A tube furnace is a specialized heating device designed for precise temperature control and uniform heating. It typically features a cylindrical cavity surrounded by heating coils embedded in a thermally insulating matrix. The furnace includes a working tube, often made of quartz or alumina, where materials are placed for heating. Temperature regulation is achieved through a thermocouple feedback system. The design can vary based on factors like process temperature, throughput, and atmosphere requirements. Additional components may include a vacuum pump, vacuum fittings, and advanced control systems for intelligent temperature adjustment and alarm functions.
Key Points Explained:
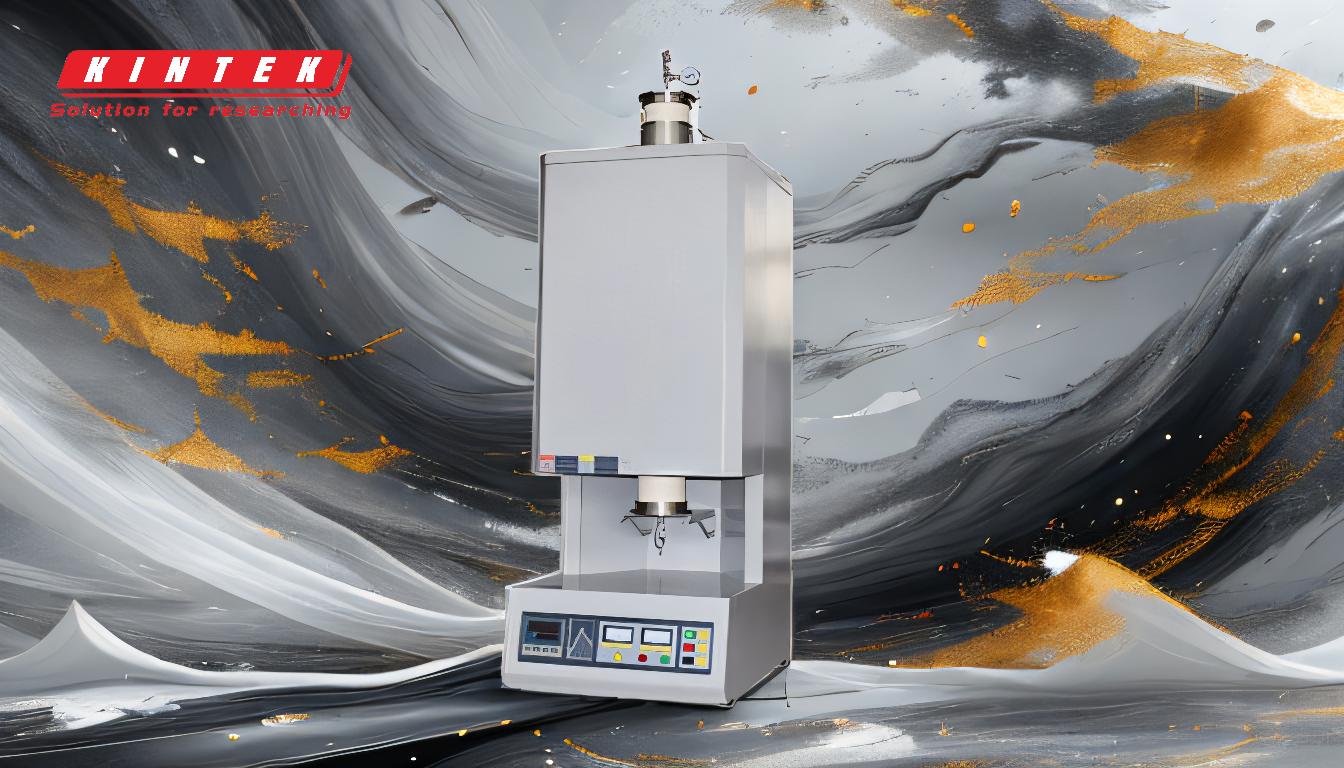
-
Cylindrical Cavity and Heating Coils:
- The core structure of a tube furnace is its cylindrical cavity, which is surrounded by heating coils. These coils are embedded in a thermally insulating matrix to ensure efficient heat retention and uniform temperature distribution.
-
Working Tube:
- Inside the cylindrical cavity, there is a working tube or vessel, typically made of quartz or alumina. This tube is where the materials to be heated are placed. The choice of material for the tube depends on the required temperature range and chemical resistance.
-
Temperature Control:
- Temperature regulation in a tube furnace is achieved through a feedback system using a thermocouple. This system ensures precise control over the heating process, allowing for consistent and accurate temperature maintenance.
-
Thermal Insulation:
- The furnace body is designed with thermal insulation to minimize heat loss and improve energy efficiency. This insulation is often made from materials like alumina ceramic fiber, which can withstand high temperatures.
-
Outer Shell and Hinges:
- The outer shell of the tube furnace is typically heavy-duty, providing structural integrity and protection for the internal components. Hinges are included to allow easy access to the working tube for loading and unloading materials.
-
Vacuum System:
- Some tube furnaces are equipped with a vacuum pump and vacuum fittings. This setup allows for the creation of a controlled atmosphere, which is essential for processes that require an inert or reducing environment.
-
Advanced Control Systems:
- Modern tube furnaces may include advanced control features such as intelligent adjustment algorithms, digital correction systems, and alarm functions. These features enhance the precision and safety of the heating process.
-
Design Variations:
- The design of a tube furnace can vary significantly based on specific application requirements. Factors influencing the design include process temperature, throughput, atmosphere requirements, material characteristics, and cooling needs.
By understanding these key points, a purchaser can make an informed decision when selecting a tube furnace that meets their specific needs, ensuring optimal performance and efficiency in their processes.
Summary Table:
Component | Description |
---|---|
Cylindrical Cavity | Surrounded by heating coils for uniform heating and heat retention. |
Working Tube | Made of quartz or alumina; holds materials for heating. |
Temperature Control | Uses a thermocouple feedback system for precise regulation. |
Thermal Insulation | Minimizes heat loss; often made of alumina ceramic fiber. |
Outer Shell and Hinges | Heavy-duty shell with hinges for easy access to the working tube. |
Vacuum System | Includes vacuum pump and fittings for controlled atmosphere processes. |
Advanced Control Systems | Features intelligent adjustment, digital correction, and alarm functions. |
Design Variations | Customizable based on temperature, throughput, atmosphere, and cooling needs. |
Looking for a tube furnace tailored to your needs? Contact us today for expert guidance!