Physical Vapor Deposition (PVD) is a highly effective technique for providing corrosion protection to metal products. It involves depositing a thin, durable, and corrosion-resistant coating onto a substrate under vacuum conditions. PVD coatings enhance the lifespan, durability, and performance of materials by improving properties such as wear resistance, oxidation resistance, and hardness. Unlike other coating methods like electroplating or Chemical Vapor Deposition (CVD), PVD uses solid-state materials, making it more environmentally friendly and capable of producing coatings with superior corrosion tolerance. This technique is widely used in industries such as aerospace, biomedical, semiconductor manufacturing, and decorative coatings, where corrosion resistance and material longevity are critical.
Key Points Explained:
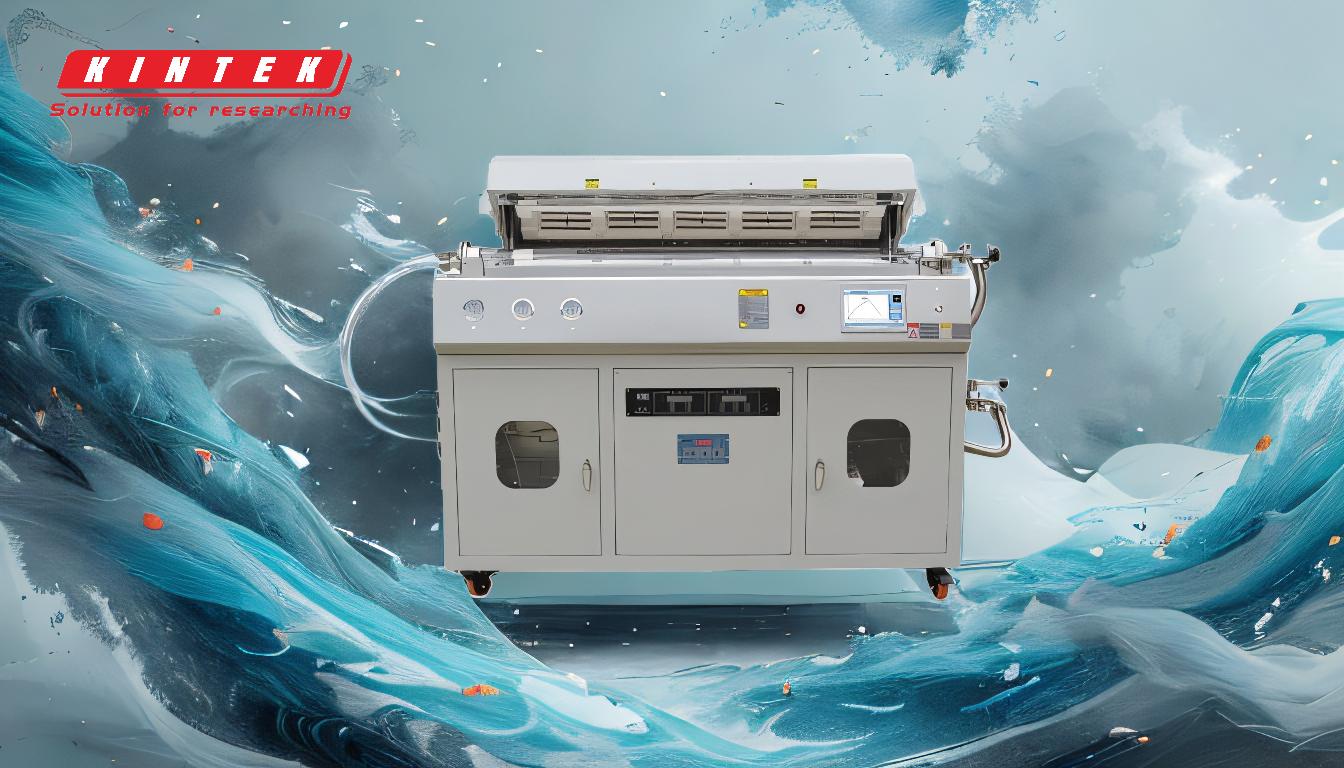
-
What is PVD?
- Physical Vapor Deposition (PVD) is a vacuum-based coating process where solid-state materials are vaporized and deposited onto a substrate to form a thin, protective layer.
- It is used to enhance the properties of materials, including corrosion resistance, wear resistance, oxidation resistance, and hardness.
- Unlike Chemical Vapor Deposition (CVD), which uses gaseous precursors, PVD relies on solid materials, making it more environmentally friendly and versatile.
-
How PVD Provides Corrosion Protection:
- PVD coatings create a barrier between the substrate material and the external environment, preventing direct contact with corrosive agents like moisture, chemicals, or oxygen.
- The coatings are highly dense and uniform, ensuring complete coverage and minimal defects that could lead to corrosion initiation.
- Materials commonly used in PVD for corrosion protection include titanium nitride (TiN), chromium nitride (CrN), and aluminum-based coatings, which are inherently resistant to oxidation and chemical attack.
-
Advantages of PVD for Corrosion Protection:
- Superior Corrosion Tolerance: PVD coatings offer higher corrosion resistance compared to traditional methods like electroplating, making them ideal for harsh environments.
- Durability: The coatings are extremely hard and wear-resistant, ensuring long-term protection even under mechanical stress.
- Environmental Benefits: PVD is a clean process that produces minimal waste and does not involve hazardous chemicals, unlike electroplating.
- Versatility: PVD can be applied to a wide range of materials, including metals, ceramics, and polymers, making it suitable for diverse applications.
-
Applications of PVD in Corrosion Protection:
- Aerospace Industry: PVD coatings are used on aircraft components to protect against corrosion caused by exposure to extreme temperatures, humidity, and saltwater.
- Biomedical Field: Implants and surgical tools are coated with PVD to prevent corrosion and improve biocompatibility.
- Cutting Tools: Tools coated with PVD (e.g., titanium nitride) exhibit enhanced wear and corrosion resistance, extending their lifespan in metalworking applications.
- Decorative Coatings: Jewelry and watches use PVD coatings to provide both aesthetic appeal and corrosion resistance.
- Semiconductor Devices: PVD is used to deposit corrosion-resistant layers on semiconductor components, ensuring reliability in electronic applications.
-
Comparison with Other Coating Techniques:
- Electroplating: PVD offers better adhesion, uniformity, and corrosion resistance compared to electroplating, which can produce porous coatings prone to corrosion.
- Chemical Vapor Deposition (CVD): While CVD provides excellent coating quality, it requires high temperatures and gaseous precursors, making it less suitable for temperature-sensitive materials. PVD, on the other hand, operates at lower temperatures and uses solid materials, making it more versatile.
-
Process of PVD Coating:
- Vacuum Environment: The process occurs in a vacuum chamber to prevent contamination and ensure high-quality coatings.
- Vaporization: The coating material (target) is vaporized using techniques like sputtering, evaporation, or arc vaporization.
- Deposition: The vaporized material condenses onto the substrate, forming a thin, uniform layer.
- Post-Treatment: Some PVD coatings may undergo additional treatments (e.g., annealing) to further enhance their properties.
-
Materials Used in PVD for Corrosion Protection:
- Titanium Nitride (TiN): Provides excellent hardness and corrosion resistance, commonly used in cutting tools and decorative coatings.
- Chromium Nitride (CrN): Known for its high oxidation resistance and durability, ideal for aerospace and biomedical applications.
- Aluminum-Based Coatings: Offer superior corrosion resistance, often used in marine and automotive industries.
-
Challenges and Considerations:
- Cost: PVD equipment and processes can be expensive, making it less suitable for low-cost applications.
- Complexity: The process requires precise control of parameters like temperature, pressure, and deposition rate to achieve optimal results.
- Substrate Compatibility: Not all materials are suitable for PVD coating, and surface preparation is critical to ensure adhesion and performance.
By leveraging the unique advantages of PVD, industries can significantly improve the corrosion resistance and longevity of their products, ensuring reliability and performance in demanding environments.
Summary Table:
Aspect | Details |
---|---|
Process | Vacuum-based coating using solid-state materials |
Key Benefits | Superior corrosion resistance, durability, environmental friendliness |
Common Materials | Titanium Nitride (TiN), Chromium Nitride (CrN), Aluminum-based coatings |
Applications | Aerospace, biomedical, cutting tools, decorative coatings, semiconductors |
Comparison with Others | Better adhesion and corrosion resistance than electroplating and CVD |
Challenges | High cost, process complexity, substrate compatibility |
Interested in enhancing your product's corrosion resistance? Contact us today to learn more about PVD solutions!