The Chemical Vapor Deposition (CVD) process is a method used to produce high-quality, high-performance solid materials, typically in the form of thin films. The process involves introducing precursor gases into a reaction chamber where they chemically react on a heated substrate, leading to the deposition of a thin film. The key factors influencing the CVD process include temperature, pressure, gas flow rates, and the nature of the precursor gases. The process is widely used in industries such as semiconductor manufacturing, optics, and materials science due to its ability to produce uniform and high-purity coatings.
Key Points Explained:
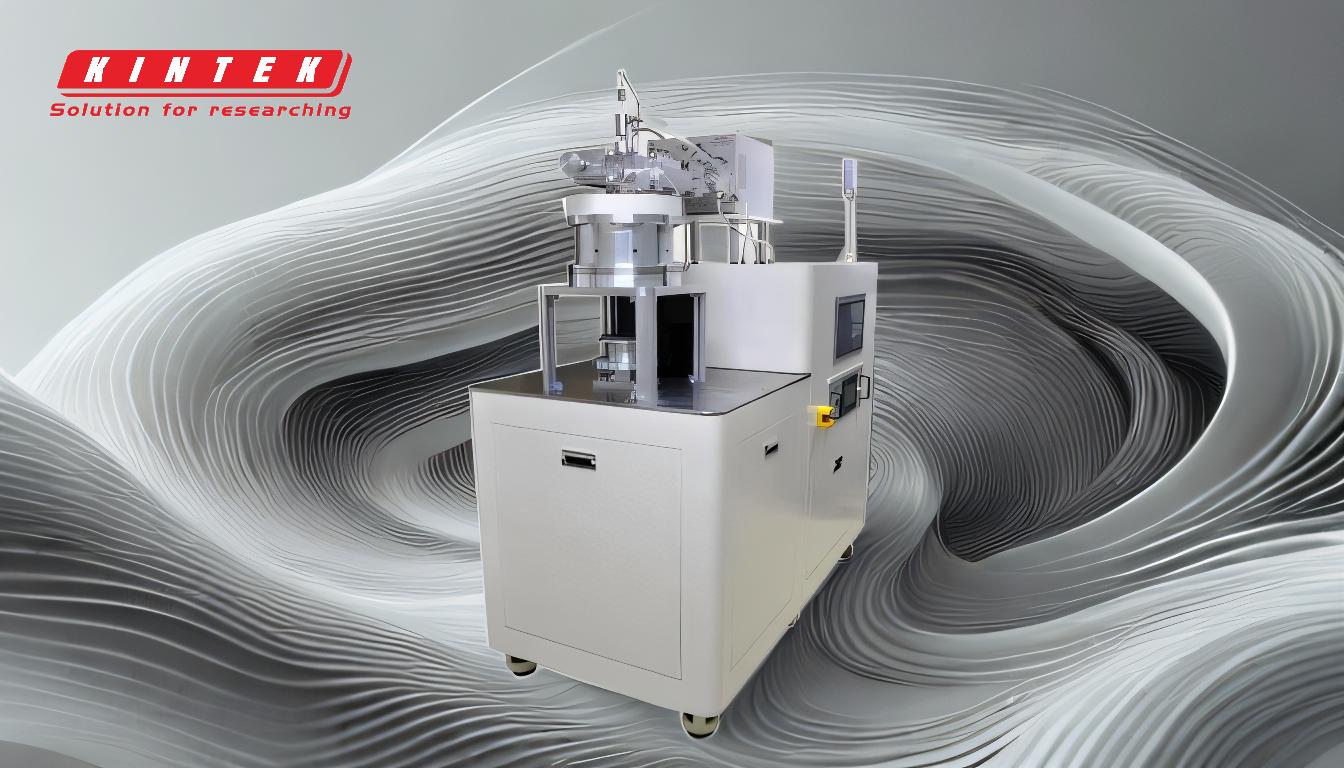
-
Introduction of Precursor Gases:
- The CVD process begins by introducing precursor gases into a reaction chamber. These gases contain the constituent atoms or molecules of the material to be deposited. For example, in the case of diamond synthesis, gases such as carbon, hydrogen, and oxygen are used.
- The precursor gases are often mixed with carrier gases to facilitate their flow into the chamber.
-
Heating the Substrate:
- The substrate, which is the material to be coated, is heated to a specific temperature, typically ranging from 800°C to 1400°C. This heating can be achieved using various methods such as microwaves, lasers, or hot filaments.
- The temperature of the substrate is crucial as it determines the type of chemical reactions that will occur and the quality of the deposited film.
-
Chemical Reactions:
- Once the precursor gases come into contact with the heated substrate, chemical reactions occur either on the substrate surface or in the vapor phase near the substrate. These reactions can be thermal, plasma-assisted, or photo-induced, depending on the specific CVD technique used.
- The chemical reactions result in the formation of reactive radicals or ions, which then deposit onto the substrate to form a thin film.
-
Deposition of Thin Film:
- The reactive species generated from the chemical reactions deposit onto the substrate, forming a thin film. This film can be crystalline, amorphous, or a combination of both, depending on the process conditions and the nature of the precursor gases.
- The deposition process is atomistic, meaning that the primary species deposited are atoms, molecules, or a combination of both.
-
Control of Process Parameters:
- The deposition rate and the quality of the thin film are highly dependent on several process parameters, including:
- Temperature: Higher temperatures generally increase the reaction rate and can improve the quality of the film.
- Pressure: The pressure inside the reaction chamber affects the mean free path of the gas molecules and the rate of chemical reactions.
- Flow Rate: The flow rate of the precursor gases influences the concentration of reactive species and the uniformity of the film.
- Gas Composition: The specific combination of precursor gases and their concentrations determine the chemical reactions and the properties of the deposited film.
- The deposition rate and the quality of the thin film are highly dependent on several process parameters, including:
-
Removal of Waste Gases:
- After the chemical reactions and deposition occur, the waste gases and by-products are pumped out of the reaction chamber. This step is essential to maintain the purity of the deposition environment and to prevent contamination of the thin film.
-
Applications and Advantages:
- CVD is widely used in various industries due to its ability to produce high-quality, uniform, and high-purity coatings. Some common applications include:
- Semiconductor Manufacturing: CVD is used to deposit thin films of silicon, silicon dioxide, and other materials onto semiconductor wafers.
- Optics: CVD is used to create anti-reflective coatings, optical filters, and other optical components.
- Materials Science: CVD is used to synthesize advanced materials such as graphene, carbon nanotubes, and diamond films.
- The advantages of CVD include the ability to deposit films with excellent conformality, high purity, and precise control over film properties.
- CVD is widely used in various industries due to its ability to produce high-quality, uniform, and high-purity coatings. Some common applications include:
-
Comparison with Physical Vapor Deposition (PVD):
- Unlike PVD, which involves physical processes such as evaporation, sputtering, or sublimation, CVD relies on chemical reactions to deposit thin films. This distinction allows CVD to produce films with unique properties and compositions that are difficult to achieve with PVD.
In summary, the CVD process is a versatile and powerful technique for depositing thin films through chemical reactions in a controlled environment. By carefully managing the process parameters, it is possible to produce high-quality films with precise properties, making CVD an essential tool in modern materials science and engineering.
Summary Table:
Key Aspect | Details |
---|---|
Precursor Gases | Introduced into a reaction chamber; contain atoms/molecules for deposition. |
Substrate Heating | Heated to 800°C–1400°C; critical for chemical reactions and film quality. |
Chemical Reactions | Occur on the substrate or in the vapor phase; form reactive species. |
Thin Film Deposition | Reactive species deposit to form crystalline, amorphous, or mixed films. |
Process Parameters | Temperature, pressure, flow rate, and gas composition control film quality. |
Applications | Semiconductor manufacturing, optics, and advanced materials synthesis. |
Advantages | High purity, uniformity, and precise control over film properties. |
Discover how the CVD process can elevate your material science projects—contact us today for expert guidance!