Physical Vapor Deposition (PVD) is a sophisticated coating technique used to deposit thin films of material onto a substrate. The process involves converting a solid target material into a vapor phase, which then condenses onto the substrate to form a thin, durable, and often highly specialized coating. PVD is widely used in industries such as electronics, optics, and manufacturing due to its ability to produce coatings with excellent adhesion, high purity, and resistance to wear and corrosion. The method is versatile, allowing for the deposition of a wide range of materials, including metals, ceramics, and composites, and can be tailored to achieve specific properties such as hardness, conductivity, or optical characteristics.
Key Points Explained:
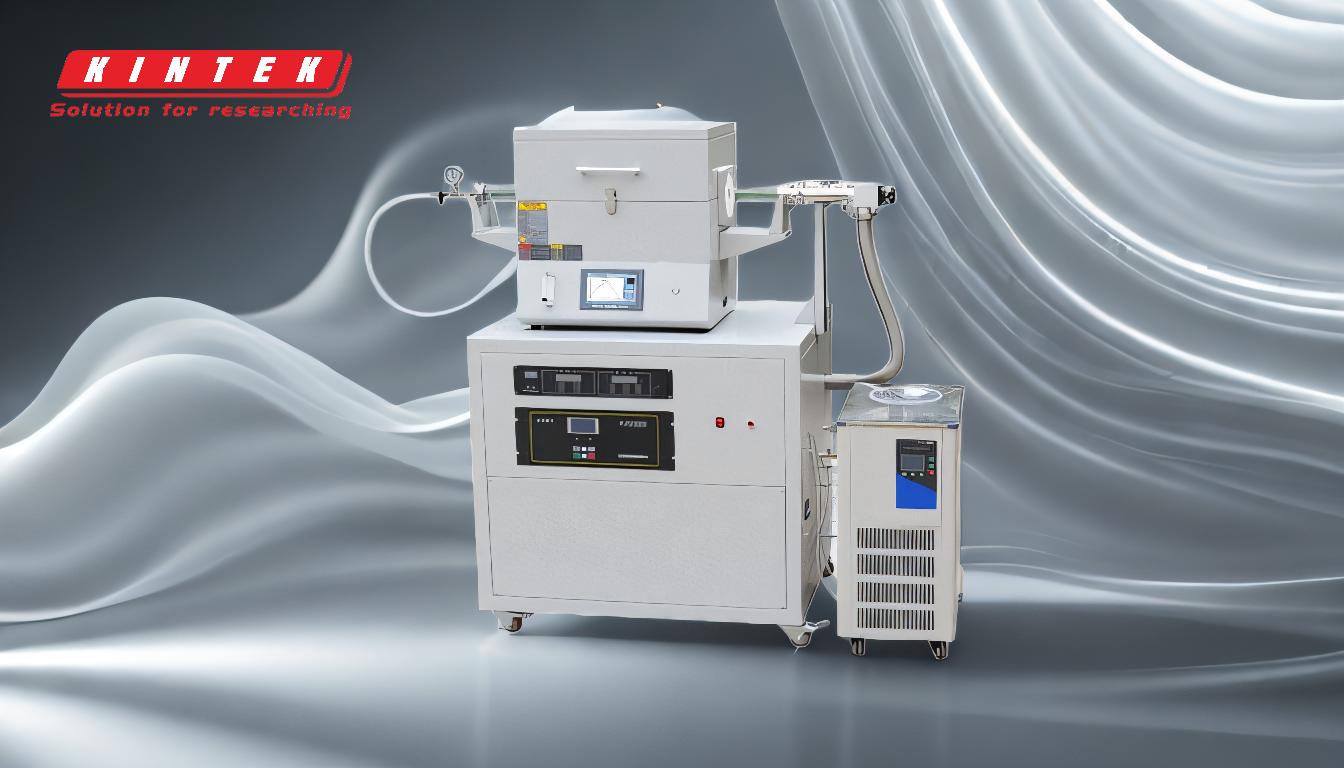
-
Basic Principle of PVD:
- PVD involves the transition of a solid material into a vapor phase, which then condenses onto a substrate to form a thin film.
- The process typically occurs in a vacuum chamber to minimize contamination and control the deposition environment.
-
Conversion of Solid to Vapor:
- The solid target material is converted into a vapor phase using various methods such as thermal evaporation, sputtering, or laser ablation.
- In thermal evaporation, the material is heated until it vaporizes.
- In sputtering, high-energy ions bombard the target material, dislodging atoms that then travel through the chamber and deposit onto the substrate.
-
Deposition onto Substrate:
- The vaporized material travels through the reaction chamber and condenses onto the substrate, forming a thin film.
- The deposition process is often "line-of-sight," meaning the atoms travel in a straight line from the target to the substrate, which can limit the coating of complex geometries.
-
Types of PVD Techniques:
- Thermal Evaporation: Involves heating the target material until it evaporates. This method is suitable for materials with lower melting points.
- Sputtering: Uses a plasma discharge to bombard the target material, causing atoms to be ejected and deposited onto the substrate. This method is more versatile and can handle materials with higher melting points.
- Laser Ablation: A laser is used to vaporize the target material, which is then deposited onto the substrate. This method is particularly useful for depositing complex materials like ceramics.
-
Process Conditions:
- PVD is typically carried out in a vacuum chamber to prevent contamination and ensure a controlled environment.
- The temperature in the chamber can range from 50 to 600 degrees Celsius, depending on the material and the desired properties of the coating.
- The process often involves the use of inert gases to facilitate the vaporization and deposition processes.
-
Advantages of PVD:
- High Adhesion: PVD coatings are known for their excellent adhesion to the substrate, which is crucial for durability and performance.
- Material Versatility: PVD can deposit a wide range of materials, including metals, ceramics, and composites, making it suitable for various applications.
- High Purity: The vacuum environment minimizes contamination, resulting in high-purity coatings.
- Durability: PVD coatings are highly durable, resistant to wear, corrosion, and high temperatures, making them ideal for harsh environments.
-
Applications of PVD:
- Electronics: Used to deposit thin films for semiconductors, solar cells, and display technologies.
- Optics: Applied in the production of anti-reflective coatings, mirrors, and optical filters.
- Manufacturing: Used to coat cutting tools, molds, and other components to enhance their wear resistance and lifespan.
- Medical Devices: PVD coatings are used on implants and surgical instruments to improve biocompatibility and durability.
-
Challenges and Considerations:
- Complex Geometries: The line-of-sight nature of PVD can make it difficult to coat complex or intricate shapes uniformly.
- Cost: The equipment and process can be expensive, particularly for large-scale or high-throughput applications.
- Material Limitations: Some materials may not be suitable for certain PVD techniques due to their melting points or other physical properties.
In summary, Physical Vapor Deposition is a versatile and highly effective technique for depositing thin films with excellent properties. Its ability to handle a wide range of materials and produce durable, high-performance coatings makes it a valuable process in many industries. However, the method does have some limitations, particularly in terms of cost and the ability to coat complex geometries.
Summary Table:
Aspect | Details |
---|---|
Basic Principle | Converts solid material into vapor, condenses onto substrate to form a film. |
Key Techniques | Thermal evaporation, sputtering, laser ablation. |
Process Conditions | Vacuum chamber, 50–600°C, inert gases. |
Advantages | High adhesion, material versatility, high purity, durability. |
Applications | Electronics, optics, manufacturing, medical devices. |
Challenges | Complex geometries, high cost, material limitations. |
Learn how PVD can enhance your projects—contact our experts today!