The process of waste pyrolysis involves the thermal decomposition of organic materials such as plastics, biomass, tires, and municipal waste in the absence of oxygen. This process typically includes several key steps: pre-treatment of the waste (shredding, drying, and impurity removal), feeding the material into a pyrolysis reactor, heating it to high temperatures (400-900°C) to break down the waste into smaller components, and then separating and refining the resulting products (bio-oil, syngas, and bio-char). The process is highly efficient and environmentally friendly, as it reduces waste volume, produces usable energy, and minimizes harmful emissions. Below, the process is broken down into detailed steps and explained further.
Key Points Explained:
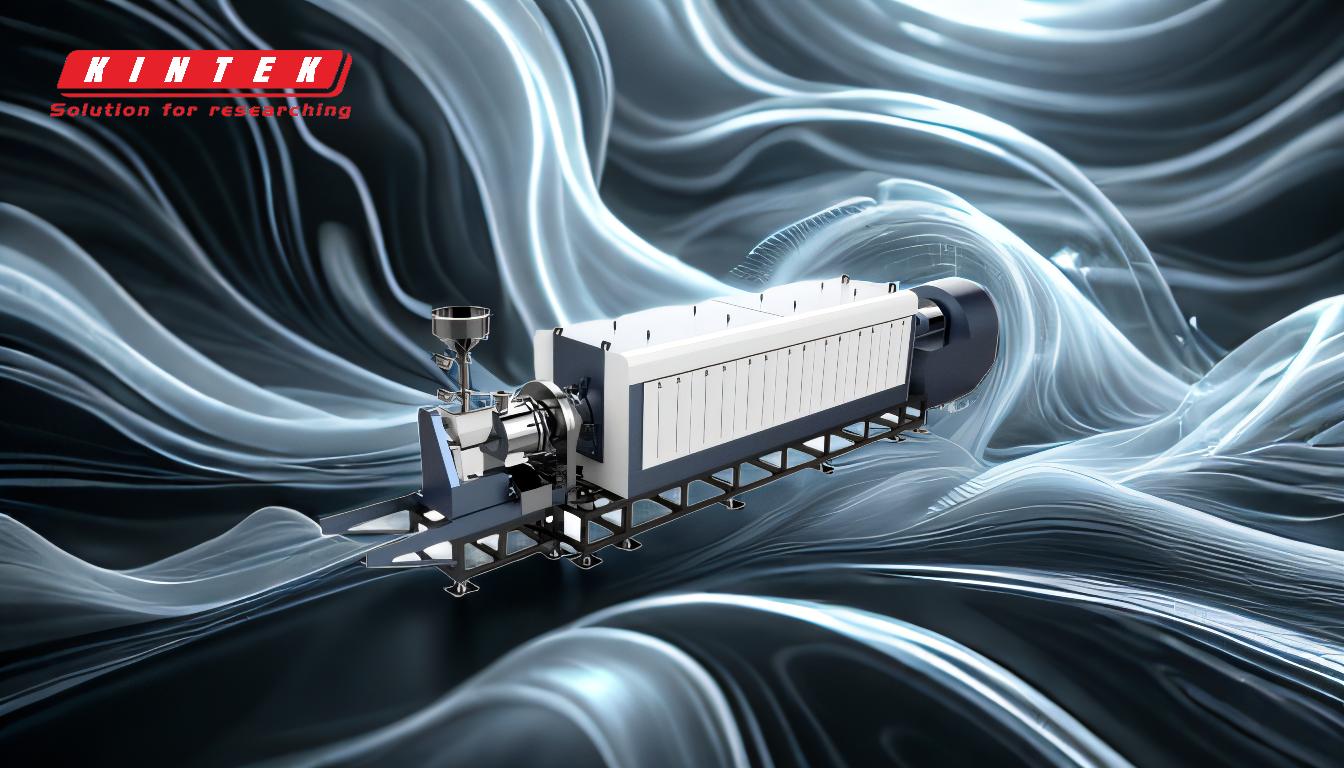
-
Pre-Treatment of Waste
- Shredding and Drying: Waste materials like plastics, tires, or biomass are first shredded into smaller pieces to facilitate uniform heating. Drying is essential to remove moisture, as excess water can interfere with the pyrolysis reaction.
- Impurity Removal: Non-organic materials such as metals, glass, and inert substances are separated to prevent contamination and ensure the purity of the pyrolysis products.
-
Feeding into the Pyrolysis Reactor
- The pre-treated waste is fed into a pyrolysis reactor, which can be a rotary kiln, fluidized bed furnace, or other specialized equipment. The reactor is designed to operate in an oxygen-free environment to prevent combustion and ensure thermal decomposition.
-
Heating and Thermal Decomposition
- The waste is heated to temperatures ranging from 400°C to 900°C, depending on the material and desired products. This high-temperature environment causes the waste to break down into smaller molecules through a process called thermal cracking.
- The absence of oxygen prevents combustion, ensuring that the waste decomposes into syngas, bio-oil, and bio-char instead of ash and CO2.
-
Product Separation
- Syngas: The gaseous byproduct of pyrolysis, consisting mainly of hydrogen, methane, and carbon monoxide, is separated and can be used as a fuel or further processed into biofuels.
- Bio-Oil: The liquid byproduct, also known as pyrolysis oil, is condensed from the vapor phase and can be refined for use as transportation fuel or in industrial applications.
- Bio-Char: The solid residue, bio-char, settles at the bottom of the reactor and can be used as a soil amendment, sorbent, or in other applications.
-
Cooling and Storage
- The pyrolysis products are cooled and stored in appropriate containers. Liquid products like bio-oil are transported to storage tanks, while syngas is purified and used as fuel for the pyrolysis process or other purposes.
-
Emission Control
- The flue gas generated during pyrolysis is treated using purification systems to remove harmful substances before being discharged into the atmosphere. This ensures that the process is environmentally friendly and compliant with regulations.
-
Energy Recovery and Efficiency
- The syngas produced during pyrolysis is often recycled to provide heat for the reactor, making the process self-sustaining and energy-efficient.
- The bio-oil and bio-char have high energy content and can be used as renewable energy sources, reducing reliance on fossil fuels.
-
Catalyst Use (Optional)
- In some cases, a catalyst is added to the pyrolysis chamber to enhance the breakdown of complex molecules and improve the quality of the end products. This is particularly common in plastic pyrolysis.
-
Industrial Applications
- Pyrolysis is widely used in industries to process waste rubber, tires, plastics, and sludge. The resulting products are valuable commodities that can be sold or reused, making pyrolysis a profitable waste management solution.
-
Safety and Control Systems
- Modern pyrolysis plants are equipped with advanced safety and control systems to monitor temperature, pressure, and other parameters, ensuring efficient and safe operation.
By following these steps, waste pyrolysis effectively transforms waste materials into valuable resources, contributing to waste reduction, energy recovery, and environmental sustainability.
Summary Table:
Step | Description |
---|---|
Pre-Treatment | Shredding, drying, and removing impurities from waste materials. |
Feeding into Reactor | Loading pre-treated waste into an oxygen-free pyrolysis reactor. |
Heating & Decomposition | Heating waste to 400-900°C for thermal cracking into smaller molecules. |
Product Separation | Separating syngas, bio-oil, and bio-char for various applications. |
Cooling & Storage | Cooling and storing products in appropriate containers. |
Emission Control | Treating flue gas to remove harmful substances before discharge. |
Energy Recovery | Recycling syngas to heat the reactor and using bio-oil/bio-char as energy sources. |
Catalyst Use (Optional) | Adding catalysts to enhance molecule breakdown and improve product quality. |
Industrial Applications | Processing waste rubber, tires, plastics, and sludge into valuable commodities. |
Safety & Control | Monitoring temperature, pressure, and other parameters for safe operation. |
Discover how waste pyrolysis can benefit your business—contact our experts today!