Chemical vapor deposition (CVD) is a versatile and widely used technique for depositing thin films onto substrates through chemical reactions in the vapor phase. Its primary purpose is to enhance surface properties, such as smoothness, electrical and thermal conductivity, and compatibility with other materials. CVD can also be tailored to produce nanometer-thin coatings with specific characteristics, depending on the precursors used. Plasma-enhanced chemical vapor deposition (PECVD) is a variant that enables efficient reactions at lower temperatures, making it suitable for temperature-sensitive materials. Overall, CVD is a critical process in industries like electronics, optics, and materials science, where precise control over surface properties is essential.
Key Points Explained:
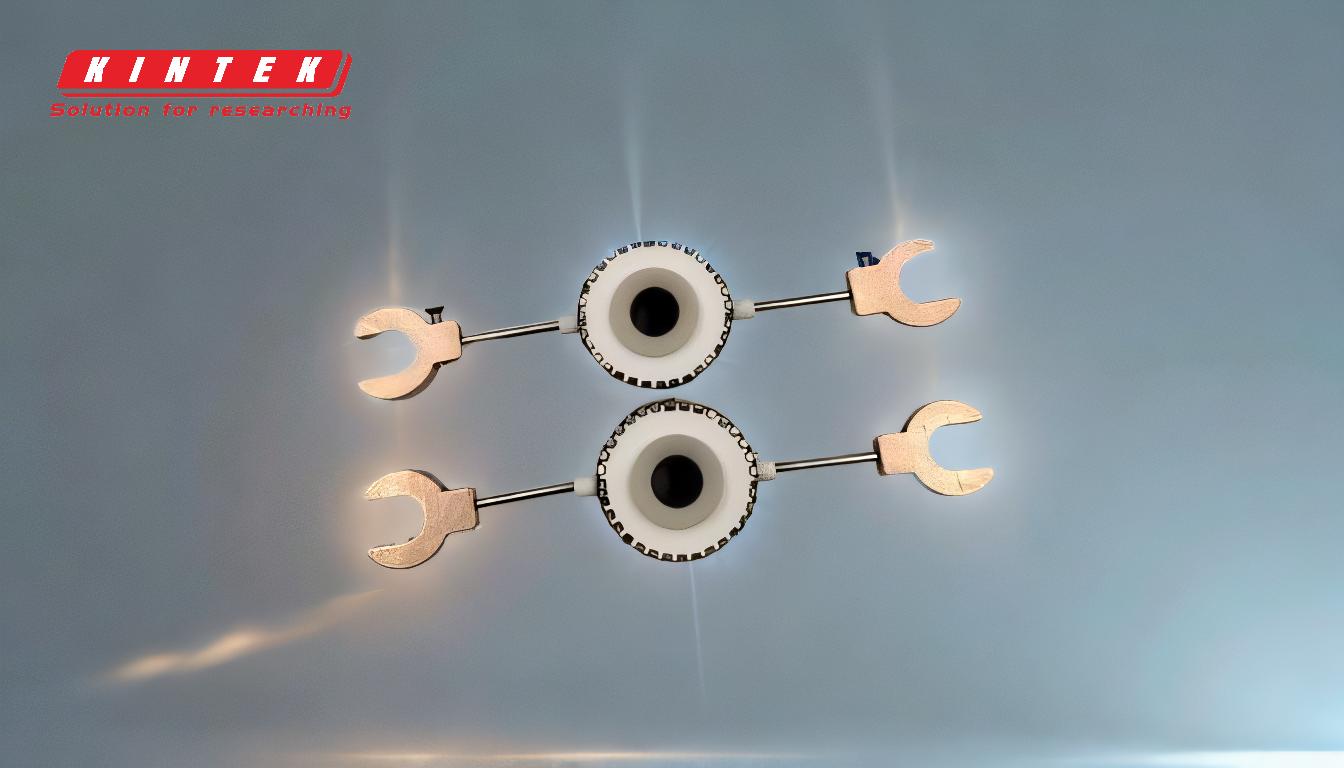
-
Definition and Mechanism of CVD:
- Chemical vapor deposition (CVD) involves depositing a solid film on a heated surface through chemical reactions in the vapor phase. The depositing species can be atoms, molecules, or a combination of both.
- Unlike physical deposition methods (e.g., evaporation or sputtering), CVD relies on gas-phase and gas–solid chemical reactions to produce thin films. This chemical approach allows for greater control over film composition and properties.
-
Enhancement of Surface Properties:
- CVD improves surface properties by creating smoother surfaces, enhancing electrical and thermal conductivity, and improving compatibility with other materials.
- The even buildup of coating material on the substrate's surface ensures uniformity, which is critical for applications in electronics, optics, and materials science.
-
Plasma-Enhanced Chemical Vapor Deposition (PECVD):
- PECVD is a variant of CVD that uses plasma to enhance the efficiency of chemical reactions at lower temperatures. This makes it suitable for temperature-sensitive materials that cannot withstand the high temperatures required in traditional CVD.
- PECVD is particularly useful for creating nanometer-thin coatings with tailored properties, such as controlled wetting characteristics or specific electrical properties.
-
Customization of Thin Films:
- CVD allows for the customization of thin films by selecting precursors with desired properties. This enables the production of coatings with specific chemical, electrical, or thermal characteristics.
- For example, PECVD can be used to create hydrophobic or hydrophilic surfaces by controlling the surface chemistry of the substrate.
-
Applications of CVD:
- CVD is widely used in industries such as semiconductors, optics, and materials science. It is essential for manufacturing integrated circuits, solar cells, and protective coatings.
- The ability to deposit thin films with precise control over composition and thickness makes CVD a cornerstone of modern technology.
-
Advantages Over Physical Deposition Methods:
- CVD offers several advantages over physical deposition methods, including better adhesion, higher purity, and the ability to deposit complex materials like ceramics and polymers.
- The chemical nature of CVD allows for the creation of films with unique properties that are difficult to achieve through physical methods.
By leveraging the principles of CVD and its variants like PECVD, industries can achieve precise control over surface properties and create materials with tailored characteristics for specific applications.
Summary Table:
Key Aspect | Details |
---|---|
Definition | Deposits thin films via chemical reactions in the vapor phase. |
Primary Purpose | Enhances surface smoothness, conductivity, and material compatibility. |
PECVD Variant | Uses plasma for efficient reactions at lower temperatures. |
Customization | Tailors films using specific precursors for desired properties. |
Applications | Used in semiconductors, optics, and materials science. |
Advantages | Better adhesion, higher purity, and ability to deposit complex materials. |
Learn how CVD can transform your material properties—contact our experts today!