PVD (Physical Vapor Deposition) coating is a versatile and advanced surface treatment technology used to enhance the properties of various materials. It involves depositing a thin, pure, and durable coating onto a substrate in a vacuum environment. The process is characterized by low processing temperatures, making it suitable for a wide range of substrates, including those sensitive to high heat. PVD coatings are known for their precision, environmental friendliness, and ability to improve wear resistance, corrosion resistance, and aesthetic appeal. This technology is widely used in industries such as automotive, aerospace, medical devices, and consumer electronics.
Key Points Explained:
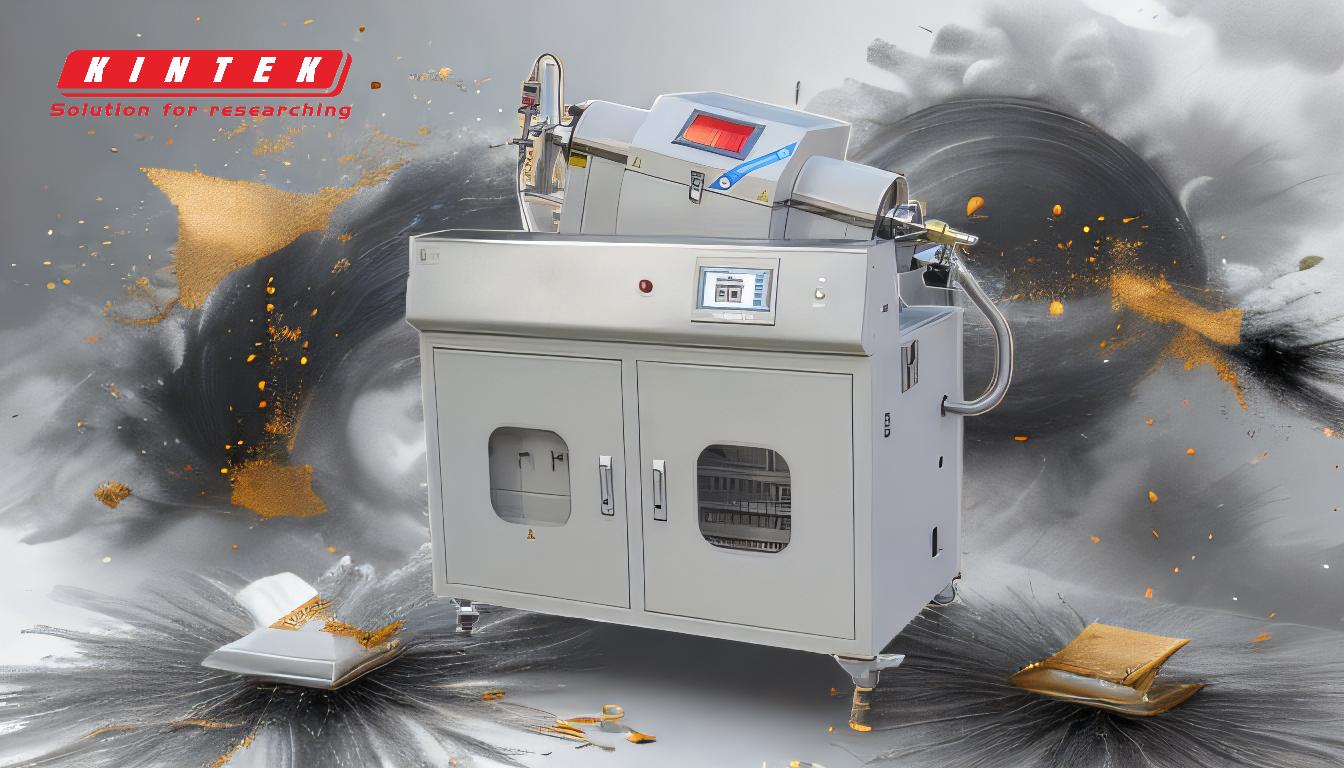
-
Low Processing Temperatures:
- PVD coating operates at relatively low temperatures, typically between 385°F and 950°F. This makes it ideal for materials that cannot withstand high heat, such as certain plastics, composites, and heat-sensitive metals.
- The low-temperature process minimizes the risk of thermal distortion or degradation of the substrate, ensuring the integrity of the base material.
-
Thin and Uniform Coatings:
- PVD coatings are extremely thin, usually ranging from 2 to 5 microns in thickness. This precision allows for close tolerances, making it suitable for applications where dimensional accuracy is critical.
- The atom-by-atom deposition process ensures a uniform and pure coating, free from impurities or defects.
-
Versatility in Substrate Compatibility:
- PVD coating can be applied to a wide variety of substrates, including metals, ceramics, glass, and polymers. This versatility makes it a preferred choice for diverse industries.
- The ability to coat different materials without compromising their properties expands its application range, from cutting tools to decorative finishes.
-
Environmental Friendliness:
- The PVD process is conducted in a vacuum chamber, which eliminates the release of harmful chemicals or byproducts into the environment.
- Compared to traditional coating methods like electroplating, PVD is more sustainable and aligns with modern environmental regulations.
-
Enhanced Material Properties:
- PVD coatings significantly improve the wear resistance, hardness, and corrosion resistance of materials. This extends the lifespan of components and reduces maintenance costs.
- The coatings also provide aesthetic benefits, such as a metallic or colored finish, which is often used in consumer products like watches, smartphones, and automotive trim.
-
Process Steps:
- The PVD coating process involves five main steps:
- Placing the target material in the vacuum chamber: The material to be vaporized is positioned inside the chamber.
- Evacuating the chamber: A high-vacuum environment is created to ensure a clean and controlled deposition process.
- Bombarding the target material: The target is vaporized using electrons, ions, or photons.
- Condensing the vaporized material: The vaporized atoms are deposited onto the substrate to form a thin film.
- Purging the chamber: Inert gases are used to remove any residual vapors, ensuring a clean finish.
- The PVD coating process involves five main steps:
-
Applications Across Industries:
- Automotive: Used for coating engine components, decorative trims, and tools to enhance durability and appearance.
- Aerospace: Applied to turbine blades and other critical components to improve performance under extreme conditions.
- Medical Devices: Used for surgical instruments and implants to ensure biocompatibility and resistance to wear.
- Consumer Electronics: Provides scratch-resistant and aesthetically pleasing finishes for devices like smartphones and laptops.
In summary, PVD coating is a highly effective and versatile technology that offers numerous benefits, including low-temperature processing, thin and uniform coatings, environmental sustainability, and enhanced material properties. Its wide range of applications across various industries underscores its importance as a modern surface treatment solution.
Summary Table:
Key Benefits of PVD Coating | Details |
---|---|
Low Processing Temperatures | 385°F–950°F, ideal for heat-sensitive materials. |
Thin & Uniform Coatings | 2–5 microns, precise and defect-free. |
Versatile Substrate Compatibility | Works on metals, ceramics, glass, and polymers. |
Environmental Friendliness | No harmful byproducts, sustainable process. |
Enhanced Material Properties | Improves wear, corrosion resistance, and aesthetics. |
Wide Industry Applications | Automotive, aerospace, medical devices, electronics. |
Unlock the potential of PVD coating for your materials—contact our experts today!