The pyrolysis of tires is a thermal decomposition process that converts waste tires into valuable products such as fuel oil, carbon black, steel wire, and gas. This process involves heating the tires in an oxygen-free environment to break down the rubber into smaller molecules. The key steps include loading whole or shredded tires into a reactor, heating the reactor to specific temperatures, condensing the vaporized gases into liquid oil, and collecting the solid residues. The process is energy-efficient and environmentally friendly, as it recycles waste tires into useful resources.
Key Points Explained:
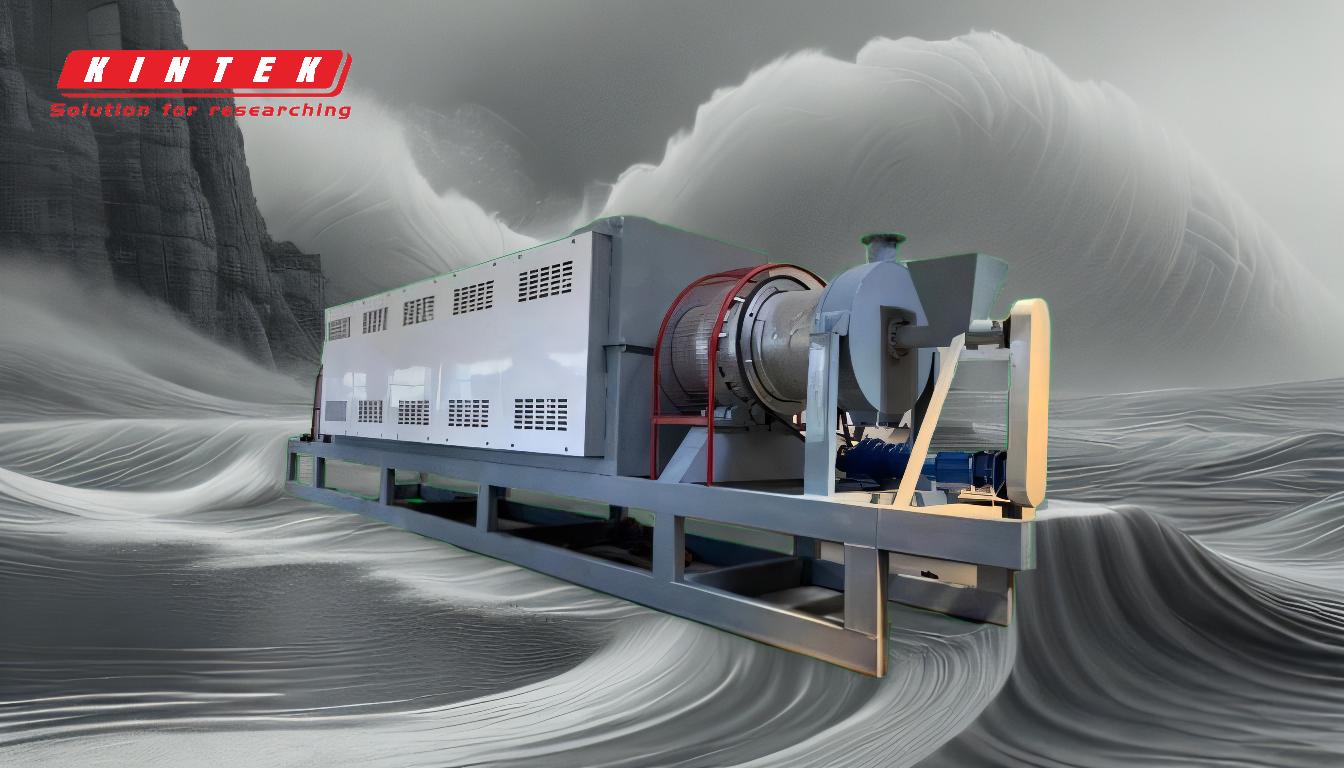
-
Preparation of Waste Tires:
- Shredding: Waste tires are often shredded into smaller pieces to increase the surface area and improve the efficiency of the pyrolysis process. This step is optional, as some systems can process whole tires directly.
- Pre-Treatment: Impurities such as dirt, metals, and other non-rubber materials are removed to ensure the quality of the end products. Magnetic separation is commonly used to extract steel wires from the tires.
-
Loading into the Reactor:
- The prepared tires are loaded into a pyrolysis reactor, which is then sealed to create an oxygen-free environment. The absence of oxygen is crucial to prevent combustion and ensure the thermal decomposition of the rubber.
-
Heating and Thermal Decomposition:
- Temperature Control: The reactor is heated to a temperature range of 200°C to 900°C, depending on the desired end products. The temperature is gradually increased to allow the rubber to melt and vaporize.
- Depolymerization: As the temperature rises, the rubber undergoes depolymerization, breaking down into smaller molecules. At around 100°C, small volatile molecules are released. At 140°C, the rubber melts into a liquid state. Between 260°C and 280°C, the rubber cracks into monomers and fragments, which then polymerize into various olefins.
-
Condensation of Vapors:
- Heat Exchange: The vaporized gases flow through a heat exchanger, where they are cooled and condensed into liquid oil. This oil, known as pyrolysis oil, can be used as fuel or further refined for other applications.
- Separation of Non-Condensable Gases: Non-condensable gases, such as methane and hydrogen, are separated and cleaned. These gases can be used to power the pyrolysis process or stored for later use.
-
Collection of Solid Residues:
- Carbon Black: The solid residue left after the pyrolysis process is primarily carbon black, which can be used as a reinforcing agent in rubber products, as a pigment, or as a fuel source.
- Steel Wire: Steel wires, which are not affected by the pyrolysis process, are separated from the carbon black and can be recycled.
-
Final Product Storage and Dispatch:
- Pyrolysis Oil: The condensed liquid oil is stored in tanks and can be dispatched for use as fuel or further processing.
- Carbon Black and Steel Wire: These solid products are collected and stored for sale or further processing.
-
Environmental and Economic Benefits:
- Waste Reduction: Pyrolysis significantly reduces the volume of waste tires, addressing environmental concerns associated with tire disposal.
- Resource Recovery: The process converts waste tires into valuable resources, contributing to a circular economy.
- Energy Efficiency: The non-condensable gases generated during pyrolysis can be used to power the process, making it energy-efficient.
In summary, the pyrolysis of tires is a multi-step process that transforms waste tires into useful products through thermal decomposition in an oxygen-free environment. The process involves preparation, heating, condensation, and collection of end products, offering both environmental and economic benefits.
Summary Table:
Step | Description |
---|---|
Preparation | Shredding and pre-treatment of tires to remove impurities. |
Loading Reactor | Tires are loaded into a sealed, oxygen-free reactor. |
Heating | Reactor heated to 200°C–900°C for depolymerization. |
Condensation | Vapors are cooled into pyrolysis oil; non-condensable gases are separated. |
Solid Residues | Carbon black and steel wire are collected for reuse or sale. |
Final Products | Pyrolysis oil, carbon black, and steel wire are stored and dispatched. |
Benefits | Reduces waste, recovers resources, and is energy-efficient. |
Discover how tire pyrolysis can benefit your business—contact us today to learn more!