Magnetron sputtering is a highly efficient physical vapor deposition (PVD) technique used to deposit thin films onto substrates. The process involves creating a high-energy plasma in a vacuum chamber, where positively charged argon ions are accelerated toward a negatively charged target material. The ions eject atoms from the target, which then travel and deposit onto the substrate, forming a thin film. A magnetic field is used to confine electrons near the target surface, increasing plasma density and deposition rates while protecting the substrate from damage. This method is widely used in industries such as semiconductors, optics, and coatings due to its precision and versatility.
Key Points Explained:
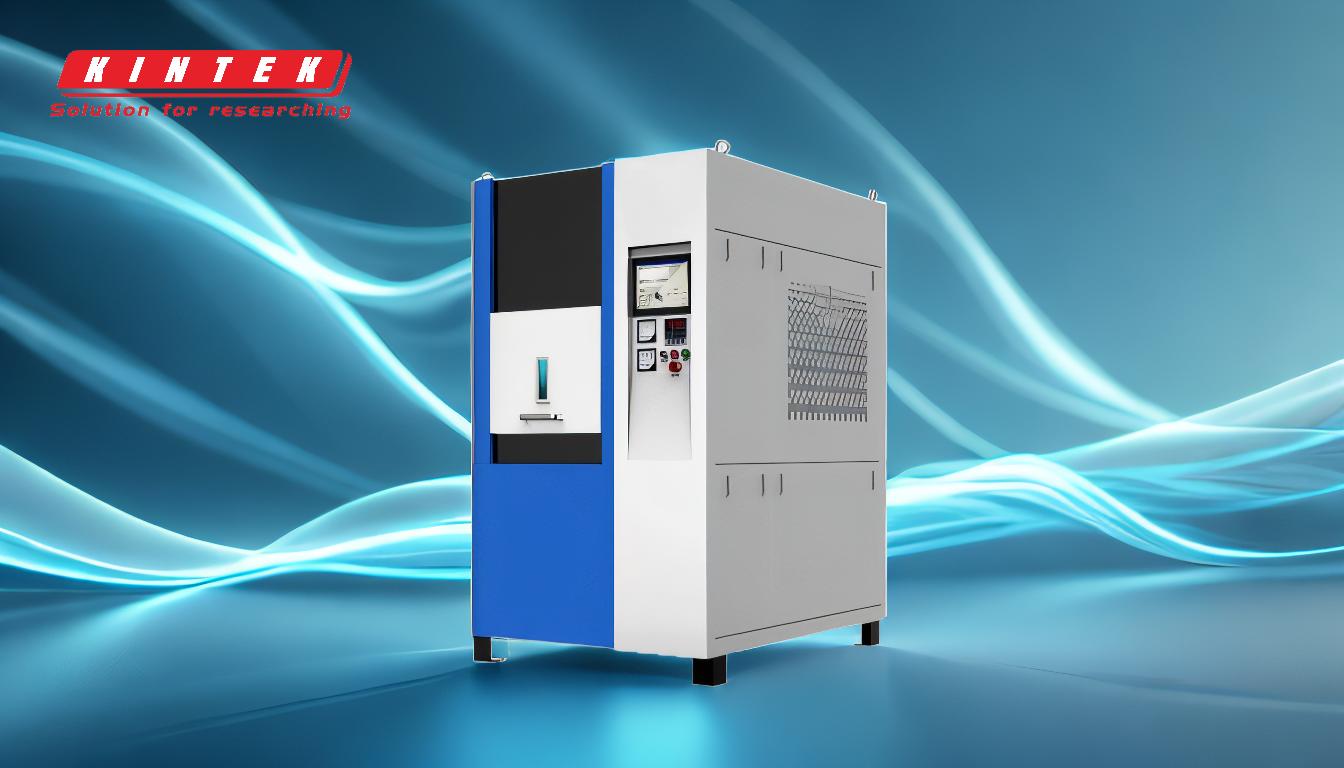
-
Vacuum Chamber Setup:
- The process begins in a high vacuum chamber to minimize contaminants and ensure a clean environment for deposition.
- The chamber is evacuated to a low pressure, typically in the milli Torr range, to create the necessary conditions for plasma generation.
-
Introduction of Sputtering Gas:
- An inert gas, usually argon, is introduced into the chamber. Argon is preferred because it is chemically inert and does not react with the target material or the substrate.
- The gas flows continuously into the chamber to maintain the required pressure for plasma formation.
-
Generation of Plasma:
- A high negative voltage is applied between the cathode (target) and anode, ionizing the argon gas and creating a plasma.
- The plasma consists of positively charged argon ions, free electrons, and neutral argon atoms. This plasma emits a glow discharge, which is visible as a colorful halo of light.
-
Role of the Magnetic Field:
- A magnetic field is generated using magnet arrays near the target. This field confines electrons in a spiral motion close to the target surface, increasing the ionization rate of the argon gas.
- The magnetic field also enhances the density of the plasma, leading to higher deposition rates and more efficient sputtering.
-
Sputtering of the Target Material:
- Positively charged argon ions from the plasma are accelerated toward the negatively charged target material.
- When these ions collide with the target, they eject neutral atoms, molecules, and secondary electrons from the target surface in a process called sputtering.
- The ejected atoms follow a line-of-sight cosine distribution as they travel toward the substrate.
-
Deposition on the Substrate:
- The ejected target atoms travel through the vacuum chamber and condense on the substrate surface, forming a thin film.
- The substrate is typically positioned opposite the target to ensure uniform deposition.
-
Secondary Electrons and Plasma Maintenance:
- Secondary electrons emitted during the sputtering process collide with the argon gas, helping to sustain the plasma.
- These electrons play a crucial role in maintaining the ionization of the gas and ensuring the continuous operation of the sputtering process.
-
Advantages of Magnetron Sputtering:
- High deposition rates due to the increased plasma density caused by the magnetic field.
- Precise control over film thickness and composition, making it suitable for applications requiring high-quality coatings.
- Reduced substrate damage because the magnetic field confines the plasma near the target, minimizing ion bombardment on the substrate.
-
Applications:
- Magnetron sputtering is widely used in the semiconductor industry for depositing thin films of metals, oxides, and nitrides.
- It is also employed in the production of optical coatings, hard coatings for tools, and decorative finishes.
By understanding these key points, one can appreciate the complexity and precision of the magnetron sputtering process, as well as its importance in modern manufacturing and technology.
Summary Table:
Key Aspect | Description |
---|---|
Vacuum Chamber Setup | High vacuum environment to minimize contaminants and enable plasma generation. |
Sputtering Gas | Argon gas is introduced to create plasma and maintain pressure. |
Plasma Generation | High negative voltage ionizes argon, forming a plasma with ions and electrons. |
Magnetic Field Role | Confines electrons, increases plasma density, and enhances deposition rates. |
Target Sputtering | Argon ions eject target atoms, which travel and deposit onto the substrate. |
Substrate Deposition | Ejected atoms form a thin film on the substrate for precise coatings. |
Secondary Electrons | Sustain plasma by ionizing argon gas, ensuring continuous sputtering. |
Advantages | High deposition rates, precise film control, and reduced substrate damage. |
Applications | Semiconductors, optical coatings, hard coatings, and decorative finishes. |
Discover how magnetron sputtering can enhance your manufacturing process—contact our experts today!