniques, such as RF sputtering.
- Heat Generation: The process can generate significant heat, which may require specialized cooling systems to manage.
In summary, DC sputtering is a highly effective PVD technique for depositing thin films of conductive materials. The process relies on the bombardment of a target material with high-energy ions, causing atoms to be ejected and deposited onto a substrate. By carefully controlling parameters such as ion energy, gas pressure, and substrate temperature, high-quality thin films with desired properties can be achieved.
Summary Table:
Key Aspect | Details |
---|---|
Process | Bombardment of a target with high-energy ions to eject atoms for deposition. |
Key Steps | Vacuuming, gas introduction, plasma generation, ionization, sputtering, deposition. |
Advantages | High deposition rates, excellent adhesion, versatile for conductive materials. |
Limitations | Limited to conductive materials, requires heat management. |
Interested in DC sputtering for your thin film needs? Contact us today to learn more!