LPCVD (Low-Pressure Chemical Vapor Deposition) is a thermal process used to deposit thin films on substrates, primarily in the electronics industry. It operates at subatmospheric pressures and relies on gas-phase precursors that react on the substrate surface to form a uniform film. The process is temperature-dependent, with precise control over the growth rate, ensuring excellent uniformity across wafers and runs. LPCVD is widely used for depositing materials like polysilicon, silicon nitride, and silicon dioxide, and it operates at relatively lower temperatures (250–350°C), making it more economical compared to higher-temperature CVD processes.
Key Points Explained:
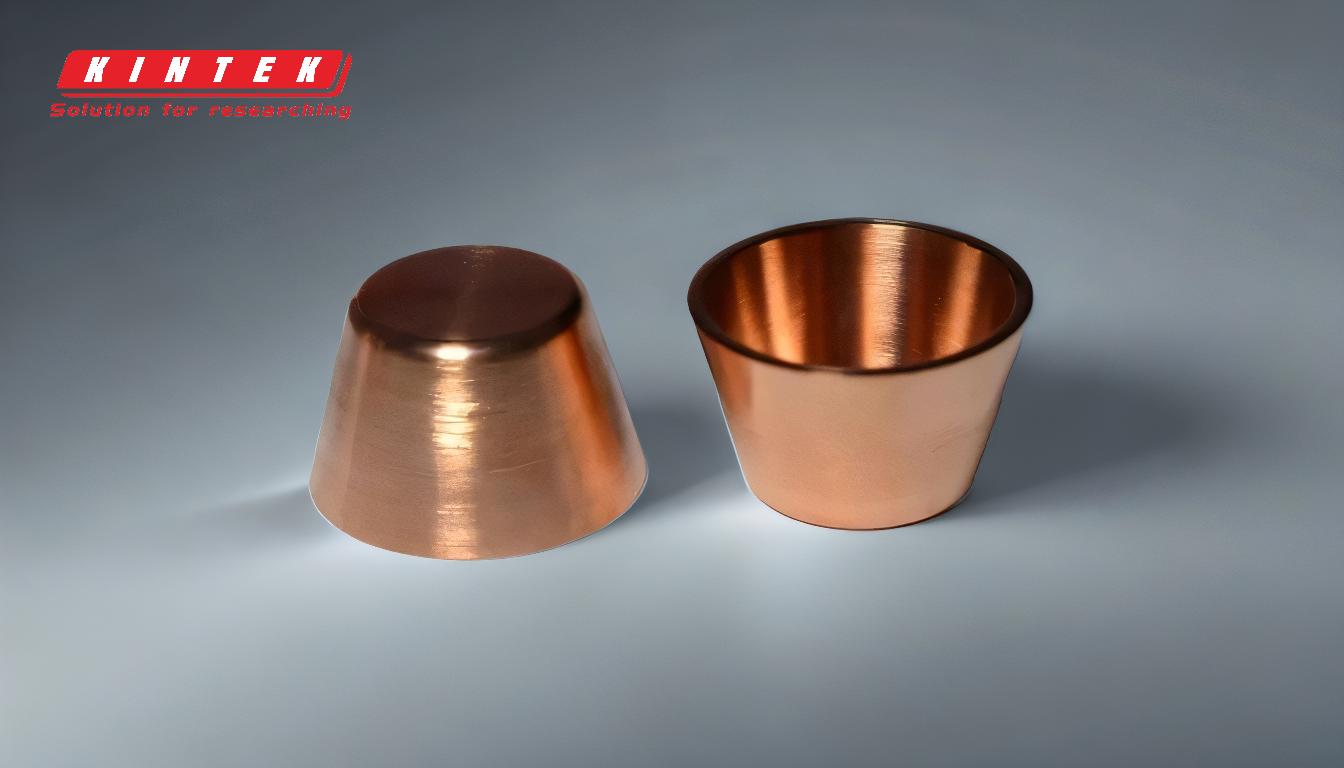
-
Definition and Purpose of LPCVD:
- LPCVD stands for Low-Pressure Chemical Vapor Deposition.
- It is a process used to deposit thin films of materials such as polysilicon, silicon nitride, and silicon dioxide on substrates.
- The process is widely used in the electronics industry for creating uniform and high-quality films.
-
Process Conditions:
- LPCVD operates at subatmospheric pressures, meaning it works under vacuum conditions.
- Reactant gases are introduced into the chamber, where they react on the substrate surface to form a continuous film.
- The process is designed so that the growth rate is limited by the rate of the surface reaction, which is highly temperature-dependent.
-
Temperature Control:
- The temperature in LPCVD can be controlled with great precision, typically ranging from 250 to 350 degrees Celsius.
- This precise temperature control ensures excellent uniformity within a wafer, from wafer to wafer, and across different runs.
- The lower operating temperatures make LPCVD more economical compared to other CVD processes that require higher temperatures.
-
Reactant Gases and Reaction Mechanism:
- Reactant gases are introduced between parallel electrodes in the LPCVD chamber.
- These gases react on the substrate surface, forming a thin film.
- The reaction is typically a surface reaction, meaning the growth rate is controlled by the rate at which the gases react on the substrate surface.
-
Advantages of LPCVD:
- Uniformity: LPCVD provides excellent uniformity across wafers and runs, which is critical for applications in the electronics industry.
- Precision: The ability to control temperature and pressure precisely allows for consistent and high-quality film deposition.
- Economical: Operating at lower temperatures reduces energy consumption and costs compared to higher-temperature CVD processes.
-
Applications:
- LPCVD is widely used in the electronics industry for depositing thin films of materials such as polysilicon, silicon nitride, and silicon dioxide.
- These materials are essential for the fabrication of semiconductor devices, integrated circuits, and other electronic components.
-
Comparison with Other CVD Processes:
- LPCVD operates at lower pressures and temperatures compared to other CVD processes.
- The lower pressure helps in achieving better step coverage and uniformity in film deposition.
- The lower temperature range (250–350°C) makes it more suitable for applications where high-temperature processes could damage the substrate or other materials.
In summary, LPCVD is a highly controlled and efficient process for depositing thin films with excellent uniformity and precision. Its lower operating temperatures and subatmospheric pressures make it a preferred choice in the electronics industry for applications requiring high-quality thin films.
Summary Table:
Key Aspect | Details |
---|---|
Definition | Low-Pressure Chemical Vapor Deposition (LPCVD) |
Purpose | Deposits thin films like polysilicon, silicon nitride, and silicon dioxide |
Operating Conditions | Subatmospheric pressure, 250–350°C temperature range |
Key Advantages | Uniformity, precision, and cost-efficiency |
Applications | Semiconductor devices, integrated circuits, and electronic components |
Comparison to Other CVD | Lower pressure and temperature, better step coverage |
Discover how LPCVD can enhance your thin film processes—contact our experts today!