A pyrolysis plant is a specialized facility designed to convert organic materials such as biomass, plastics, rubber, and waste tires into valuable products like bio-oil, biochar, and syngas through the process of pyrolysis. This thermochemical decomposition occurs in the absence of oxygen, typically at temperatures ranging from 400°C to 900°C. The plant plays a crucial role in waste management by recycling materials that would otherwise contribute to landfill waste, while also producing energy and industrial resources. Additionally, pyrolysis plants are environmentally friendly, cost-effective, and capable of large-scale industrial production, making them a sustainable solution for waste utilization and resource recovery.
Key Points Explained:
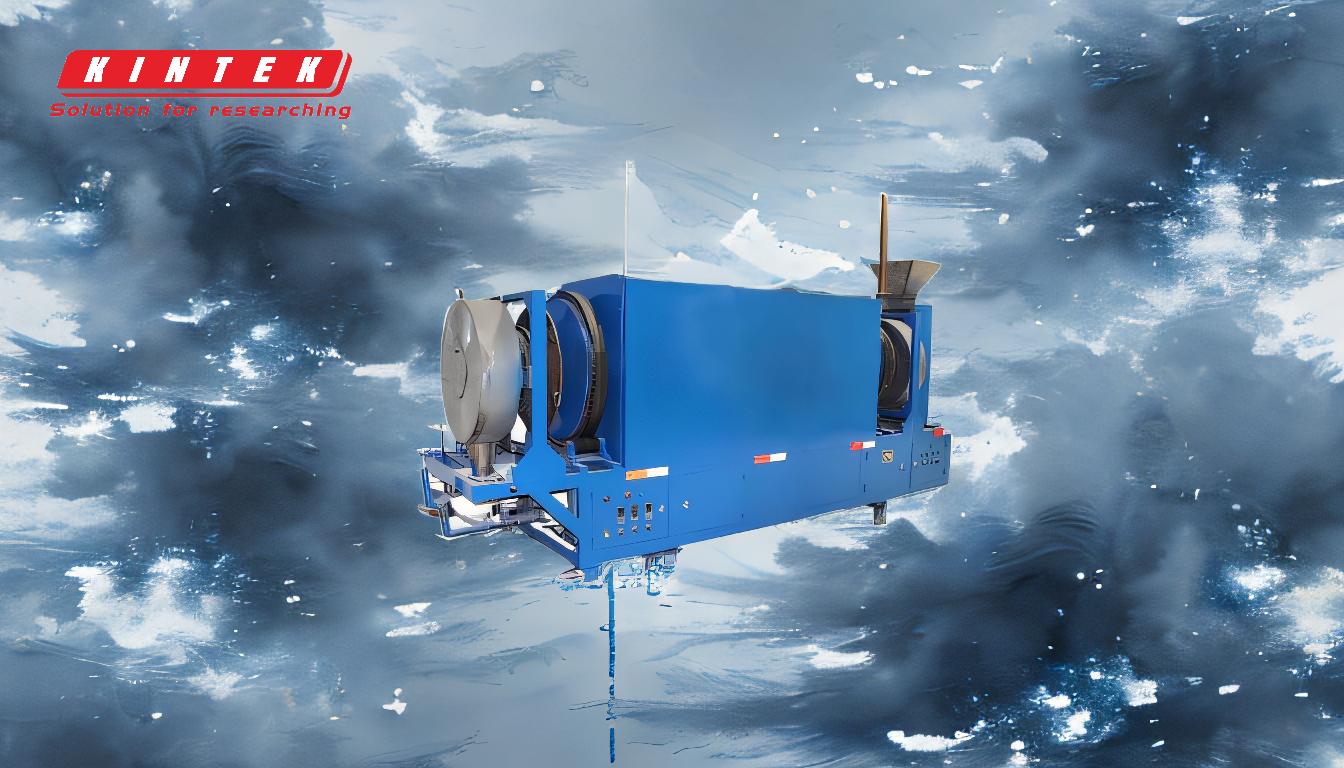
-
Conversion of Organic Waste into Valuable Products
- Pyrolysis plants are designed to process organic materials such as biomass, plastics, rubber, and waste tires.
- Through pyrolysis, these materials are thermally decomposed in the absence of oxygen, producing three main outputs:
- Bio-oil: A liquid fuel that can be used directly or refined for industrial or transportation purposes.
- Biochar: A carbon-rich solid product used as a soil amendment, sorbent, or in other industrial applications.
- Syngas: A gaseous mixture that can be used as fuel or further processed into biofuels.
-
Waste Management and Recycling
- Pyrolysis plants play a significant role in reducing waste, particularly for materials like waste tires and plastics that are difficult to recycle through conventional methods.
- For example, rubber pyrolysis plants specifically target used or damaged tires, converting them into fuel, asphalt, and other products, thereby reducing landfill waste.
- This process helps address environmental concerns by repurposing non-biodegradable materials and reducing pollution.
-
Environmental Benefits
- Pyrolysis plants are equipped with systems like de-dusting and hydroseal to minimize pollution and emissions.
- The process itself is environmentally friendly, as it prevents the release of harmful gases and reduces the carbon footprint associated with waste disposal.
- By converting waste into usable energy and products, pyrolysis contributes to a circular economy and sustainable resource management.
-
Economic Advantages
- Pyrolysis plants are cost-effective to operate, with low production costs and high profitability.
- The products generated, such as bio-oil and syngas, have high market value and can be sold directly or further refined for additional revenue.
- The rotary running mechanism ensures efficient heating and energy savings, further enhancing the economic viability of the plant.
-
Industrial and Large-Scale Applications
- Pyrolysis plants are designed for industrial-scale production, making them suitable for large volumes of waste processing.
- They are versatile and can handle a wide range of organic materials, making them applicable in various industries, including energy, agriculture, and manufacturing.
- The ability to process diverse feedstocks ensures flexibility and adaptability to different waste streams.
-
Technical Operation and Safety
- The pyrolysis process involves heating materials in a reactor at high temperatures (400°C to 900°C) in the absence of oxygen.
- The plant includes advanced safety and control systems to ensure efficient and safe operation.
- The process is highly controlled to optimize product yields and maintain operational stability.
In summary, pyrolysis plants serve a dual purpose of waste management and resource recovery, offering environmental, economic, and industrial benefits. They are a sustainable solution for converting organic waste into valuable products, reducing landfill dependency, and contributing to a cleaner, more efficient energy and manufacturing landscape.
Summary Table:
Key Aspect | Details |
---|---|
Input Materials | Biomass, plastics, rubber, waste tires |
Output Products | Bio-oil, biochar, syngas |
Temperature Range | 400°C to 900°C |
Environmental Benefits | Reduces landfill waste, minimizes emissions, supports circular economy |
Economic Advantages | Cost-effective, high profitability, energy-efficient |
Industrial Applications | Energy, agriculture, manufacturing, large-scale waste processing |
Safety Features | Advanced control systems, optimized for safe and efficient operation |
Ready to transform waste into valuable resources? Contact us today to learn more about pyrolysis plants!