The process of evaporation coating is a Physical Vapor Deposition (PVD) technique used to create thin, uniform layers of material on a substrate. It involves heating a source material to its evaporation point in a high-vacuum environment, causing it to vaporize and then condense onto the target object. This method ensures a clean, precise, and high-quality coating, often used in industries like electronics, optics, and aerospace. The process relies on maintaining a vacuum to minimize contamination and ensure proper adhesion of the coating material to the substrate.
Key Points Explained:
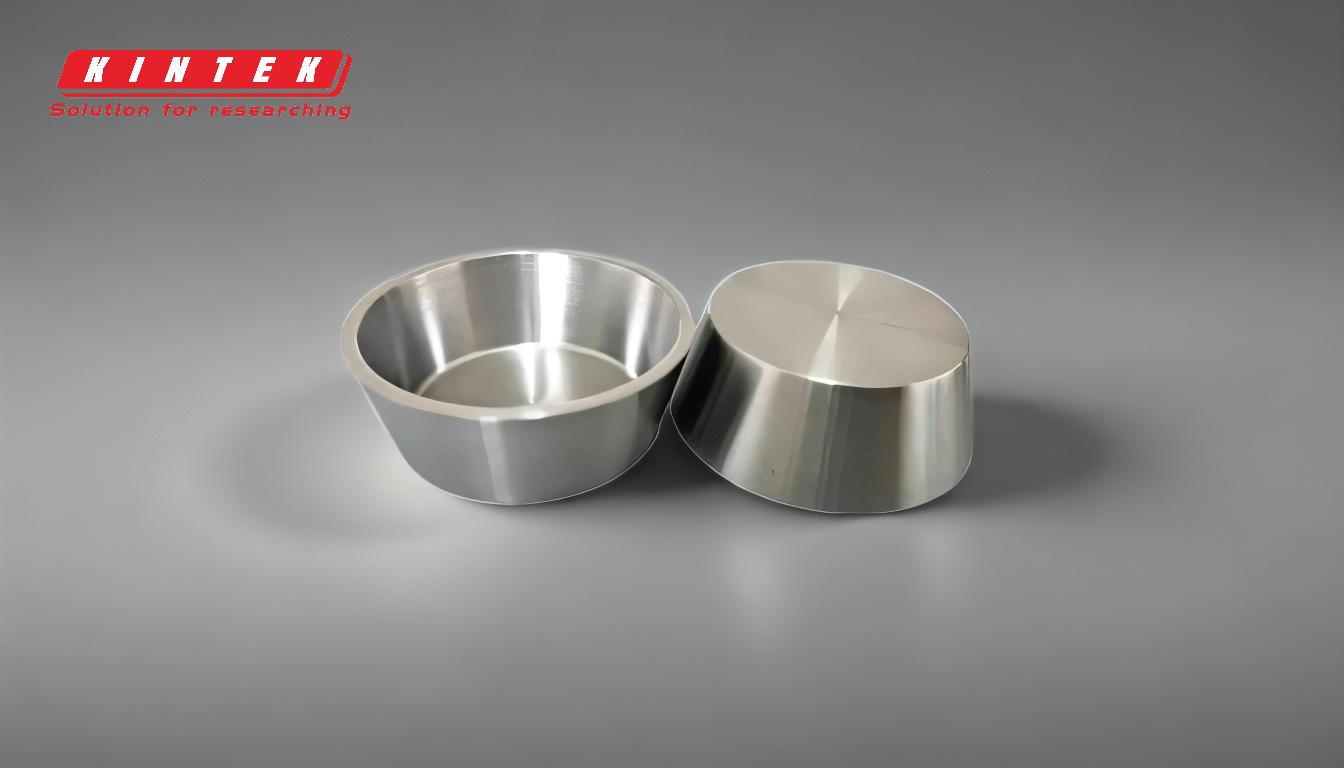
-
Preparation of the Vacuum Chamber:
- The process begins by placing the substrate (target object) and the source material inside a high-vacuum chamber.
- A vacuum pump removes air and other gases to create a low-pressure environment, reducing the likelihood of gas collisions and contamination.
- This step is critical to ensure the purity of the coating and to provide a clear path for the vaporized material to travel.
-
Heating the Source Material:
- The source material (e.g., metal, alloy, or compound) is heated to its melting or evaporation point using methods such as resistive heating, electron beam heating, or induction heating.
- As the material heats, it transitions from a solid to a vapor state, releasing atoms or molecules into the chamber.
- The temperature must be carefully controlled to achieve consistent evaporation and prevent overheating, which could damage the material or the chamber.
-
Vaporization and Deposition:
- Once vaporized, the material forms a vapor stream that travels through the vacuum chamber.
- The vaporized atoms or molecules condense onto the substrate, forming a thin, uniform coating.
- The coating adheres to the substrate due to the high-energy state of the vapor particles and the controlled substrate temperature, which promotes strong bonding.
-
Role of the Substrate Temperature:
- The substrate is often heated to optimize the adhesion and uniformity of the coating.
- Proper substrate temperature ensures that the vaporized material spreads evenly and bonds effectively to the surface.
- If the substrate is too cold, the coating may not adhere properly; if too hot, it may cause defects or unevenness.
-
Advantages of High-Vacuum Conditions:
- The high-vacuum environment minimizes the presence of contaminants, such as oxygen or moisture, which could react with the vaporized material.
- It also reduces heat transfer, allowing for precise control over the deposition process.
- The vacuum ensures that the vaporized material travels in a straight line, coating only the surfaces within line of sight.
-
Applications of Evaporation Coating:
- This process is widely used in industries requiring high-precision coatings, such as:
- Electronics: For creating thin films on semiconductors and circuit boards.
- Optics: For applying anti-reflective or reflective coatings on lenses and mirrors.
- Aerospace: For protective coatings on critical components.
- The ability to produce micro-thin, uniform coatings makes it ideal for advanced technological applications.
- This process is widely used in industries requiring high-precision coatings, such as:
-
Types of Evaporation Techniques:
- Thermal Evaporation: Uses resistive heating to vaporize the source material.
- Electron Beam Evaporation: Employs a focused electron beam to heat and evaporate the material, suitable for high-melting-point materials.
- Induction Heating: Utilizes electromagnetic induction to heat the material, often used for large-scale applications.
-
Challenges and Considerations:
- The process requires precise control over temperature, vacuum pressure, and deposition rate.
- Line-of-sight deposition means that complex geometries may require additional techniques, such as rotating the substrate or using multiple evaporation sources.
- The cost of maintaining high-vacuum conditions and specialized equipment can be a limiting factor for some applications.
By following these steps and considerations, evaporation coating provides a reliable and efficient method for creating high-quality, thin-film coatings on a variety of substrates.
Summary Table:
Key Aspect | Details |
---|---|
Process | Physical Vapor Deposition (PVD) technique for thin-film coating. |
Environment | High-vacuum chamber to minimize contamination. |
Heating Methods | Resistive, electron beam, or induction heating for material vaporization. |
Applications | Electronics, optics, aerospace for high-precision coatings. |
Advantages | Clean, precise, uniform coatings with strong adhesion. |
Challenges | Requires precise temperature control and high-vacuum maintenance. |
Discover how evaporation coating can enhance your projects—contact our experts today!