Isostatic pressing is a manufacturing process that involves applying uniform pressure to a powder or material enclosed in a flexible mold, typically made of polyurethane. This process can be performed using either the wet-bag or dry-bag technique, depending on the application. The general steps include loading the powder into the mold, sealing it, applying hydrostatic pressure via a liquid medium in a pressure vessel, and then releasing the pressure to retrieve the compacted product. This method ensures uniform density and shape, making it suitable for producing complex geometries and high-performance materials. The process is widely used in industries such as aerospace, automotive, and ceramics.
Key Points Explained:
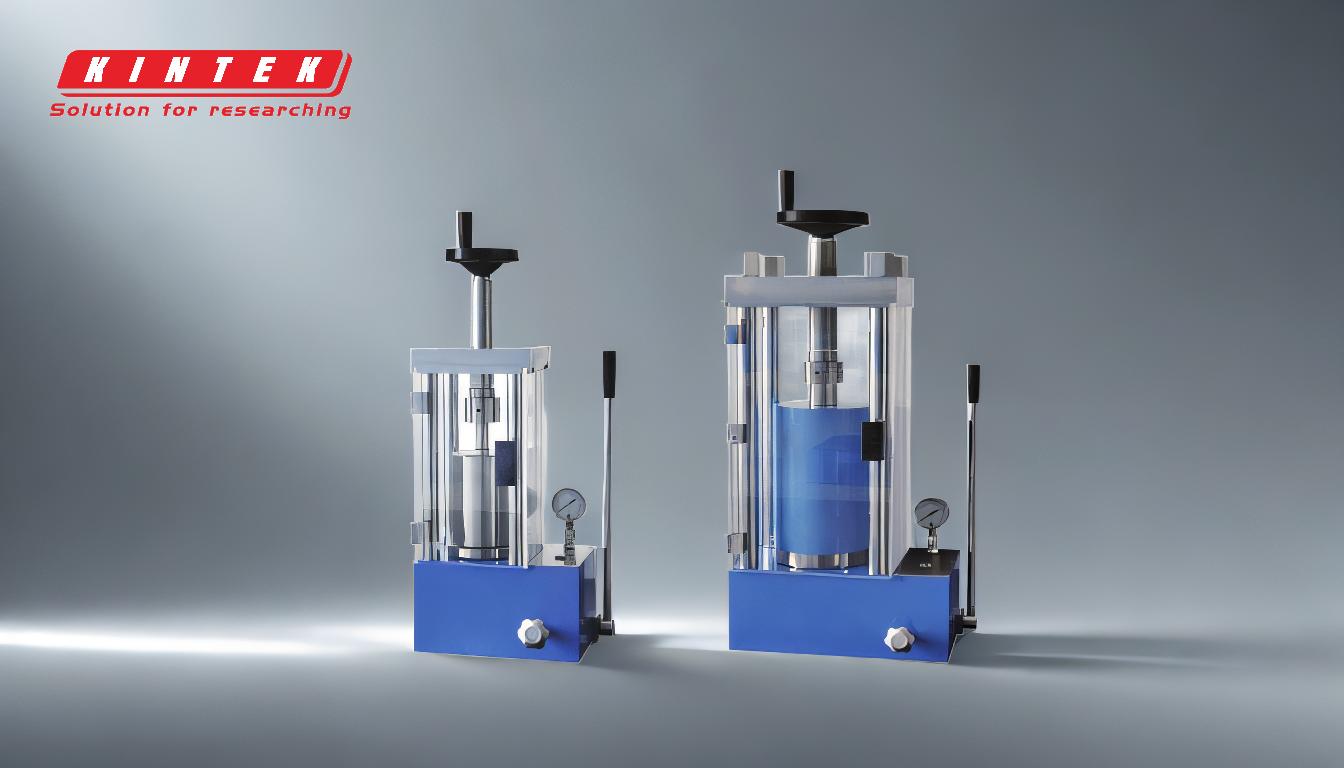
-
Flexible Mold and Powder Loading
- The process begins by loading the powder into a flexible mold, often made of materials like polyurethane. This mold is designed to deform under pressure, ensuring uniform compaction of the powder.
- The mold is then sealed to prevent leakage of the powder or the pressurizing fluid during the process.
-
Wet-Bag vs. Dry-Bag Techniques
- Wet-Bag Technique: The flexible mold containing the powder is submerged in a pressure vessel filled with a pressurizing fluid, such as oil or water. This technique is versatile and suitable for small-scale or custom production.
- Dry-Bag Technique: The flexible mold is permanently fixed inside the pressure vessel, and powder is loaded without removing the mold. This method is more efficient for high-volume production.
-
Application of Hydrostatic Pressure
- The pressure vessel is filled with a liquid medium, which is pressurized to apply uniform hydrostatic pressure on all surfaces of the mold. This ensures equal force distribution, regardless of the shape or size of the product.
- In cold isostatic pressing machine processes, pressures can reach up to 100,000 psi, depending on the material and application.
-
Compaction and Density Increase
- The applied pressure compacts the powder, increasing its density and forming it into the desired shape. The uniform pressure eliminates voids and ensures consistent material properties throughout the product.
- This step is critical for producing high-performance materials with minimal defects.
-
Pressure Release and Product Retrieval
- After the compaction process, the pressure is gradually released, and the compacted product is removed from the mold. The flexible mold allows for easy extraction of the final product.
- The product retains its shape and density, ready for further processing or use.
-
Applications and Capacities
- Isostatic pressing is used in various industries, including aerospace, automotive, and ceramics, to produce components with complex geometries and high strength.
- The process can be scaled to different capacities, including small-sized, medium-sized, and large-sized HIP (Hot Isostatic Pressing) systems, depending on the production requirements.
-
Advantages of Isostatic Pressing
- Uniform pressure application ensures consistent density and material properties.
- Suitable for producing complex shapes and intricate designs.
- Reduces material waste and improves product performance.
By following these steps, isostatic pressing provides a reliable and efficient method for producing high-quality, dense materials with uniform properties. The choice between wet-bag and dry-bag techniques depends on the specific application and production scale, making it a versatile process for various industries.
Summary Table:
Step | Details |
---|---|
Flexible Mold & Powder Loading | Powder is loaded into a flexible mold (e.g., polyurethane) and sealed to prevent leakage. |
Wet-Bag vs. Dry-Bag Techniques | Wet-bag: Submerged in fluid for versatility. Dry-bag: Mold fixed for high-volume production. |
Hydrostatic Pressure Application | Uniform pressure applied via liquid medium (up to 100,000 psi) for equal force distribution. |
Compaction & Density Increase | Pressure compacts powder, eliminating voids and ensuring uniform density. |
Pressure Release & Product Retrieval | Pressure is released, and the compacted product is removed, retaining shape and density. |
Applications | Aerospace, automotive, and ceramics industries for complex geometries and high-strength parts. |
Advantages | Uniform density, complex shapes, reduced waste, and improved performance. |
Discover how isostatic pressing can enhance your production—contact our experts today!