The most commonly used filler metal in brazing is silver-based filler metal, often referred to as silver brazing alloys. These alloys are widely favored due to their excellent flow characteristics, strong joint strength, and versatility in joining a variety of base metals, including copper, brass, stainless steel, and nickel alloys. Silver brazing alloys typically contain silver, copper, and zinc, with additional elements like cadmium, nickel, or tin to enhance specific properties such as corrosion resistance or temperature tolerance. Their ability to create durable, leak-proof joints makes them indispensable in industries like HVAC, plumbing, automotive, and electronics. While other filler metals like aluminum-silicon or copper-phosphorus are used for specific applications, silver-based fillers remain the go-to choice for general-purpose brazing due to their reliability and performance.
Key Points Explained:
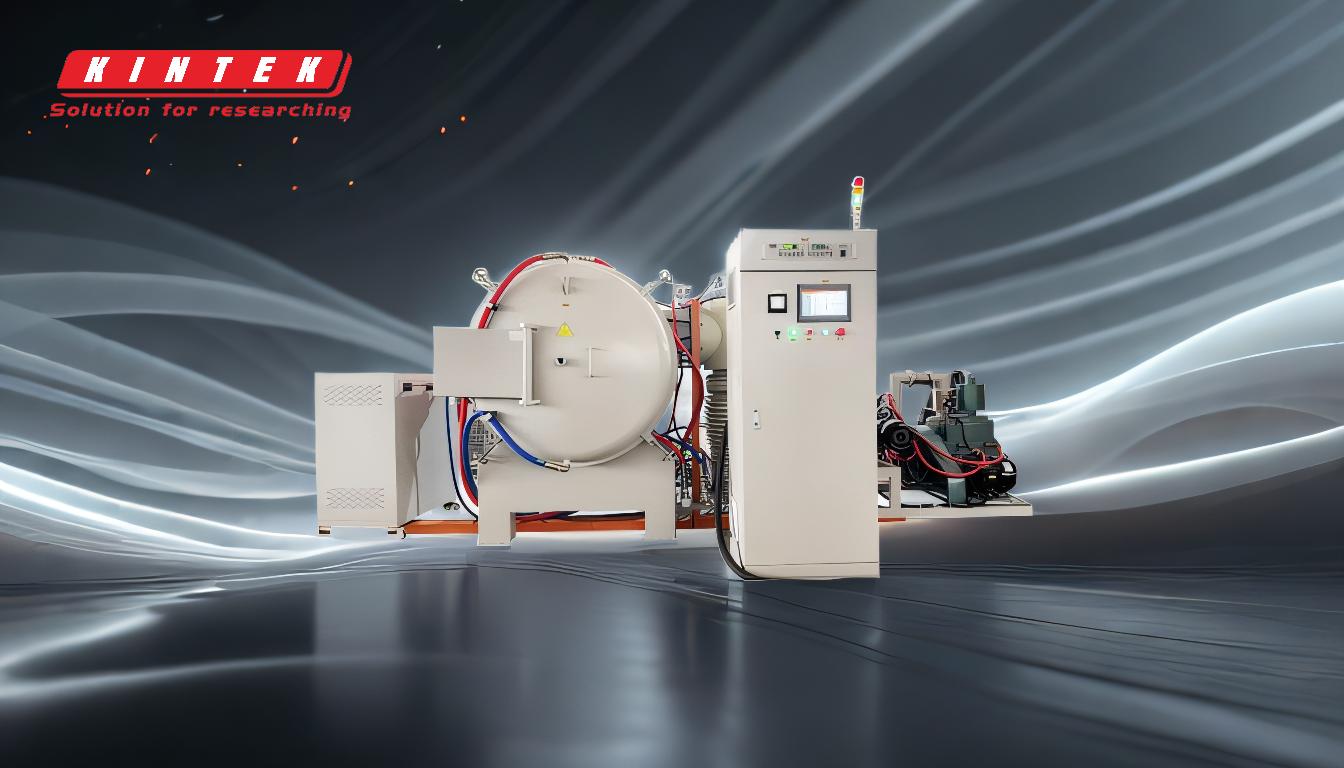
-
Silver-Based Filler Metals Are the Most Common
- Silver brazing alloys are the most widely used filler metals in brazing due to their versatility and performance.
- They are composed primarily of silver, copper, and zinc, with optional additions of elements like cadmium, nickel, or tin to improve specific properties.
-
Advantages of Silver Brazing Alloys
- Excellent Flow Characteristics: Silver-based fillers flow easily into tight joints, ensuring strong and uniform bonds.
- High Joint Strength: The resulting joints are mechanically strong and capable of withstanding stress and vibration.
- Corrosion Resistance: Alloys with added nickel or tin offer enhanced resistance to corrosion, making them suitable for harsh environments.
- Leak-Proof Seals: These alloys are ideal for applications requiring airtight or watertight seals, such as in plumbing or refrigeration systems.
-
Compatibility with Various Base Metals
- Silver brazing alloys can join a wide range of base metals, including copper, brass, stainless steel, and nickel alloys.
- This versatility makes them suitable for diverse industries, from HVAC and automotive to electronics and aerospace.
-
Comparison with Other Filler Metals
- Aluminum-Silicon Alloys: Used for brazing aluminum and its alloys, but not as versatile as silver-based fillers.
- Copper-Phosphorus Alloys: Commonly used for copper-to-copper joints, but limited in their ability to join dissimilar metals.
- Nickel-Based Alloys: Suitable for high-temperature applications, but more expensive and less user-friendly than silver-based fillers.
-
Applications of Silver Brazing Alloys
- HVAC and Refrigeration: Used for joining copper tubing and components in air conditioning and refrigeration systems.
- Plumbing: Ideal for creating leak-proof joints in water and gas pipelines.
- Automotive: Employed in manufacturing radiators, fuel lines, and other critical components.
- Electronics: Used for joining electrical contacts and connectors due to their excellent conductivity and reliability.
-
Environmental and Safety Considerations
- Some silver brazing alloys contain cadmium, which poses health and environmental risks. As a result, cadmium-free alternatives are increasingly preferred.
- Proper ventilation and safety precautions are essential when using silver brazing alloys to avoid exposure to harmful fumes.
-
Cost and Availability
- While silver-based filler metals are more expensive than some alternatives, their performance and reliability justify the cost.
- They are widely available in various forms, including rods, wires, and preforms, making them accessible for different brazing techniques.
In summary, silver-based filler metals dominate the brazing industry due to their unmatched combination of flowability, strength, and versatility. While other filler metals have their niche applications, silver brazing alloys remain the most commonly used and trusted choice for a wide range of brazing tasks.
Summary Table:
Key Feature | Details |
---|---|
Primary Composition | Silver, copper, zinc, with optional elements like cadmium, nickel, or tin |
Advantages | Excellent flow, high joint strength, corrosion resistance, leak-proof seals |
Compatible Base Metals | Copper, brass, stainless steel, nickel alloys |
Applications | HVAC, plumbing, automotive, electronics |
Environmental Notes | Cadmium-free options preferred; proper ventilation required |
Ready to optimize your brazing process? Contact our experts today to learn more!