The pyrolysis of rubber, particularly from waste tires, is a thermochemical process that breaks down rubber into smaller molecules in the absence of oxygen. This process generates valuable outputs such as pyrolysis oil, carbon black, and syngas, which can be used for energy production, industrial applications, or further refining. The process involves several stages, including pre-treatment, heating, vaporization, condensation, and product collection. Each step is carefully controlled to optimize the yield and quality of the end products. Pyrolysis is an effective method for recycling rubber waste, reducing environmental pollution, and recovering valuable resources.
Key Points Explained:
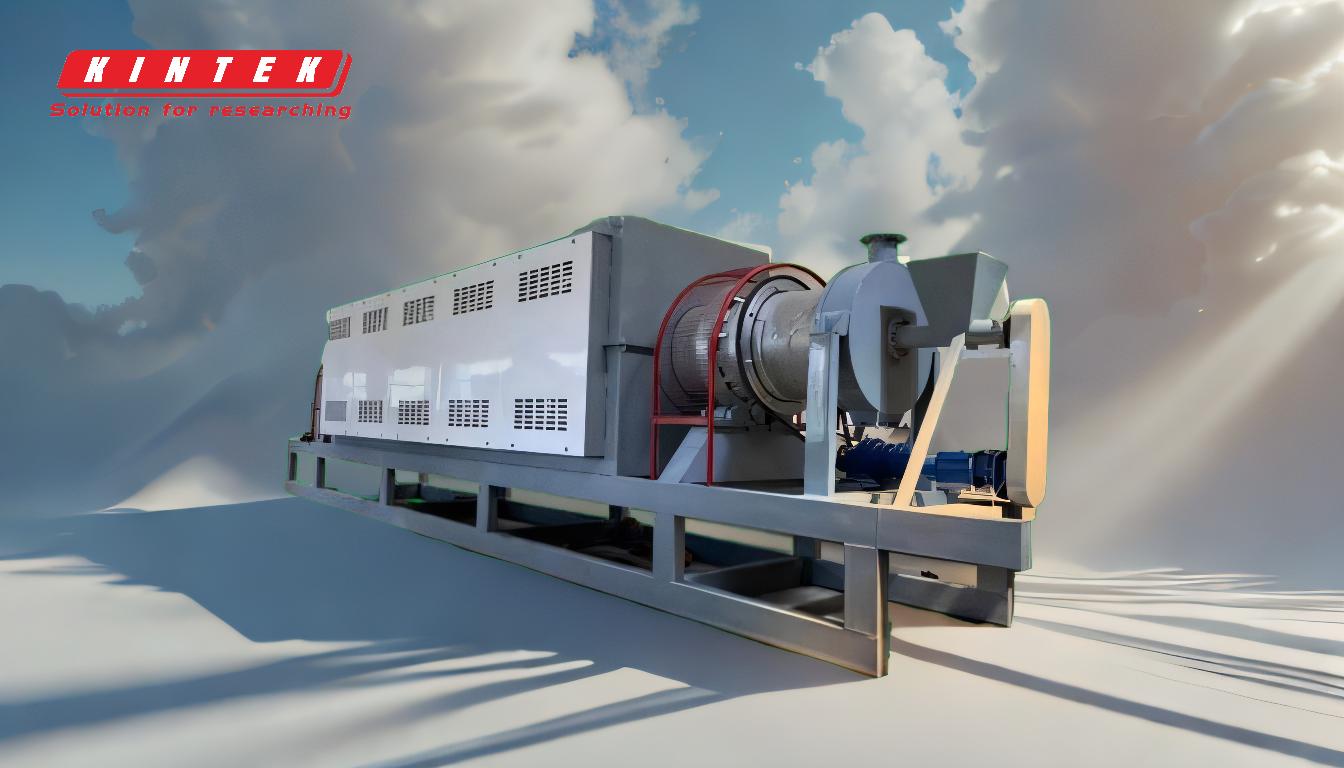
-
Pre-Treatment of Rubber Waste:
- Before pyrolysis, rubber waste, such as tires, undergoes pre-treatment to remove impurities and prepare it for processing.
- This may include shredding the tires into smaller pieces to increase the surface area and improve heat transfer during pyrolysis.
- Non-rubber components like steel wires are often separated during this stage.
-
Loading into the Pyrolysis Reactor:
- The pre-treated rubber is loaded into a pyrolysis reactor, which is designed to operate in the absence of oxygen.
- The reactor is sealed to prevent any oxygen from entering, as its presence could lead to combustion instead of pyrolysis.
-
Heating and Thermal Decomposition:
- The reactor is heated to temperatures typically ranging from 300°C to 900°C, depending on the desired products and the type of rubber being processed.
- At these high temperatures, the rubber undergoes thermal decomposition, breaking down into smaller molecules.
- The process is endothermic, meaning it requires a continuous input of heat to maintain the reaction.
-
Vaporization and Gas Formation:
- As the rubber decomposes, it produces vapors consisting of various hydrocarbons and gases.
- These vapors are a mixture of condensable and non-condensable gases, which will be separated in subsequent steps.
-
Condensation of Vapors:
- The vapors are passed through a condensation system, where they are cooled and condensed into liquid pyrolysis oil.
- The non-condensable gases, such as methane, ethane, and hydrogen, are collected separately and can be used as fuel for the pyrolysis process or other applications.
-
Collection of Solid Residues:
- After the pyrolysis process, solid residues such as carbon black and steel wires remain in the reactor.
- Carbon black is a valuable byproduct used in various industries, including tire manufacturing, inks, and coatings.
- Steel wires are separated and recycled for use in other applications.
-
Refining and Storage of Pyrolysis Oil:
- The liquid pyrolysis oil collected from the condensation process may undergo further refining to improve its quality and remove any impurities.
- The refined oil can be used as a fuel or as a feedstock for chemical production.
- It is stored in tanks for later use or dispatch.
-
Environmental and Economic Benefits:
- Pyrolysis of rubber waste helps reduce the environmental impact of tire disposal by converting waste into valuable products.
- The process also contributes to resource recovery, as the byproducts can be used in various industrial applications, reducing the need for virgin materials.
- Economically, pyrolysis offers a sustainable solution for waste management and creates opportunities for revenue generation from the sale of pyrolysis products.
-
Challenges and Considerations:
- The pyrolysis process is energy-intensive and requires careful control of temperature and pressure to ensure optimal product yields.
- The quality of the pyrolysis oil and other byproducts depends on the composition of the rubber feedstock and the process conditions.
- Proper handling and disposal of any residual waste or emissions are essential to minimize environmental impact.
In summary, the pyrolysis of rubber is a multi-step process that transforms waste rubber into valuable products such as pyrolysis oil, carbon black, and syngas. Each stage, from pre-treatment to product collection, is crucial for ensuring the efficiency and sustainability of the process. By converting rubber waste into useful resources, pyrolysis offers a viable solution for waste management and resource recovery.
Summary Table:
Stage | Description |
---|---|
Pre-Treatment | Shredding and removing impurities from rubber waste (e.g., tires). |
Loading into Reactor | Sealed reactor ensures no oxygen, preventing combustion. |
Heating & Decomposition | Rubber breaks down at 300°C–900°C, producing vapors and gases. |
Vaporization & Gas Formation | Hydrocarbon vapors and gases are generated. |
Condensation | Vapors are cooled into pyrolysis oil; non-condensable gases are collected. |
Solid Residue Collection | Carbon black and steel wires are separated for reuse. |
Refining & Storage | Pyrolysis oil is refined and stored for industrial use. |
Environmental Benefits | Reduces waste, recovers resources, and minimizes environmental pollution. |
Challenges | Energy-intensive process; requires precise temperature and pressure control. |
Discover how pyrolysis can revolutionize waste management—contact us today for expert guidance!