Physical vapor deposition (PVD) is a versatile and widely used thin-film coating process that involves the physical transfer of material from a source to a substrate in a vacuum environment. The primary purpose of PVD is to deposit thin, uniform, and high-quality coatings onto surfaces to enhance their properties, such as wear resistance, corrosion resistance, electrical conductivity, optical performance, and aesthetic appeal. This process is essential in industries like electronics, aerospace, automotive, and medical devices, where precise and durable coatings are required. PVD techniques, such as sputtering and evaporation, allow for the deposition of a wide range of materials, including metals, ceramics, and composites, with excellent adhesion and control over film thickness and composition.
Key Points Explained:
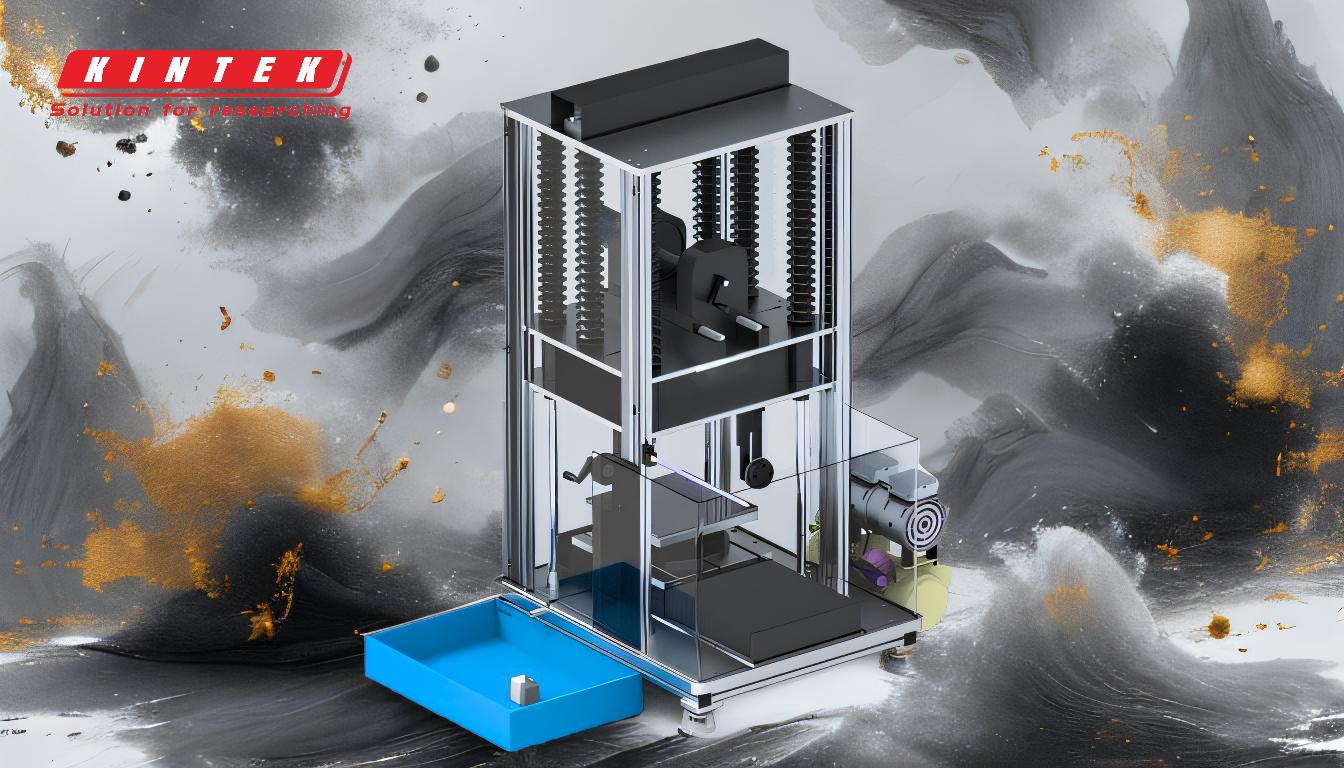
-
Thin-Film Deposition:
- PVD is primarily used to deposit thin films, typically ranging from a few nanometers to several micrometers in thickness. These films are applied to enhance the surface properties of substrates, such as improving hardness, reducing friction, or providing decorative finishes.
- The process ensures uniform and precise coating, which is critical for applications requiring high performance and reliability.
-
Enhanced Surface Properties:
- Wear Resistance: PVD coatings, such as titanium nitride (TiN) or diamond-like carbon (DLC), significantly improve the wear resistance of tools, molds, and components, extending their lifespan.
- Corrosion Resistance: Coatings like chromium nitride (CrN) or aluminum oxide (Al2O3) protect surfaces from environmental degradation, making them suitable for harsh conditions.
- Electrical Conductivity: PVD is used to deposit conductive materials like gold, silver, or copper in electronics for interconnects, contacts, and circuits.
- Optical Performance: PVD coatings are applied to lenses, mirrors, and displays to enhance reflectivity, anti-reflectivity, or filtering properties.
-
Versatility in Material Selection:
- PVD can deposit a wide range of materials, including metals (e.g., aluminum, titanium), ceramics (e.g., oxides, nitrides), and composites. This versatility makes it suitable for diverse applications across industries.
- The process allows for the creation of multilayer or alloy coatings with tailored properties by combining different materials.
-
High-Quality and Durable Coatings:
- PVD coatings exhibit excellent adhesion to substrates, ensuring long-lasting performance even under extreme conditions.
- The vacuum environment minimizes contamination, resulting in high-purity coatings with consistent quality.
-
Applications Across Industries:
- Electronics: PVD is used to deposit thin films for semiconductors, solar cells, and displays.
- Aerospace: Coatings are applied to turbine blades and other components to withstand high temperatures and wear.
- Automotive: PVD enhances the durability and appearance of engine parts, decorative trims, and cutting tools.
- Medical Devices: Biocompatible coatings are deposited on implants and surgical instruments to improve performance and safety.
-
Environmental and Economic Benefits:
- PVD is a clean and environmentally friendly process, as it does not involve hazardous chemicals or produce harmful byproducts.
- The durability of PVD coatings reduces the need for frequent replacements, leading to cost savings and reduced material waste.
-
Process Techniques:
- Sputtering: A common PVD method where high-energy ions bombard a target material, ejecting atoms that deposit onto the substrate.
- Evaporation: Involves heating a material in a vacuum until it vaporizes and condenses onto the substrate.
- Both techniques allow for precise control over coating thickness, composition, and microstructure.
In summary, physical vapor deposition serves as a critical technology for creating high-performance coatings that enhance the functionality, durability, and appearance of materials across various industries. Its ability to deposit a wide range of materials with exceptional precision and quality makes it indispensable in modern manufacturing and engineering.
Summary Table:
Key Aspect | Details |
---|---|
Purpose | Deposits thin, uniform coatings to enhance surface properties. |
Key Benefits | Wear resistance, corrosion resistance, electrical conductivity, optical performance. |
Materials Used | Metals (e.g., aluminum, titanium), ceramics (e.g., oxides, nitrides), composites. |
Applications | Electronics, aerospace, automotive, medical devices. |
Techniques | Sputtering, evaporation. |
Environmental Benefits | Clean process, no hazardous chemicals, reduces material waste. |
Learn how PVD can transform your materials—contact our experts today!