Physical vapor deposition (PVD) is a vacuum-based coating technique used to deposit thin layers of material onto a substrate to enhance properties such as wear resistance, hardness, oxidation resistance, and lifespan. The process involves physically vaporizing the coating material, which then condenses onto the substrate. PVD is widely used in industries like aerospace, automotive, and electronics due to its ability to produce durable, high-quality coatings. The process is environmentally friendly and offers a wide range of material options and colors. PVD is distinct from chemical vapor deposition (CVD) in that it relies on physical means rather than chemical reactions to deposit materials.
Key Points Explained:
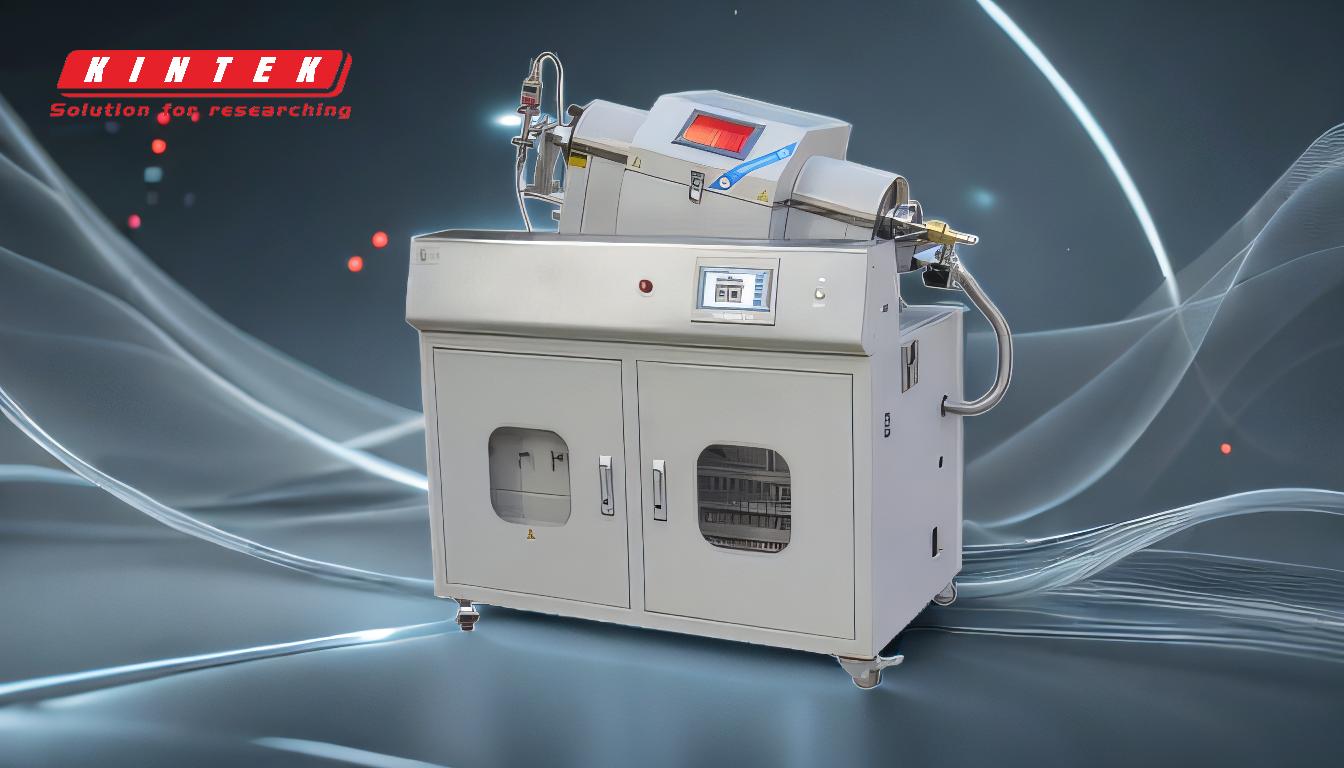
-
Definition and Purpose of PVD:
- Physical vapor deposition (PVD) is a vacuum-based process used to deposit thin layers of material onto a substrate. The primary purpose is to enhance surface properties such as wear resistance, hardness, oxidation resistance, and durability. This makes PVD coatings particularly valuable in industries like aerospace, automotive, and electronics.
-
Mechanism of PVD:
- PVD involves the physical transformation of a solid coating material into a vapor, which then condenses onto the substrate. This is achieved through methods like evaporation or sputtering, where the material is vaporized using high-energy sources such as heat or ion bombardment.
-
Types of PVD Processes:
- PVD processes are broadly categorized into two methods: sputtering and thermal processes. Thermal processes include:
- Vacuum evaporation
- Pulsed laser deposition (PLD)
- Molecular beam epitaxy (MBE)
- Ion plating
- Activated reactive evaporation (ARE)
- Ionized cluster beam deposition (ICBD)
- PVD processes are broadly categorized into two methods: sputtering and thermal processes. Thermal processes include:
-
Comparison with Chemical Vapor Deposition (CVD):
- Deposition Mechanism: PVD uses physical means (e.g., evaporation or sputtering) to deposit material, whereas CVD relies on chemical reactions between gases or vapors.
- Substrate Temperature: PVD typically does not require heating the substrate, while CVD often involves high temperatures to facilitate chemical reactions.
- Film Quality: PVD films tend to have better surface smoothness and adhesion, while CVD films are denser and offer better coverage.
- Deposition Rate: PVD generally has lower deposition rates compared to CVD.
- Material Range: Both methods can deposit a wide range of materials, but CVD is particularly suited for metals, semiconductors, and ceramics.
- Production Suitability: PVD is often preferred for high-volume production due to its higher deposition rates and ability to coat large areas.
-
Advantages of PVD:
- Durability: PVD coatings are highly durable and provide excellent wear and corrosion resistance.
- Aesthetic Flexibility: PVD can produce coatings in a wide range of colors, making it suitable for decorative applications.
- Environmental Friendliness: The process is environmentally sound, as it does not involve harmful chemicals or produce significant waste.
- Enhanced Properties: PVD coatings improve the chemical resistance, wear resistance, and lifespan of products.
-
Applications of PVD:
- PVD is used in various industries for applications such as:
- Coating cutting tools to improve wear resistance.
- Enhancing the durability of automotive components.
- Providing decorative finishes on consumer electronics.
- Improving the performance of aerospace components.
- PVD is used in various industries for applications such as:
-
Historical Context and Technological Evolution:
- The PVD process has been known for over 100 years. In the last 30 years, plasma-assisted PVD (PAPVD) has emerged, incorporating technologies like direct current (DC) diode, triode, radio-frequency (RF), pulsed plasma, and ion beam-assisted coatings.
-
Equipment and Setup:
- A typical PVD setup includes a vacuum chamber, a high-voltage DC power supply, and a substrate connected to the negative voltage of the power supply. The target material is vaporized using a high-energy source, and the vaporized atoms condense on the substrate to form a thin film.
By understanding these key points, one can appreciate the versatility and effectiveness of PVD as a coating technology, making it a preferred choice for various industrial applications.
Summary Table:
Aspect | Details |
---|---|
Definition | Vacuum-based process to deposit thin material layers for enhanced properties. |
Mechanism | Physical vaporization and condensation of coating material onto substrates. |
Types of Processes | Sputtering, vacuum evaporation, pulsed laser deposition, ion plating, etc. |
Advantages | Durable, eco-friendly, aesthetic flexibility, enhanced wear and corrosion resistance. |
Applications | Aerospace, automotive, electronics, cutting tools, decorative finishes. |
Comparison with CVD | PVD uses physical means; CVD relies on chemical reactions. |
Discover how PVD coatings can elevate your product performance—contact our experts today!