The pyrolysis of waste tires is a thermochemical process that converts discarded tires into valuable products such as pyrolysis oil, carbon black, steel wire, and gas. This process involves heating the tires in an oxygen-free environment to break down their complex polymer structures into simpler components. The key steps include tire pre-treatment, loading into a pyrolysis reactor, heating to induce depolymerization, condensation of vapors into liquid oil, and collection of by-products. The resulting products have applications in energy generation, industrial processes, and material reuse, making tire pyrolysis an environmentally and economically beneficial recycling method.
Key Points Explained:
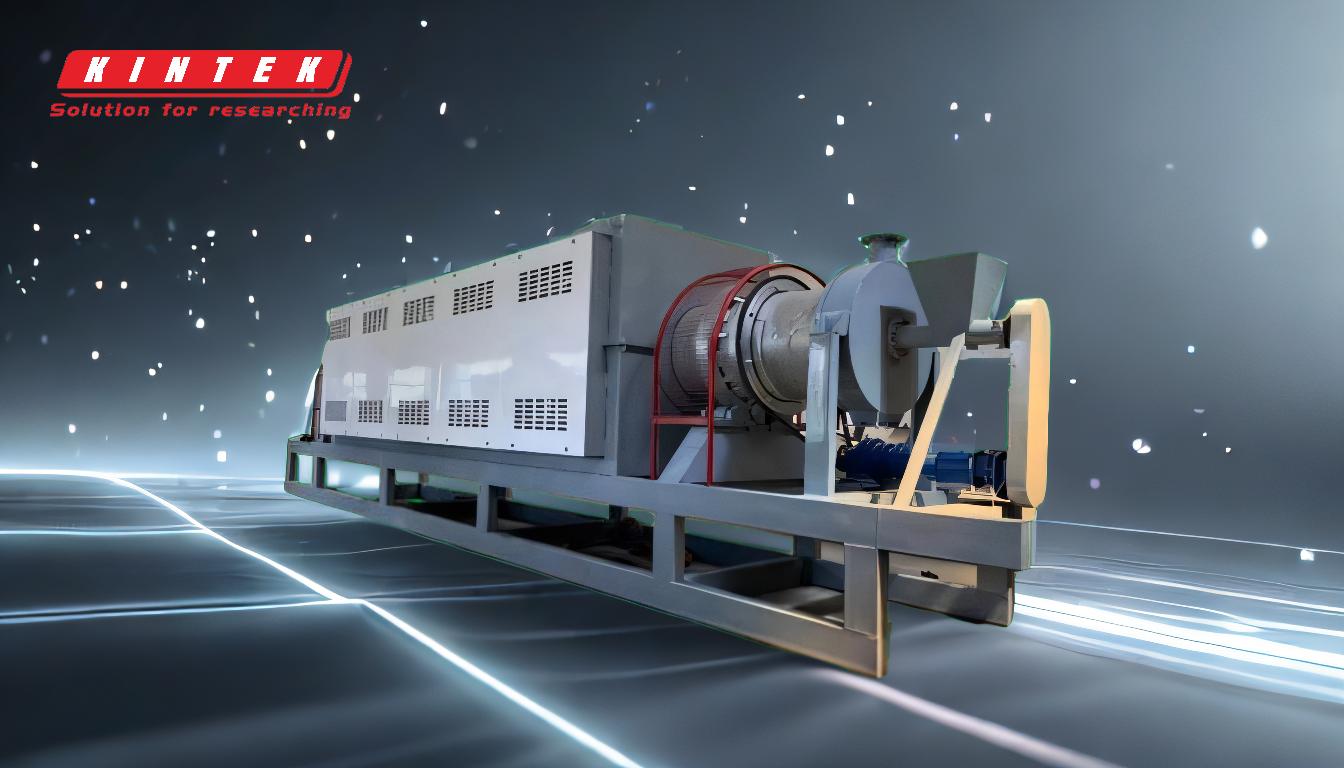
-
Pre-Treatment of Waste Tires
- Before pyrolysis, waste tires undergo pre-treatment to prepare them for the process. This may include:
- Shredding: Tires are cut into smaller pieces to ensure uniform heating and efficient processing.
- Magnetic Separation: Steel wires embedded in the tires are removed using magnetic separators for recycling.
- Drying: Moisture is removed to prevent unwanted reactions during pyrolysis.
- Before pyrolysis, waste tires undergo pre-treatment to prepare them for the process. This may include:
-
Loading into the Pyrolysis Reactor
- The pre-treated tires are loaded into a pyrolysis reactor, which is a sealed, oxygen-free chamber designed to withstand high temperatures.
- The reactor is placed inside a furnace, and oxygen is evacuated to create an inert environment, preventing combustion.
-
Heating and Depolymerization
- The reactor is heated to temperatures typically ranging from 200°C to 900°C, depending on the desired products and process efficiency.
- During this stage, the rubber polymers in the tires undergo thermal cracking or depolymerization, breaking down into smaller molecules. This process generates:
- Pyrolysis Gas: A mixture of hydrocarbons and other gases.
- Pyrolysis Oil: Condensable hydrocarbons in liquid form.
- Solid Residues: Carbon black and any remaining steel wires.
-
Condensation and Separation
- The pyrolysis gas is passed through a heat exchanger or condenser, where the condensable hydrocarbons are cooled and collected as pyrolysis oil.
- Non-condensable gases, such as methane and hydrogen, are desulfurized and cleaned before being stored in a gas pressure tank for later use as fuel.
-
Collection of Final Products
- Pyrolysis Oil: This liquid product can be used as fuel for heating, power generation, or further refined into diesel or other industrial oils.
- Carbon Black: A solid residue that can be used as a reinforcing agent in rubber products, pigments, or as a raw material in manufacturing.
- Steel Wire: Recovered during pre-treatment, it can be recycled for use in construction or other industries.
- Non-Condensable Gas: Used as an energy source to power the pyrolysis process or for other industrial applications.
-
Environmental and Economic Benefits
- Tire pyrolysis reduces the volume of waste tires in landfills, mitigating environmental pollution.
- The process generates valuable products that can replace virgin materials, contributing to a circular economy.
- It provides a sustainable solution for managing non-biodegradable rubber waste while reducing reliance on fossil fuels.
-
Applications of Pyrolysis Products
- Pyrolysis Oil: Used as an alternative fuel in boilers, furnaces, and power plants. It can also be refined into higher-value products like diesel or gasoline.
- Carbon Black: Utilized in the production of tires, rubber goods, and coatings.
- Steel Wire: Recycled into new steel products, reducing the need for raw material extraction.
- Non-Condensable Gas: Provides a renewable energy source for the pyrolysis process or other industrial needs.
By following these steps, the pyrolysis process effectively transforms waste tires into useful resources, offering a sustainable and economically viable solution for tire waste management.
Summary Table:
Step | Description |
---|---|
Pre-Treatment | Shredding, magnetic separation, and drying of waste tires. |
Loading into Reactor | Tires are placed in a sealed, oxygen-free pyrolysis reactor. |
Heating & Depolymerization | Reactor heated to 200°C–900°C, breaking down rubber polymers into smaller molecules. |
Condensation & Separation | Pyrolysis gas is condensed into oil; non-condensable gases are cleaned and stored. |
Final Products | Pyrolysis oil, carbon black, steel wire, and non-condensable gas. |
Benefits | Reduces landfill waste, generates valuable products, and supports sustainability. |
Applications | Fuel generation, rubber production, steel recycling, and renewable energy. |
Discover how tire pyrolysis can benefit your business—contact us today to learn more!