The plasma pressure for sputtering typically ranges from 5–30 mTorr (millitorr), depending on the specific sputtering conditions and desired outcomes. This pressure range is crucial for achieving effective sputtering, as it ensures that energetic particles sputtered or reflected from the target are "thermalized" through gas-phase collisions before reaching the substrate. This thermalization process is essential for controlling the energy and direction of the deposited particles, which directly impacts the quality and uniformity of the thin film. The pressure is maintained within a vacuum chamber, where inert gases like argon are ionized to create the plasma necessary for the sputtering process.
Key Points Explained:
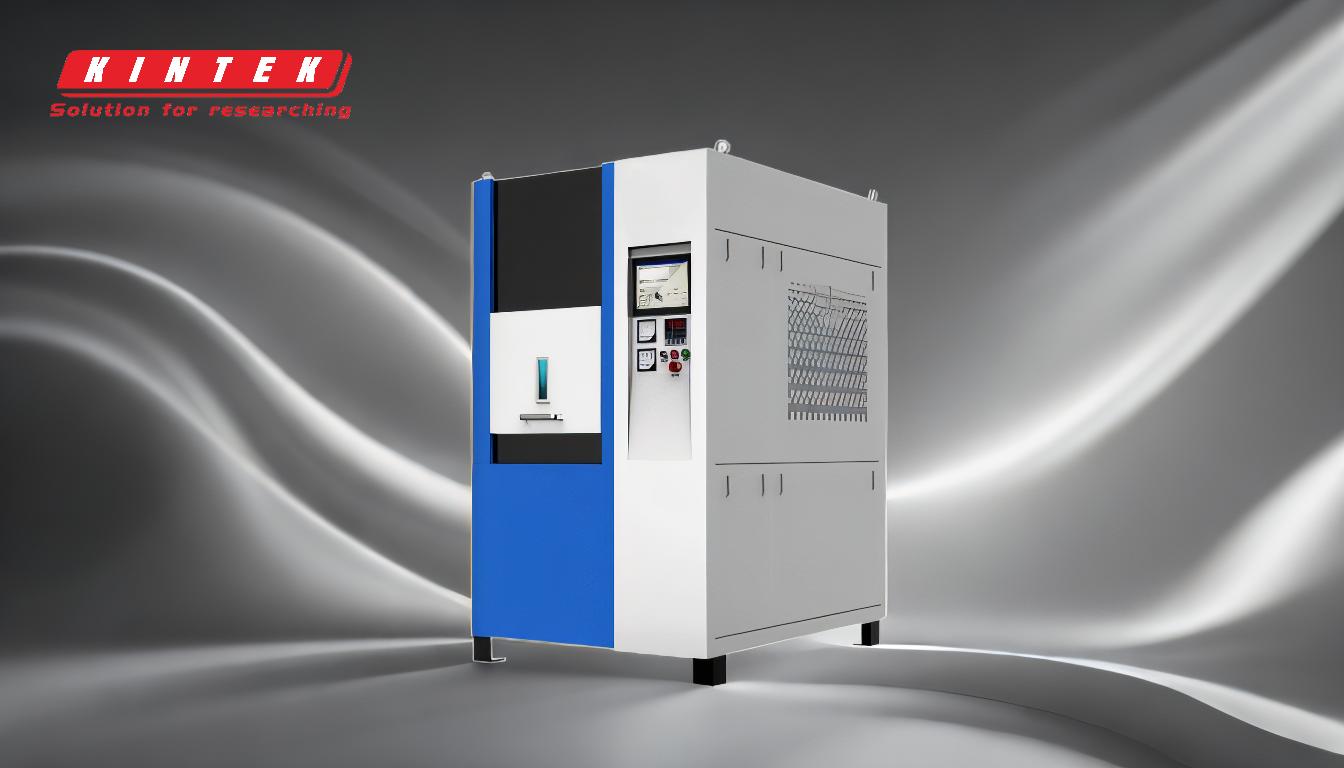
-
Plasma Pressure Range for Sputtering:
- The typical plasma pressure for sputtering ranges from 5–30 mTorr.
- This range is optimal for ensuring that sputtered particles are thermalized through collisions with gas atoms before reaching the substrate.
- Thermalization reduces the kinetic energy of the particles, allowing for more controlled and uniform deposition.
-
Role of Inert Gas and Plasma Formation:
- Inert gases like argon are introduced into the vacuum chamber to create the plasma.
- The gas is ionized using a high voltage (3–5 kV) or electromagnetic excitation, forming Ar+ ions.
- These ions are accelerated toward the target (cathode), where they collide and eject target atoms, initiating the sputtering process.
-
Importance of Vacuum Conditions:
- The sputtering process begins by creating a vacuum in the chamber, typically around 1 Pa (0.0000145 psi), to remove moisture and impurities.
- Lower pressures are initially used to avoid contamination from residual gases before introducing argon at higher pressures.
-
Thermalization of Sputtered Particles:
- At higher gas pressures (e.g., 5–30 mTorr), sputtered ions collide with gas atoms, causing them to lose energy and move diffusively.
- This random walk motion ensures that particles reach the substrate with controlled energy, improving film quality and coverage.
-
Impact of Pressure on Deposition:
- Higher pressures improve coverage by ensuring particles are evenly distributed across the substrate.
- Lower pressures allow for high-energy ballistic impacts, which may be desirable for specific applications requiring high-energy deposition.
-
Factors Influencing Sputtering Yield:
- The sputtering yield (number of target atoms ejected per incident ion) depends on factors such as:
- Incident ion energy.
- Mass of the ions and target atoms.
- Angle of incidence.
- These factors vary depending on the target material and sputtering conditions.
- The sputtering yield (number of target atoms ejected per incident ion) depends on factors such as:
-
Magnetic Field and Confinement:
- A magnetic field is often used to confine the plasma around the target, increasing the density of Ar+ ions and enhancing the sputtering efficiency.
- This magnetic confinement is critical for maintaining a stable plasma and improving deposition rates.
-
Practical Considerations for Equipment and Consumables:
- When selecting equipment, consider the pressure range and compatibility with inert gases like argon.
- Ensure the vacuum pump can achieve and maintain the required pressures (1 Pa to 30 mTorr).
- Choose a power source (DC or RF) that aligns with the desired deposition rate and material compatibility.
By understanding these key points, equipment and consumable purchasers can make informed decisions about the sputtering process, ensuring optimal performance and high-quality thin film deposition.
Summary Table:
Key Aspect | Details |
---|---|
Plasma Pressure Range | 5–30 mTorr |
Inert Gas Used | Argon |
Vacuum Chamber Pressure | ~1 Pa (0.0000145 psi) |
Thermalization Process | Ensures controlled energy and direction of deposited particles |
Magnetic Field Role | Confines plasma, increases Ar+ ion density, and enhances sputtering efficiency |
Equipment Considerations | Vacuum pump, power source (DC/RF), and compatibility with inert gases |
Ready to optimize your sputtering process? Contact our experts today for tailored solutions!