A laboratory furnace is a versatile and essential piece of equipment in scientific and industrial settings, designed to perform a wide range of heat treatment processes. Its primary purposes include drying, baking, and curing samples, as well as advanced heat treatments like annealing, quenching, and sintering. These processes are crucial for altering the physical or chemical properties of materials, ensuring optimal performance in various applications. Laboratory furnaces are widely used in fields such as materials science, metallurgy, and aerospace, where precise temperature control and uniform heating are required to achieve desired outcomes.
Key Points Explained:
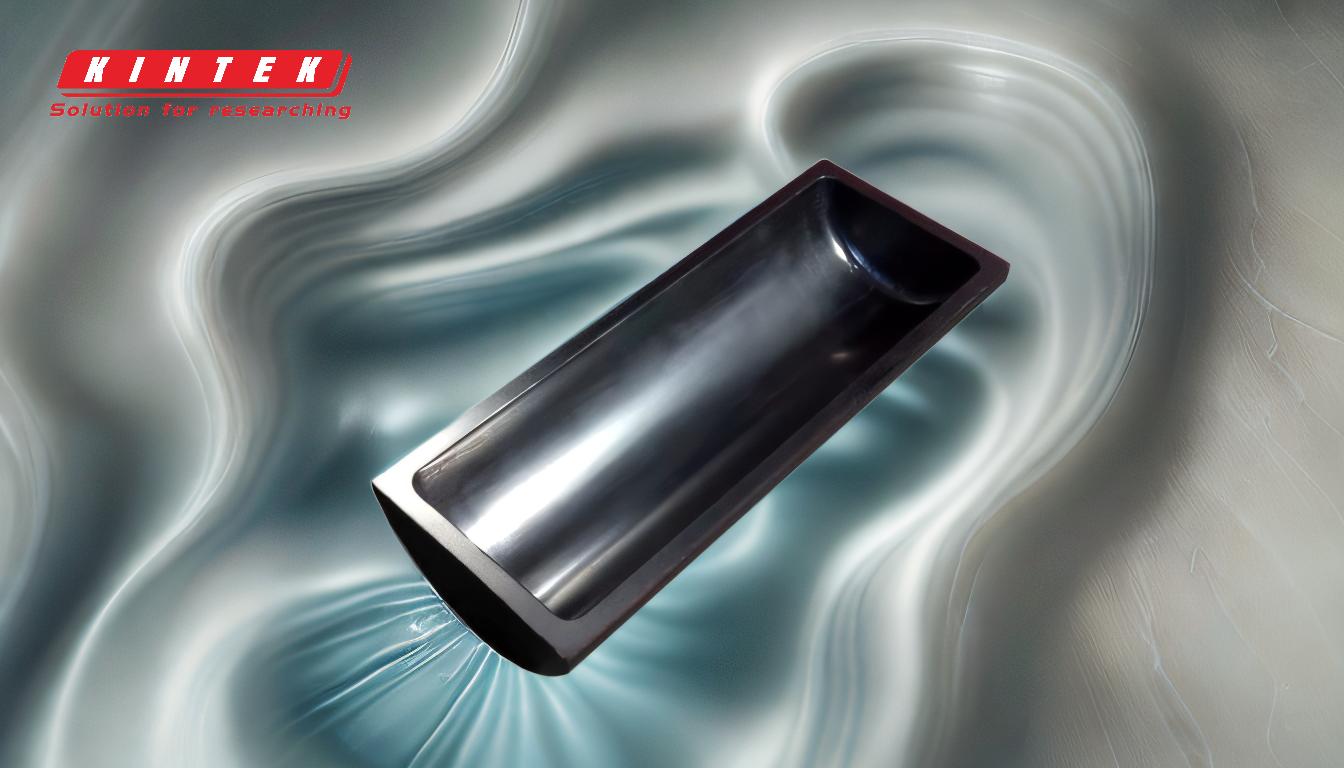
-
Drying, Baking, and Curing:
- Drying: A laboratory furnace is used to remove moisture from samples, which is essential for preparing materials for further analysis or processing. This is particularly important in industries like pharmaceuticals and food science, where moisture content can affect product quality.
- Baking: This involves heating samples without dehumidification, often used to harden or set materials. For example, in ceramics, baking helps solidify the material without altering its chemical composition.
- Curing: This process chemically or physically alters a sample, often to improve its strength, durability, or other properties. Curing is commonly used in polymer and composite manufacturing.
-
Advanced Heat Treatment Processes:
- Vacuum Heating: This process involves heating materials in a vacuum to prevent oxidation and contamination. It is widely used in aerospace and metallurgy to enhance material properties.
- Quenching: Rapid cooling of materials to achieve specific mechanical properties, such as increased hardness. This is critical in the production of tools and machinery components.
- Tempering: A process that reduces brittleness in materials by reheating them after quenching, balancing hardness and toughness.
- Annealing: Heating and then slowly cooling materials to relieve internal stresses and improve ductility. This is essential in metalworking and glass manufacturing.
- Carburizing and Nitriding: Surface hardening techniques that introduce carbon or nitrogen into the surface of metals, enhancing wear resistance and durability.
-
Specialized Applications:
- Powder Metallurgy Sintering: Laboratory furnaces are used to bond metal powders into solid components through heat and pressure, a process critical in manufacturing complex parts with high precision.
- Brazing of Aerospace Workpieces: This involves joining metal components using a filler material, which is melted and flowed into the joint. The high-temperature capabilities of a laboratory furnace ensure strong, reliable bonds.
-
Material Performance Enhancement:
- The vacuum heat treatment process in a laboratory furnace significantly improves the performance of treated materials. By preventing oxidation and contamination, it allows for the full utilization of material properties, leading to stronger, more durable, and higher-quality products.
-
Versatility and Precision:
- Laboratory furnaces are designed to provide precise temperature control and uniform heating, making them indispensable in research and industrial applications. Their ability to perform a wide range of processes under controlled conditions ensures consistent and reliable results.
In summary, a laboratory furnace is a critical tool for a variety of heat treatment processes, enabling the modification and enhancement of material properties for numerous applications. Its versatility, precision, and ability to perform advanced treatments make it an invaluable asset in scientific research and industrial manufacturing.
Summary Table:
Purpose | Description |
---|---|
Drying | Removes moisture from samples, crucial for pharmaceuticals and food science. |
Baking | Hardens or sets materials without altering chemical composition. |
Curing | Chemically or physically alters samples to improve strength and durability. |
Vacuum Heating | Prevents oxidation and contamination, enhancing material properties. |
Quenching | Rapidly cools materials to increase hardness. |
Tempering | Reduces brittleness by reheating after quenching. |
Annealing | Relieves internal stresses and improves ductility. |
Carburizing/Nitriding | Surface hardening techniques for wear resistance. |
Sintering | Bonds metal powders into solid components for precision manufacturing. |
Brazing | Joins metal components using high-temperature filler materials. |
Unlock the full potential of your materials with a laboratory furnace—contact us today to learn more!