Pyrolysis of tires is a thermochemical process that converts waste tires into valuable products such as pyrolysis oil, carbon black, steel wire, and syngas. The process involves heating the tires in the absence of oxygen to break down their long-chain polymers into smaller molecules. This method is environmentally beneficial as it reduces tire waste and generates reusable materials. The process typically includes feeding whole or shredded tires into a reactor, heating them to high temperatures (300-900°C), and then condensing the resulting vapors into liquid oil. Non-condensable gases are cleaned and stored, while solid residues like carbon black and steel wire are collected for further use. The entire process is energy-intensive and requires precise control of temperature and oxygen levels to ensure efficiency and safety.
Key Points Explained:
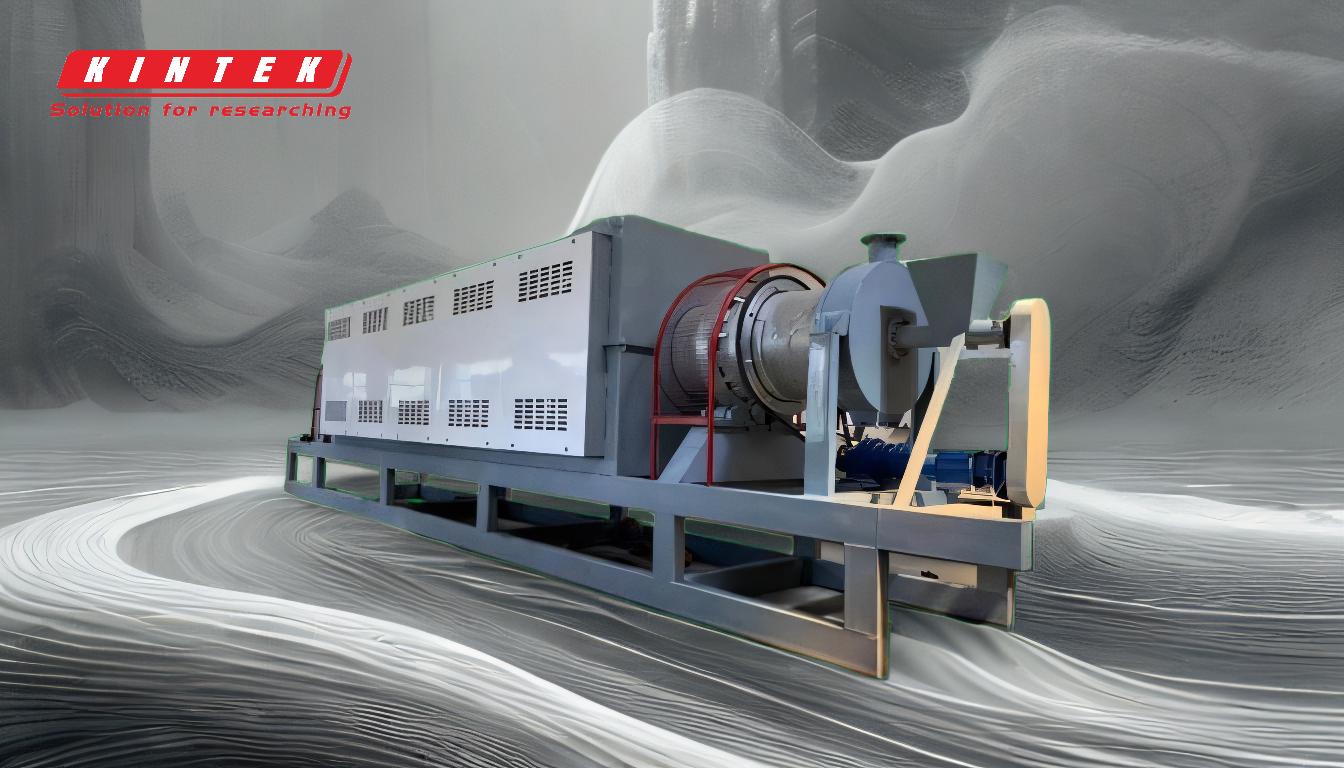
-
Definition and Purpose of Pyrolysis:
- Pyrolysis is a thermal decomposition process that occurs in the absence of oxygen, breaking down materials into smaller molecules.
- For tires, pyrolysis converts waste into useful products like oil, carbon black, steel wire, and syngas, reducing environmental waste and generating valuable resources.
-
Pre-Treatment of Tires:
- Tires are either fed whole or shredded into the reactor.
- Pre-treatment may include removing impurities, magnetic separation to extract steel wires, and grinding tires to the required size for efficient processing.
-
Heating and Depolymerization:
- The reactor is heated to temperatures between 300-900°C in an oxygen-free environment.
- The high temperature causes the tires to melt and vaporize, breaking down the long-chain polymers into smaller hydrocarbon molecules.
-
Condensation and Product Separation:
- The vaporized gases flow through a heat exchanger, where they are condensed into liquid pyrolysis oil.
- Non-condensable gases (syngas) are desulfurized, cleaned, and stored for use as fuel or further processing.
-
Collection of Final Products:
- Pyrolysis Oil: Collected as a liquid, it can be used for heating, power generation, or as a feedstock for hydrogen production.
- Carbon Black: A solid residue, it is used in manufacturing tires, inks, and other industrial applications.
- Steel Wire: Extracted through magnetic separation, it is recycled for use in construction or manufacturing.
- Syngas: Non-condensable gases are stored and can be used to power the pyrolysis process or for other energy needs.
-
Energy and Environmental Considerations:
- The process is energy-intensive, requiring significant heat input to maintain high temperatures.
- Proper control of oxygen levels is crucial to prevent combustion and ensure the process remains purely thermal decomposition.
- Pyrolysis reduces tire waste in landfills and generates reusable materials, contributing to a circular economy.
-
Process Efficiency and Challenges:
- The efficiency of the process depends on factors like temperature control, reactor design, and the quality of the feedstock.
- Challenges include managing the energy requirements, ensuring consistent product quality, and addressing emissions or by-products that may require further treatment.
-
Applications of Pyrolysis Products:
- Pyrolysis Oil: Used as a fuel substitute or refined for chemical production.
- Carbon Black: Recycled into new tires or industrial products.
- Steel Wire: Recycled for use in construction or manufacturing.
- Syngas: Used as a fuel source or for generating electricity.
By following these steps, the pyrolysis of tires not only addresses the issue of tire waste but also creates a sustainable pathway for resource recovery and energy generation.
Summary Table:
Key Products | Applications |
---|---|
Pyrolysis Oil | Heating, power generation, feedstock for hydrogen production |
Carbon Black | Manufacturing tires, inks, and industrial products |
Steel Wire | Recycled for construction or manufacturing |
Syngas | Used as fuel or for generating electricity |
Discover how pyrolysis can transform tire waste into valuable resources—contact us today for more details!