The pressure range for pyrolysis varies depending on the type of pyrolysis process and the desired end products. Generally, pyrolysis processes involving liquid and gaseous species are conducted at pressures between 1-30 bar. Fast pyrolysis, which aims to maximize bio-oil production, typically operates at moderate pressures, while slow pyrolysis is usually conducted at atmospheric pressure. The choice of pressure, along with temperature, heating rate, and residence time, significantly influences the efficiency and output of the pyrolysis process.
Key Points Explained:
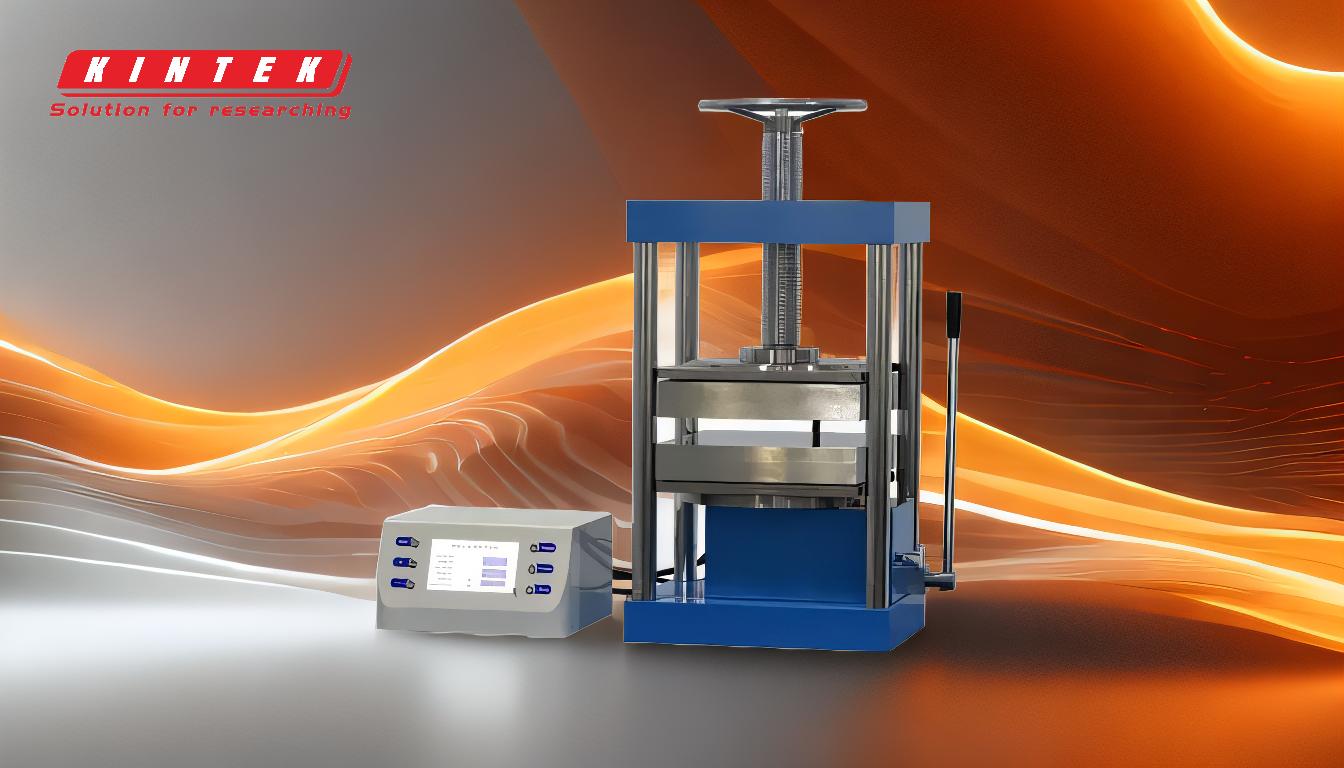
-
General Pressure Range for Pyrolysis:
- Pyrolysis processes involving liquid and gaseous species are typically carried out at pressures between 1-30 bar. This range is suitable for various pyrolysis types, including fast and slow pyrolysis, depending on the specific requirements of the process and the desired end products.
-
Fast Pyrolysis Pressure Conditions:
- Fast pyrolysis is optimized for high bio-oil yields and is typically conducted at moderate pressures. The process involves rapid heating rates (1000 °C/s) and short residence times to maximize the production of bio-oil. While the references do not specify exact pressure values for fast pyrolysis, it is generally understood to operate within the broader 1-30 bar range, often closer to atmospheric pressure to facilitate rapid heating and quenching.
-
Slow Pyrolysis Pressure Conditions:
- Slow pyrolysis is usually conducted at atmospheric pressure. This process involves slower heating rates (1-30 °C/min) and longer residence times, which are conducive to producing higher yields of bio-char. The atmospheric pressure condition simplifies the reactor design and operation, making it more accessible for smaller-scale applications.
-
Pressure's Role in Pyrolysis:
- Pressure is a critical parameter in pyrolysis as it influences the thermal degradation of organic materials and the distribution of end products. Higher pressures can enhance the breakdown of complex molecules and improve the yield of certain products like syngas. However, excessively high pressures may increase operational costs and complexity, making it essential to balance pressure with other process parameters like temperature and heating rate.
-
Interaction Between Pressure and Temperature:
- The pressure range for pyrolysis is closely linked to the temperature range. For instance, fast pyrolysis operates at temperatures around 500 °C, while slow pyrolysis occurs at lower temperatures, typically between 350°C–550°C. The pressure must be adjusted to complement the temperature to achieve optimal product yields and process efficiency.
-
Practical Considerations for Equipment Purchasers:
- When selecting pyrolysis equipment, purchasers should consider the pressure range required for their specific application. For fast pyrolysis aimed at bio-oil production, equipment capable of handling moderate pressures and rapid heating rates is essential. For slow pyrolysis focused on bio-char production, simpler, atmospheric pressure systems may suffice. Additionally, the choice of reactor material (e.g., refractory alloys) and design (e.g., long, thin reactor tubes) should align with the intended pressure and temperature conditions.
By understanding these key points, equipment and consumable purchasers can make informed decisions about the appropriate pressure range and associated parameters for their pyrolysis processes, ensuring optimal performance and product yields.
Summary Table:
Pyrolysis Type | Pressure Range | Key Characteristics |
---|---|---|
General Pyrolysis | 1-30 bar | Suitable for liquid and gaseous species production. |
Fast Pyrolysis | Moderate pressures | Optimized for bio-oil; rapid heating rates (1000 °C/s) and short residence times. |
Slow Pyrolysis | Atmospheric | Focused on bio-char; slower heating rates (1-30 °C/min) and longer residence times. |
Pressure Role | Varies | Influences thermal degradation, product distribution, and operational efficiency. |
Need help selecting the right pyrolysis equipment for your pressure and temperature needs? Contact our experts today!