Thin film deposition is a critical process in materials science and engineering, used to apply thin layers of material onto a substrate. The methods are broadly categorized into chemical vapor deposition (CVD) and physical vapor deposition (PVD). CVD involves chemical reactions to produce high-purity thin films, while PVD relies on physical processes like vaporization and condensation. Both categories include numerous techniques, such as thermal evaporation, sputtering, electroplating, and atomic layer deposition (ALD), each suited for specific applications and material properties. Understanding these methods is essential for selecting the right technique based on the desired film characteristics, substrate type, and application requirements.
Key Points Explained:
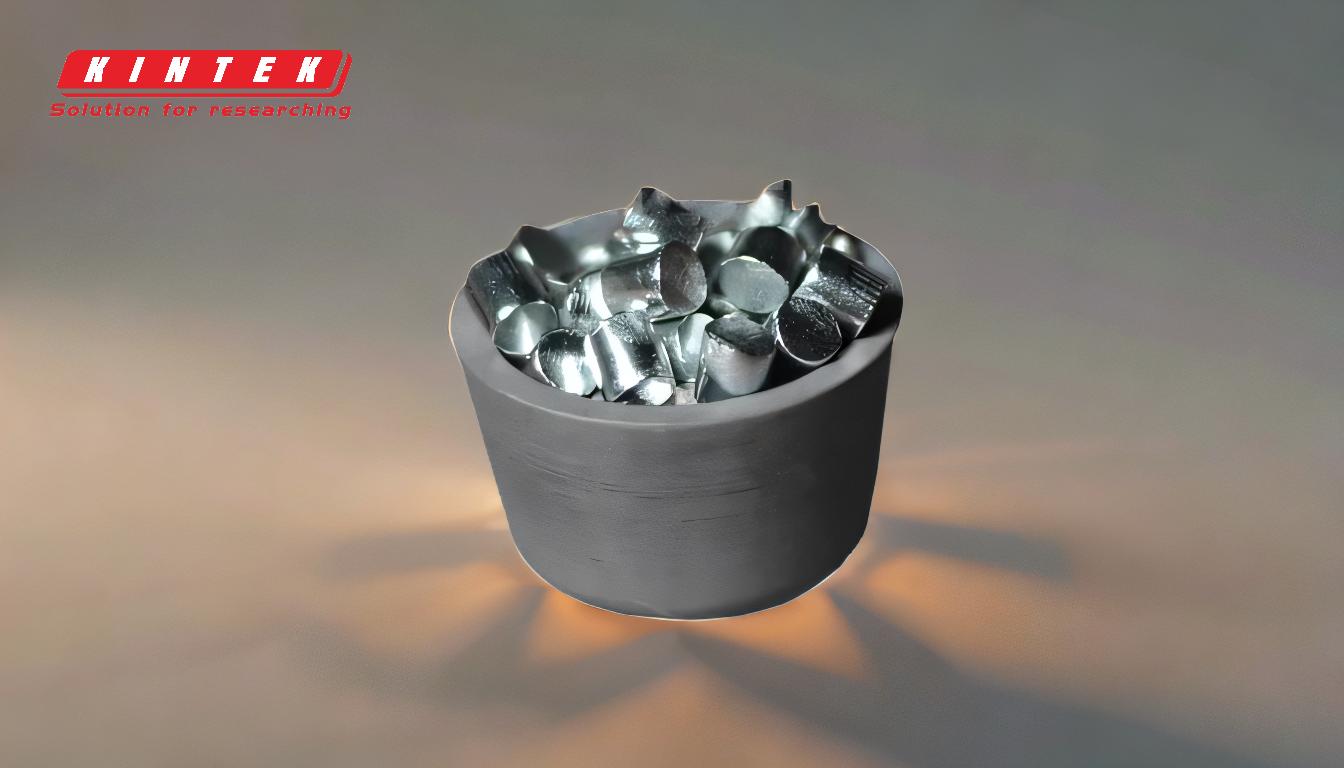
-
Overview of Thin Film Deposition Methods
- Thin film deposition techniques are divided into two main categories: Chemical Vapor Deposition (CVD) and Physical Vapor Deposition (PVD).
- These methods are used to create thin layers of material, typically less than one micron thick, on various substrates.
- The choice of method depends on factors like material type, substrate compatibility, and desired film properties.
-
Chemical Vapor Deposition (CVD)
- Definition: CVD involves chemical reactions in a gaseous phase to produce a thin film on a substrate.
-
Key Techniques:
- Standard CVD: Uses thermal energy to drive chemical reactions.
- Plasma-Enhanced CVD (PECVD): Utilizes plasma to lower the reaction temperature, making it suitable for temperature-sensitive substrates.
- Atomic Layer Deposition (ALD): A precise method where thin films are deposited one atomic layer at a time, ensuring excellent uniformity and control.
- Applications: CVD is widely used in semiconductor manufacturing, solar cells, and protective coatings.
- Advantages: High purity, excellent conformality, and ability to deposit complex materials.
- Limitations: High temperatures and complex chemical precursors can limit its use.
-
Physical Vapor Deposition (PVD)
- Definition: PVD involves the physical vaporization of a solid material in a vacuum, which then condenses onto a substrate.
-
Key Techniques:
- Thermal Evaporation: Material is heated until it vaporizes and deposits onto the substrate.
- Sputtering: A target material is bombarded with ions, causing atoms to be ejected and deposited onto the substrate.
- Electron Beam Evaporation: Uses an electron beam to vaporize the target material.
- Pulsed Laser Deposition (PLD): A laser ablates the target material, creating a plasma that deposits onto the substrate.
- Applications: PVD is used in optical coatings, wear-resistant coatings, and microelectronics.
- Advantages: High deposition rates, good adhesion, and versatility in material selection.
- Limitations: Line-of-sight deposition can result in uneven coatings on complex geometries.
-
Comparison of CVD and PVD
- Process Mechanism: CVD relies on chemical reactions, while PVD involves physical processes like vaporization and condensation.
- Temperature Requirements: CVD often requires higher temperatures compared to PVD.
- Film Quality: CVD typically produces films with better conformality and step coverage, while PVD films may have better adhesion and density.
- Cost and Complexity: CVD systems are generally more complex and expensive due to the need for chemical precursors and precise control.
-
Other Deposition Methods
- Electroplating: A chemical method where a thin film is deposited via electrochemical reactions.
- Sol-Gel: A wet-chemical technique that involves the transition of a solution into a gel, which is then dried to form a thin film.
- Dip Coating and Spin Coating: Simple methods for applying thin films from liquid solutions, often used for polymers and coatings.
- Molecular Beam Epitaxy (MBE): A highly controlled PVD technique used for growing high-quality crystalline films, commonly in semiconductor research.
-
Factors Influencing Method Selection
- Material Properties: The type of material being deposited (e.g., metals, ceramics, polymers) influences the choice of method.
- Substrate Compatibility: The substrate’s thermal and chemical stability must be considered.
- Film Thickness and Uniformity: Some methods, like ALD, offer exceptional control over film thickness and uniformity.
- Application Requirements: Specific applications, such as microelectronics or optical coatings, may demand particular deposition techniques.
-
Emerging Trends in Thin Film Deposition
- Hybrid Methods: Combining CVD and PVD techniques to leverage the advantages of both.
- Nanotechnology: Development of methods for depositing ultra-thin films at the nanoscale.
- Sustainability: Efforts to reduce the environmental impact of deposition processes, such as using greener chemical precursors in CVD.
By understanding these key points, equipment and consumable purchasers can make informed decisions about the most suitable deposition method for their specific needs, ensuring optimal performance and cost-effectiveness.
Summary Table:
Category | Key Techniques | Applications | Advantages | Limitations |
---|---|---|---|---|
Chemical Vapor Deposition (CVD) | Standard CVD, Plasma-Enhanced CVD (PECVD), Atomic Layer Deposition (ALD) | Semiconductor manufacturing, solar cells, protective coatings | High purity, excellent conformality, complex material deposition | High temperatures, complex chemical precursors |
Physical Vapor Deposition (PVD) | Thermal Evaporation, Sputtering, Electron Beam Evaporation, Pulsed Laser Deposition | Optical coatings, wear-resistant coatings, microelectronics | High deposition rates, good adhesion, versatile material selection | Line-of-sight deposition, uneven coatings on complex geometries |
Other Methods | Electroplating, Sol-Gel, Dip Coating, Spin Coating, Molecular Beam Epitaxy (MBE) | Polymers, coatings, semiconductor research | Simple, cost-effective, high-quality crystalline films | Limited to specific materials and applications |
Ready to choose the right thin film deposition method for your needs? Contact our experts today for personalized guidance!