Thin film making is a sophisticated process that involves depositing layers of material onto a substrate to achieve precise thickness, composition, and properties. The process can be broadly categorized into physical, chemical, and solution-based methods, each with its own set of techniques such as Physical Vapour Deposition (PVD), Chemical Vapour Deposition (CVD), spin coating, and more. These methods are chosen based on the desired film properties, application requirements, and material characteristics. The process begins with substrate preparation, followed by the deposition of the thin film, and concludes with post-deposition treatments to enhance film properties.
Key Points Explained:
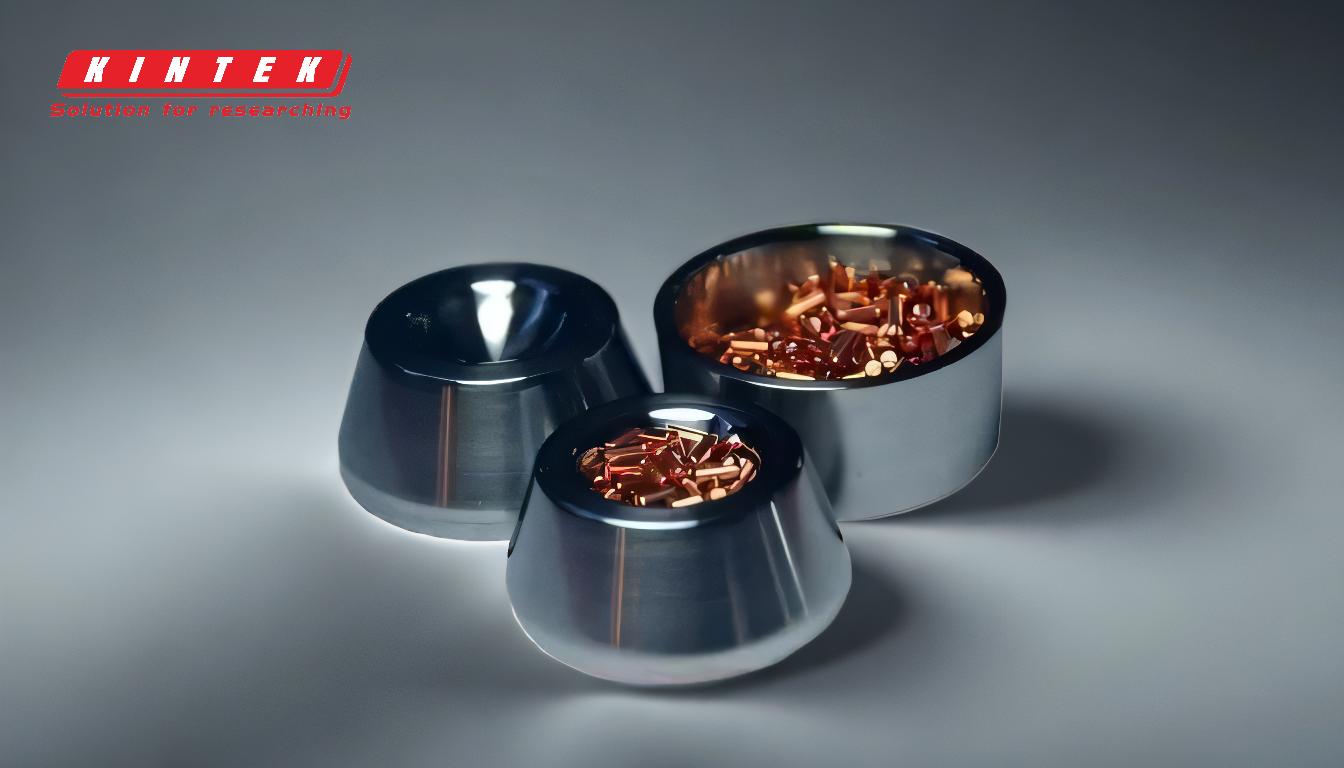
-
Substrate Preparation
- Cleaning: The substrate must be thoroughly cleaned to remove any contaminants that could affect the adhesion and quality of the thin film. Techniques include ultrasonic cleaning, chemical cleaning, and plasma cleaning.
- Surface Treatment: Surface treatments such as etching or applying adhesion promoters may be necessary to improve the bonding between the substrate and the thin film.
-
Deposition Techniques
-
Physical Vapour Deposition (PVD):
- Evaporation: Material is heated in a vacuum until it vaporizes, then condenses on the substrate to form a thin film. This method is suitable for materials with relatively low melting points.
- Sputtering: A target material is bombarded with ions, causing atoms to be ejected and deposited onto the substrate. This technique is versatile and can be used for a wide range of materials.
-
Chemical Vapour Deposition (CVD):
- Thermal CVD: The substrate is exposed to volatile precursors that react or decompose on the substrate surface to form the desired thin film. This method is widely used for depositing high-quality, uniform films.
- Plasma-Enhanced CVD (PECVD): Plasma is used to enhance the chemical reaction, allowing deposition at lower temperatures compared to thermal CVD.
-
Solution-Based Methods:
- Spin Coating: A solution containing the film material is applied to the substrate, which is then spun at high speed to spread the solution evenly and evaporate the solvent, leaving a thin film.
- Dip Coating: The substrate is dipped into a solution and then withdrawn at a controlled speed, allowing a thin film to form as the solvent evaporates.
- Layer-by-Layer (LbL) Assembly: Alternating layers of different materials are deposited onto the substrate, often through dip or spin coating, to create complex multilayered structures.
-
Physical Vapour Deposition (PVD):
-
Post-Deposition Treatments
- Annealing: The thin film is heated to a specific temperature to improve its crystallinity, reduce defects, and enhance its mechanical and electrical properties.
- Surface Modification: Techniques such as plasma treatment or chemical functionalization may be used to alter the surface properties of the thin film for specific applications.
- Characterization: The thin film is analyzed using various techniques (e.g., X-ray diffraction, electron microscopy, spectroscopy) to ensure it meets the desired specifications in terms of thickness, composition, and properties.
-
Applications and Considerations
- Semiconductors: Thin films are crucial in the fabrication of semiconductor devices, where precise control over thickness and composition is essential for performance.
- Optical Coatings: Thin films are used to create anti-reflective coatings, mirrors, and filters, where optical properties such as transparency and reflectivity are critical.
- Flexible Electronics: Thin films of polymers and other materials are used in flexible solar cells, OLEDs, and other devices that require flexibility and lightweight properties.
- Barrier Layers: Thin films can act as barrier layers to protect substrates from environmental factors such as moisture, oxygen, and UV radiation.
In conclusion, the process of thin film making is a complex and highly controlled procedure that involves multiple steps, from substrate preparation to post-deposition treatments. The choice of deposition technique depends on the material, desired film properties, and application. Each method has its advantages and limitations, and the process must be carefully optimized to achieve the desired results.
Summary Table:
Step | Details |
---|---|
Substrate Preparation | Cleaning (ultrasonic, chemical, plasma) and surface treatment (etching, adhesion promoters). |
Deposition Techniques | PVD (evaporation, sputtering), CVD (thermal, PECVD), solution-based (spin coating, dip coating, LbL). |
Post-Deposition | Annealing, surface modification, and characterization (XRD, microscopy, spectroscopy). |
Applications | Semiconductors, optical coatings, flexible electronics, barrier layers. |
Interested in optimizing your thin film processes? Contact our experts today to get started!