The process of pelleting biomass involves converting raw biomass materials, such as wood, straw, or agricultural residues, into dense, uniform pellets that can be used as fuel or for other applications. This process typically includes several key steps: drying, grinding, conditioning, pelleting, cooling, and packaging. The goal is to create a compact, energy-dense product that is easy to transport, store, and use.
Key Points Explained:
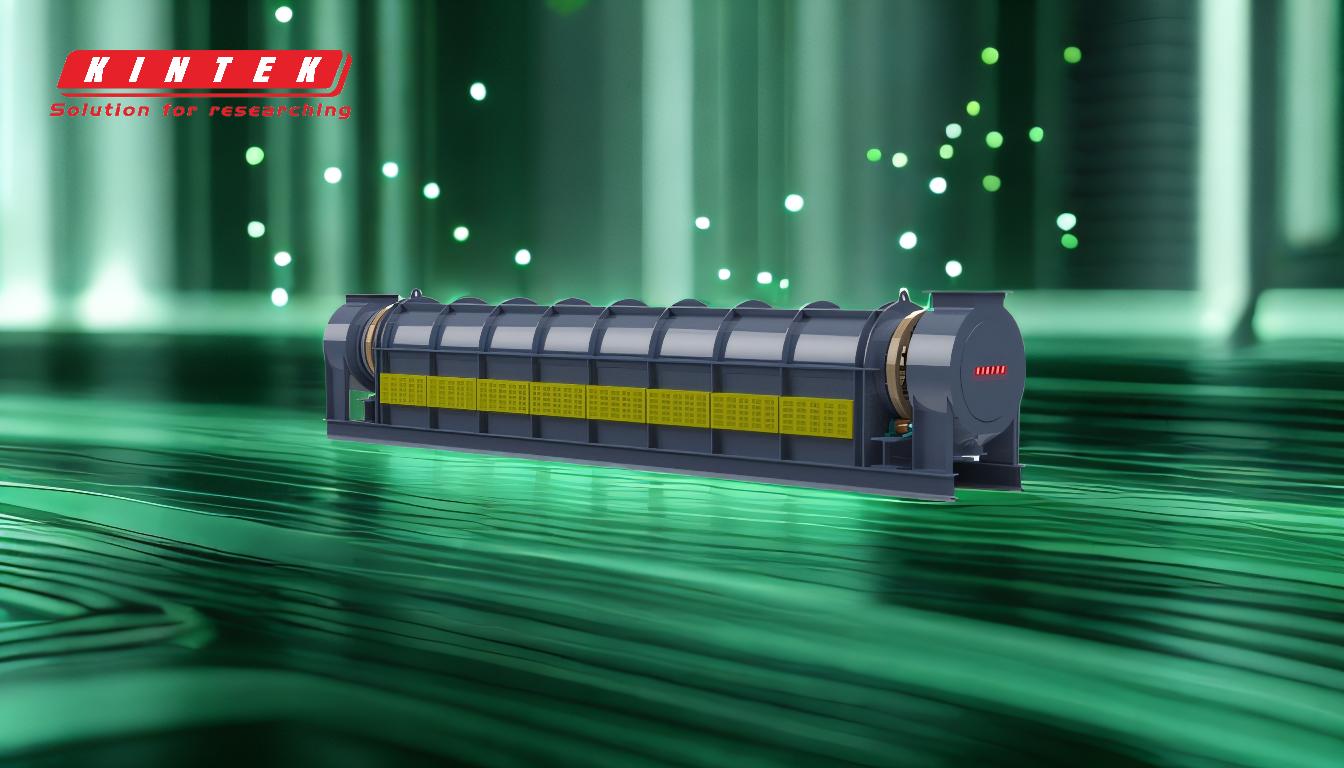
-
Drying:
- Raw biomass often contains a high moisture content, which must be reduced to ensure efficient pelleting.
- The drying process typically involves heating the biomass to evaporate excess moisture, bringing it down to an optimal level (usually around 10-15% moisture content).
- Proper drying is crucial because excessive moisture can lead to poor pellet quality and inefficiencies in the pelleting machine.
-
Grinding:
- After drying, the biomass is ground into smaller particles to ensure uniformity and improve the efficiency of the pelleting process.
- The size of the particles depends on the type of biomass and the desired pellet size. Smaller particles allow for better compression and binding during pelleting.
- Hammer mills or grinders are commonly used for this step.
-
Conditioning:
- Conditioning involves adding steam or water to the ground biomass to soften it and improve its binding properties.
- This step ensures that the biomass particles stick together more effectively during the pelleting process.
- The addition of binders, such as lignin or starch, may also be used to enhance pellet durability.
-
Pelleting:
- The conditioned biomass is fed into a pellet mill, where it is compressed under high pressure and forced through a die with small holes.
- The friction and pressure generated in the pellet mill cause the biomass to heat up, which helps bind the particles together.
- The pellets are extruded from the die in cylindrical shapes and cut to the desired length.
-
Cooling:
- Freshly extruded pellets are hot and soft, so they need to be cooled and hardened to maintain their shape and durability.
- Cooling is typically done using a pellet cooler, which blows ambient air over the pellets to reduce their temperature and moisture content.
- Proper cooling ensures the pellets are stable and ready for storage or transport.
-
Packaging:
- Once cooled, the pellets are screened to remove fines (small particles that did not form into pellets) and then packaged for distribution.
- Packaging methods vary depending on the intended use, but common options include bags, bulk containers, or storage silos.
- Proper packaging protects the pellets from moisture and contamination, ensuring their quality is maintained.
By following these steps, biomass is transformed into a high-quality, energy-dense product that can be used for heating, electricity generation, or other industrial applications. The pelleting process not only makes biomass easier to handle but also enhances its combustion efficiency and reduces transportation costs.
Summary Table:
Step | Description |
---|---|
Drying | Reduce moisture content to 10-15% for efficient pelleting. |
Grinding | Ground into smaller particles for uniformity and better compression. |
Conditioning | Add steam or binders to improve binding properties. |
Pelleting | Compress biomass under high pressure to form cylindrical pellets. |
Cooling | Cool pellets to harden and stabilize them for storage or transport. |
Packaging | Screen and package pellets to protect from moisture and contamination. |
Ready to optimize your biomass pelleting process? Contact us today for expert guidance!