Spark Plasma Sintering (SPS), also known as Field Assisted Sintering Technique (FAST) or Direct Current Sintering (DCS), is an advanced powder metallurgy sintering method that utilizes pulsed direct current (DC) to generate localized high temperatures and plasma between powder particles. This process facilitates rapid densification by melting and bonding particle interfaces through surface and boundary defect diffusion. SPS integrates plasma activation, hot pressing, and resistance heating, offering advantages such as fast heating, short sintering times, and energy efficiency. The method achieves high-density materials (over 99% in some cases) at lower temperatures compared to conventional sintering, making it suitable for ceramics, metals, and composites.
Key Points Explained:
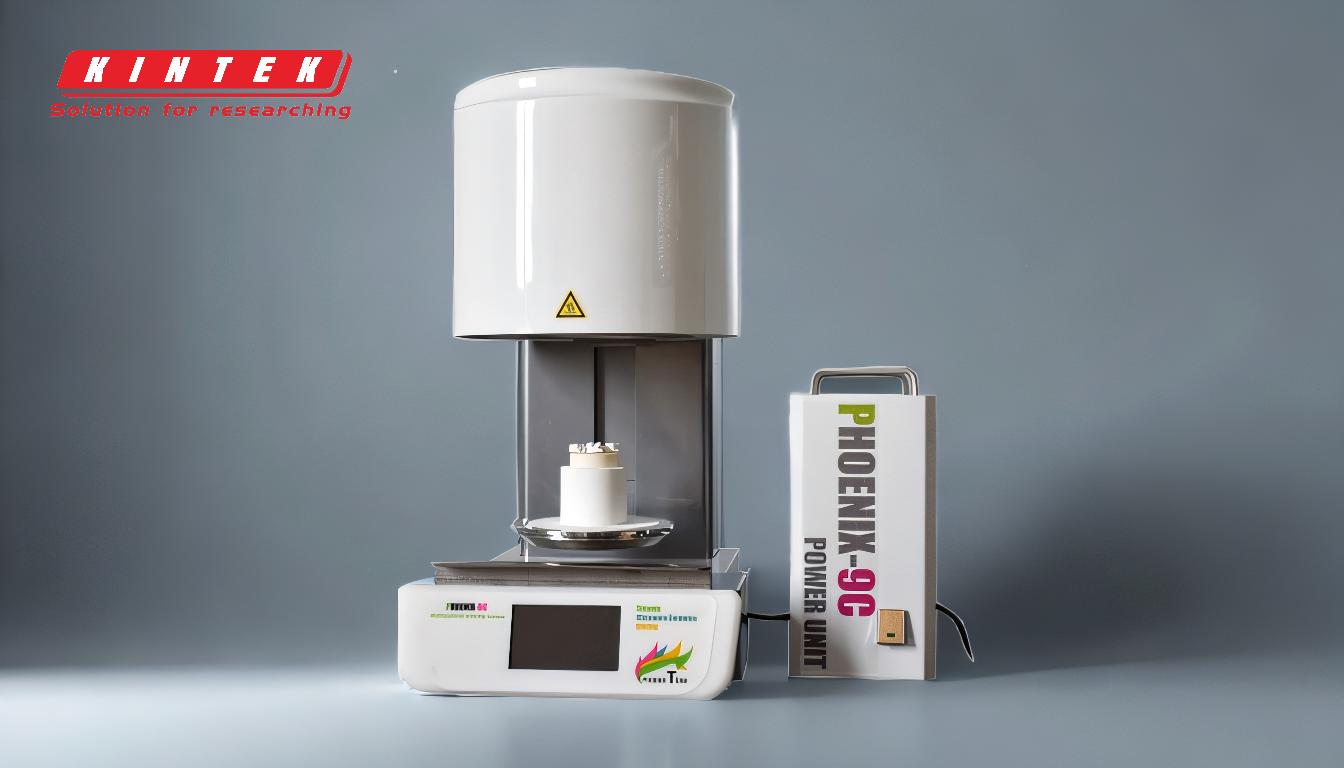
-
Principle of Spark Plasma Sintering (SPS):
- SPS operates on the principle of electric spark discharge, where a high-energy pulsed DC current is applied to the powder material.
- This generates localized high temperatures (up to 10,000°C) and plasma between particles, causing rapid heating and activation of particle surfaces.
-
Mechanism of Sintering:
- The pulsed current creates discharge plasma, which reduces the gap between particles and promotes surface diffusion and boundary defect diffusion.
- Particle surfaces melt and fuse, forming "necks" that grow over time, increasing the material's density to over 99% in some cases.
-
Role of Plasma and Joule Heating:
- Plasma activation cleans particle surfaces by oxidizing or evaporating contaminants, ensuring better bonding.
- Joule heating (resistance heating) occurs as the current passes through the conductive die and powder, providing both internal and external heating.
-
Integration of Hot Pressing:
- SPS combines plasma activation with mechanical pressure, applied through a graphite die, to enhance densification.
- This dual action allows sintering at lower temperatures and shorter times compared to conventional methods.
-
Advantages of SPS:
- Fast Heating and Cooling Rates: SPS enables rapid temperature changes, reducing processing time.
- Lower Sintering Temperatures: Materials can be sintered at temperatures hundreds of degrees lower than conventional methods.
- Energy Efficiency: The process consumes less energy due to shorter sintering times and lower temperatures.
- Controlled Microstructure: SPS allows precise control over material density and grain size, resulting in superior mechanical properties.
-
Applications of SPS:
- SPS is widely used for sintering ceramics, metals, and composite materials.
- It is particularly effective for materials that are difficult to sinter using traditional methods, such as nanostructured materials and high-performance alloys.
-
Alternative Names and Misconceptions:
- Despite its name, research suggests that plasma may not always be present in the process.
- Alternative names include Field Assisted Sintering Technique (FAST), Electric Field Assisted Sintering (EFAS), and Direct Current Sintering (DCS).
-
Equipment and Process Control:
- SPS requires specialized equipment, including a power control device that applies ON-OFF DC pulse voltage to the powder sample.
- The graphite die acts as both a pressure applicator and a heat source, ensuring uniform heating and densification.
By leveraging the unique combination of plasma activation, hot pressing, and resistance heating, Spark Plasma Sintering offers a highly efficient and versatile method for producing dense, high-performance materials with controlled microstructures.
Summary Table:
Aspect | Details |
---|---|
Principle | Uses pulsed DC to generate localized high temperatures and plasma. |
Mechanism | Melts and bonds particle interfaces via surface and boundary defect diffusion. |
Key Advantages | Fast heating, lower sintering temperatures, energy efficiency, and controlled microstructure. |
Applications | Ideal for ceramics, metals, composites, and nanostructured materials. |
Equipment | Requires specialized power control devices and graphite dies. |
Learn how Spark Plasma Sintering can optimize your material processing—contact us today!