Sputtering is a physical vapor deposition (PVD) technique used to deposit thin films of material onto a substrate. The process involves bombarding a target material with high-energy ions, causing atoms to be ejected from the target and deposited onto a substrate. This method is widely used in industries such as semiconductor manufacturing, optics, and surface coating. The sputtering process typically involves creating a vacuum environment, introducing an inert gas, ionizing the gas to create a plasma, and using the resulting ions to sputter atoms from the target material onto the substrate. The process is highly controllable and allows for the deposition of uniform and high-quality thin films.
Key Points Explained:
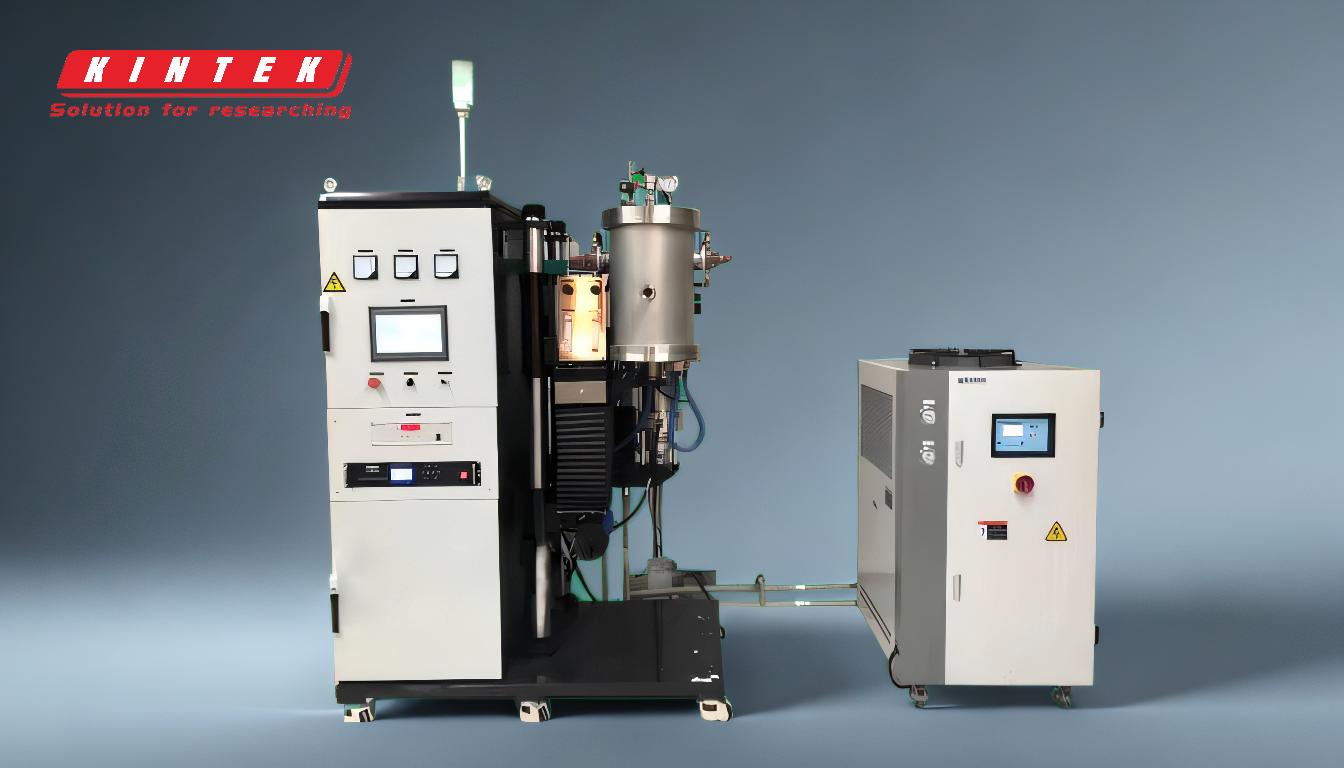
-
Vacuum Chamber Preparation:
- The process begins by placing the target material and substrate inside a vacuum chamber. The chamber is then evacuated to create a low-pressure environment, which is essential for the sputtering process. This step ensures that the deposition occurs in a controlled atmosphere, free from contaminants.
-
Introduction of Inert Gas:
- An inert gas, typically argon, is introduced into the vacuum chamber. The choice of gas depends on the specific requirements of the deposition process. Inert gases are used because they do not react chemically with the target material or the substrate, ensuring the purity of the deposited film.
-
Ionization and Plasma Formation:
- A power source, such as a DC or RF (radio frequency) power supply, is used to ionize the inert gas atoms. This ionization creates a plasma, a state of matter consisting of free electrons and ions. The plasma is essential for generating the high-energy ions needed to sputter atoms from the target material.
-
Sputtering of Target Material:
- The high-energy ions in the plasma bombard the target material, transferring their energy to the target atoms. This energy transfer causes the target atoms to be ejected from the surface in a process known as sputtering. The ejected atoms are neutral and travel through the vacuum chamber.
-
Transport of Sputtered Atoms:
- The sputtered atoms travel through the vacuum chamber and are directed towards the substrate. The low-pressure environment ensures that the atoms move in a straight line, minimizing collisions with other particles and ensuring a uniform deposition.
-
Deposition on Substrate:
- The sputtered atoms condense on the surface of the substrate, forming a thin film. The substrate is typically mounted on a holder that can be rotated or moved to ensure even coverage. The thickness and uniformity of the film can be controlled by adjusting parameters such as the power, pressure, and deposition time.
-
Post-Deposition Processes:
- After the deposition is complete, the vacuum chamber is gradually returned to ambient conditions. This may involve cooling the chamber and substrate to room temperature and venting the chamber to atmospheric pressure. The substrate is then removed for further processing or analysis.
In summary, the sputtering process is a versatile and precise method for depositing thin films of material onto a substrate. It involves creating a vacuum environment, ionizing an inert gas to form a plasma, and using the resulting ions to sputter atoms from a target material onto a substrate. The process is widely used in various industries due to its ability to produce high-quality, uniform thin films.
Summary Table:
Step | Description |
---|---|
1. Vacuum Chamber Prep | Create a low-pressure environment to ensure a contaminant-free deposition. |
2. Inert Gas Introduction | Introduce inert gas (e.g., argon) to maintain purity during the process. |
3. Ionization & Plasma | Ionize gas to form plasma, generating high-energy ions for sputtering. |
4. Sputtering Target | Bombard target material with ions, ejecting atoms for deposition. |
5. Atom Transport | Sputtered atoms travel through the vacuum chamber to the substrate. |
6. Deposition on Substrate | Atoms condense on the substrate, forming a uniform thin film. |
7. Post-Deposition | Return chamber to ambient conditions and prepare substrate for further use. |
Discover how sputtering can enhance your thin film applications—contact our experts today for tailored solutions!