The production of steel by Electric Arc Furnace (EAF) involves the use of high-powered electric arcs to melt recycled ferrous scrap, transforming it into high-quality steel. This process is energy-efficient, environmentally friendly, and cost-effective compared to traditional blast furnace methods. EAFs generate intense heat through an electric arc between electrodes and the charged metal, reaching temperatures up to 1,800°C (or higher in lab conditions). The process is self-contained, requiring no secondary heat source, and can produce steel from 100% scrap material. EAFs are widely used in mini-mills and industrial settings for their scalability, smaller footprint, and ability to produce both carbon and alloy steels.
Key Points Explained:
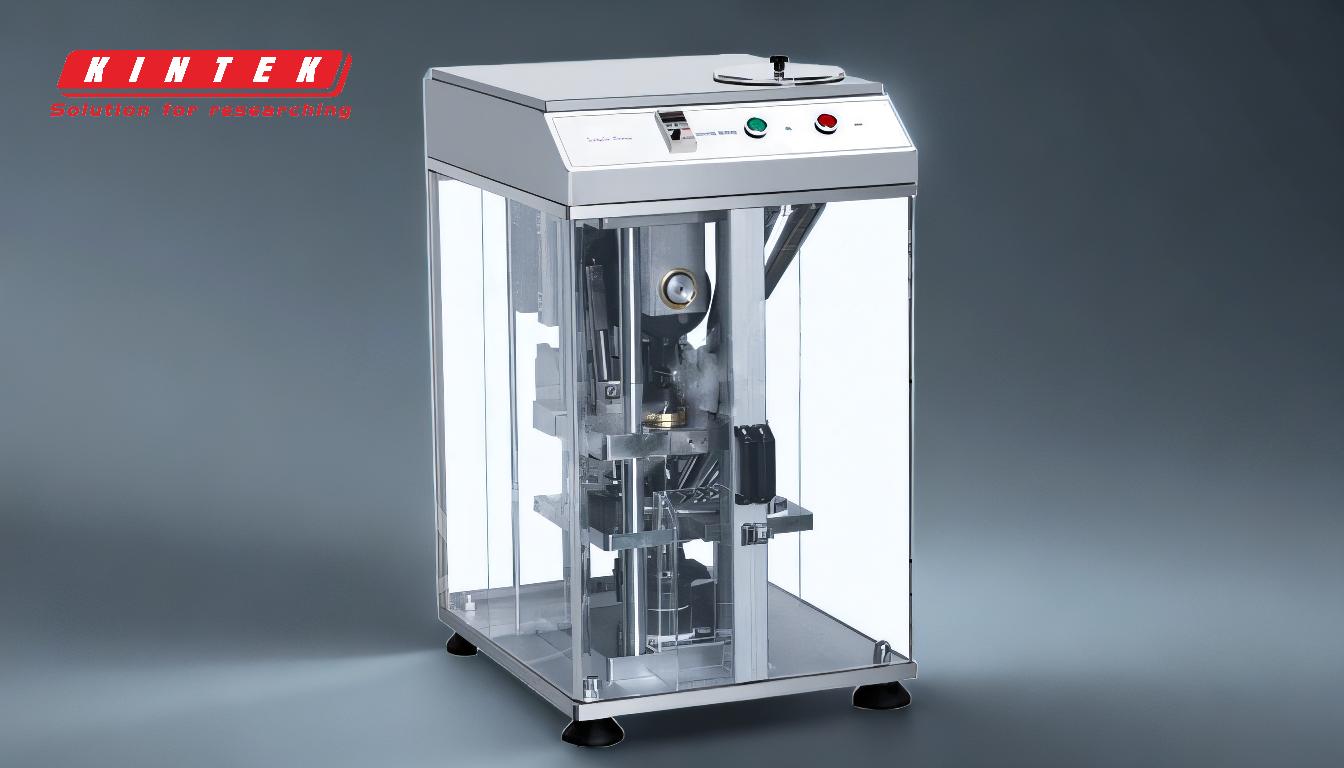
-
What is an Electric Arc Furnace (EAF)?
- An EAF is an industrial furnace that uses an electric arc to generate intense heat for melting metals.
- It operates by creating an electric arc between electrodes and the charged metal inside the furnace, producing temperatures up to 1,800°C (or higher in lab conditions).
- The process is self-contained, meaning it does not rely on external heat sources like combustion or coke.
-
How Does an EAF Work?
- Scrap metal is loaded into the furnace along with limestone to aid in slag formation.
- High-powered electric arcs are formed between the electrodes and the scrap metal, generating temperatures sufficient to melt the metal.
- The electric arc creates a plasma discharge, leading to rapid melting of the materials.
- The process typically requires 350 kWh to 370 kWh of energy per ton of scrap melted.
-
Advantages of EAF in Steel Production:
- Energy Efficiency: EAFs are more energy-efficient than blast furnaces because they do not require large amounts of fuel or coke for combustion.
- Environmental Benefits: EAFs can produce steel from 100% recycled scrap, reducing the need for virgin ores and minimizing environmental impact.
- Scalability: EAFs can be scaled down to operate in mini-mills, making them suitable for smaller production facilities.
- Cost-Effectiveness: The ability to use scrap metal as the primary raw material reduces production costs.
-
Applications of EAF-Produced Steel:
- EAFs are primarily used to produce carbon steel and alloy steel.
- The process is ideal for re-melting steel scrap and producing cast-iron products.
- EAFs are widely used in industries requiring high-temperature operations for ferrous and non-ferrous metals.
-
Comparison with Blast Furnaces:
- Footprint: EAFs have a smaller physical footprint compared to blast furnaces.
- Flexibility: EAFs can be started and stopped more easily, providing greater operational flexibility.
- Purity: EAFs can achieve high purities without the continuous addition of coke, making them suitable for producing high-quality steel.
-
Temperature and Efficiency:
- EAFs can generate temperatures between 3,000°C and 3,500°C during low-tension operations, ensuring efficient melting of materials.
- The high temperatures and rapid melting process make EAFs ideal for industrial-scale steel production.
-
Role of Scrap Metal:
- Scrap metal is the primary raw material for EAFs, making the process highly sustainable.
- The use of scrap reduces the reliance on mining and processing virgin ores, contributing to a circular economy.
By leveraging the unique capabilities of EAFs, steel producers can achieve efficient, cost-effective, and environmentally friendly steel production, making this technology a cornerstone of modern metallurgy.
Summary Table:
Key Aspect | Details |
---|---|
Process | Uses high-powered electric arcs to melt recycled ferrous scrap. |
Temperature | Reaches up to 1,800°C (or higher in lab conditions). |
Energy Efficiency | Requires 350-370 kWh per ton of scrap, making it more efficient than blast furnaces. |
Environmental Benefits | Produces steel from 100% recycled scrap, reducing reliance on virgin ores. |
Applications | Ideal for carbon steel, alloy steel, and cast-iron products. |
Footprint | Smaller physical footprint compared to blast furnaces. |
Scalability | Suitable for mini-mills and smaller production facilities. |
Ready to optimize your steel production? Contact us today to learn more about Electric Arc Furnaces!