Pyrolysis is a thermochemical decomposition process where organic materials are heated to high temperatures (typically 300-900°C) in the absence of oxygen, causing them to break down into smaller molecules. This process results in the formation of gases (syngas), liquids (bio-oil), and solids (bio-char), which can be used for various applications, such as fuel production, chemical synthesis, and waste reduction. The mechanism involves breaking chemical bonds in the material's molecules due to heat, leading to the formation of smaller, more volatile compounds. The absence of oxygen prevents combustion, ensuring the material decomposes rather than burns. The process can be optimized by controlling temperature, pressure, and the presence of catalysts or inert atmospheres to maximize the yield of desired products.
Key Points Explained:
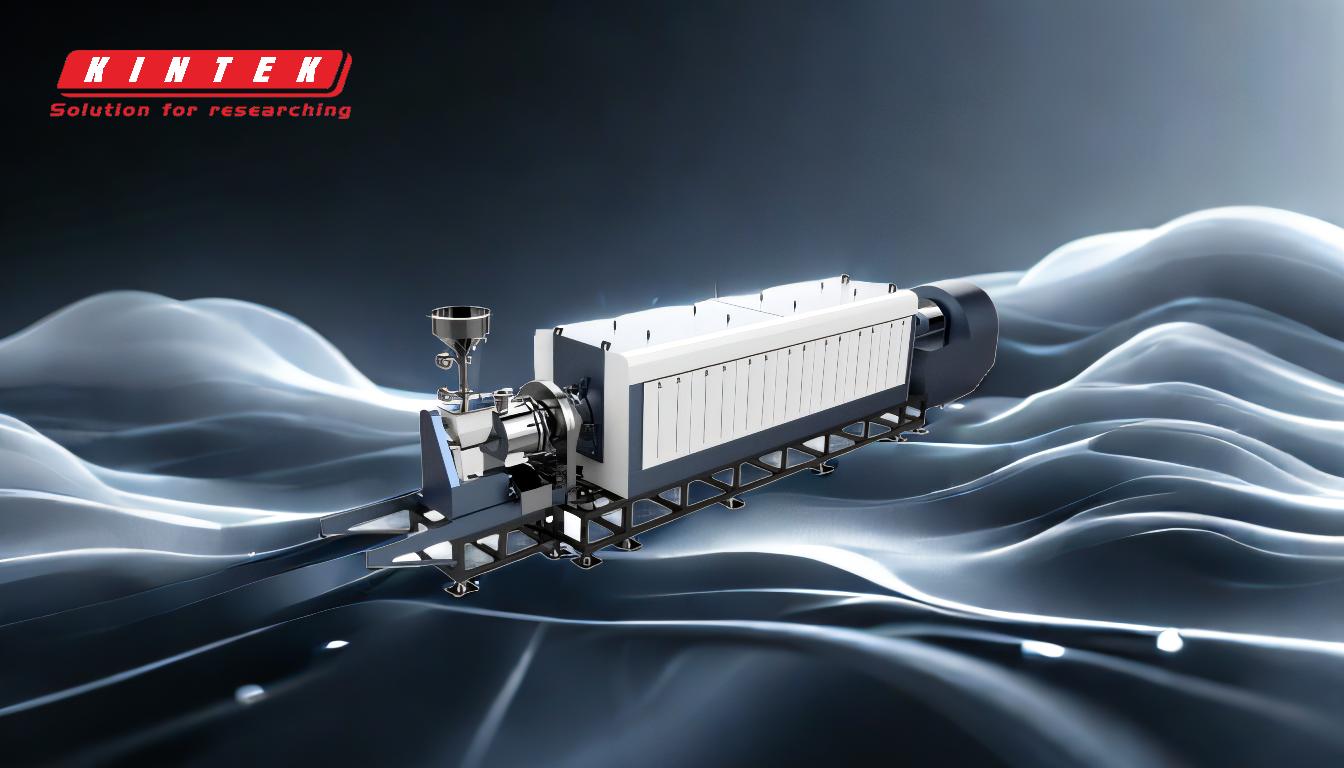
-
Definition of Pyrolysis:
- Pyrolysis is a thermochemical process where organic materials are decomposed by heat in the absence of oxygen.
- The process breaks down complex molecules into smaller, simpler compounds, producing gases, liquids, and solids.
-
Temperature Range:
- Pyrolysis typically occurs at temperatures between 300°C and 900°C.
- The specific temperature range depends on the material being processed and the desired end products.
-
Absence of Oxygen:
- Oxygen is excluded to prevent combustion, ensuring the material decomposes rather than burns.
- This allows for the controlled breakdown of the material into useful byproducts.
-
Products of Pyrolysis:
- Gases (Syngas): Includes hydrogen, carbon monoxide, and methane, which can be used as fuel or chemical feedstocks.
- Liquids (Bio-oil): A mixture of water and volatile organic compounds, which can be refined into fuel or used in chemical synthesis.
- Solids (Bio-char): Carbon-rich material that can be used as a soil amendment or for carbon sequestration.
-
Mechanism of Chemical Bond Breaking:
- Heating the material above its decomposition temperature causes the breaking of chemical bonds in its molecules.
- This results in the formation of smaller molecules or residues with larger molecular mass.
-
Process Conditions:
- Pyrolysis can be conducted in a vacuum or inert atmosphere to avoid side reactions like combustion or hydrolysis.
- The presence of catalysts can enhance the breakdown of the material and improve the yield of desired products.
-
Applications of Pyrolysis:
- Waste Management: Converts plastic waste, biomass, and tires into useful products, reducing landfill use.
- Energy Production: Generates syngas and bio-oil that can be used as renewable fuels.
- Chemical Production: Provides raw materials for the synthesis of chemicals and other valuable substances.
-
Energy Intensiveness:
- Pyrolysis is an energy-intensive process, requiring significant heat input to achieve the necessary temperatures.
- The energy efficiency of the process can be improved by optimizing process conditions and using heat recovery systems.
-
Side Reactions:
- If oxygen or water is present, side reactions like combustion or hydrolysis can occur, reducing the yield of desired products.
- Conducting pyrolysis in an inert atmosphere minimizes these side reactions.
-
Process Optimization:
- The yield and composition of pyrolysis products can be controlled by adjusting temperature, pressure, and the presence of catalysts.
- Pre-treatment of the feedstock, such as grinding and removing impurities, can also improve the efficiency of the process.
By understanding these key points, one can appreciate the complexity and versatility of pyrolysis as a method for converting waste materials into valuable resources. The process not only helps in waste reduction but also contributes to the production of renewable energy and chemicals, making it a crucial technology in the transition to a more sustainable future.
Summary Table:
Key Aspect | Details |
---|---|
Definition | Thermochemical decomposition of organic materials in the absence of oxygen. |
Temperature Range | 300°C to 900°C, depending on material and desired products. |
Products | Syngas (gases), bio-oil (liquids), bio-char (solids). |
Applications | Waste management, renewable energy, chemical production. |
Process Conditions | Controlled temperature, inert atmosphere, and optional catalysts. |
Energy Efficiency | Optimized through heat recovery and pre-treatment of feedstock. |
Discover how pyrolysis can transform your waste into valuable resources—contact our experts today!