E-beam (electron beam) evaporation is a specialized form of physical vapor deposition (PVD) that utilizes a high-energy electron beam to vaporize and deposit materials onto a substrate. This process is particularly effective for materials with high melting points, such as gold and silicon dioxide, and offers higher deposition rates compared to other PVD methods like sputtering or resistive thermal evaporation. The process occurs in a high-vacuum environment, ensuring a clean and controlled deposition of thin, dense coatings. E-beam evaporation is widely used in industries requiring precise and high-quality thin-film coatings, such as optics, electronics, and semiconductors.
Key Points Explained:
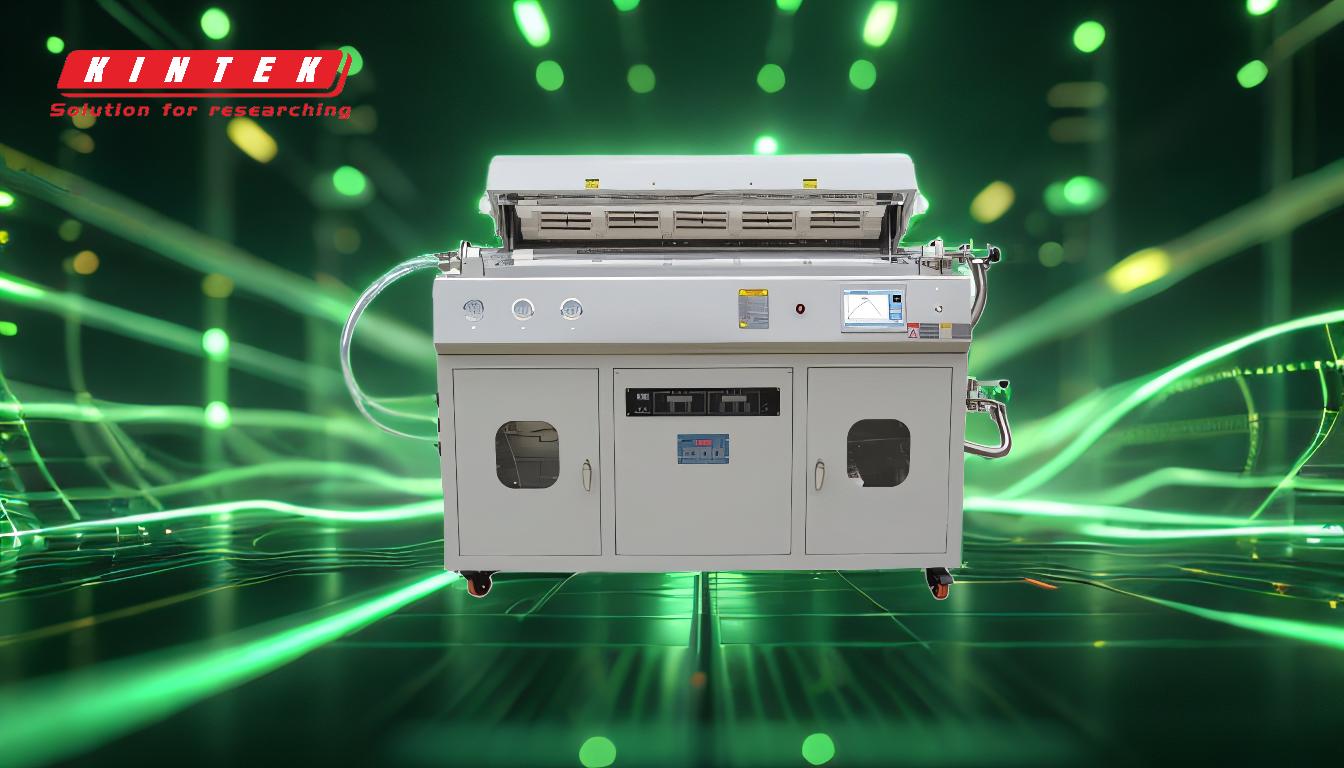
-
Definition and Mechanism of E-Beam Evaporation:
- E-beam evaporation is a thermal evaporation process where a high-energy electron beam is directed at the source material, causing it to vaporize. The vaporized material then condenses onto a substrate, forming a thin, dense coating.
- This method is a subset of physical vapor deposition (PVD), which involves the transfer of material at the atomic or molecular level under vacuum conditions.
-
High Melting Point Materials:
- One of the standout features of e-beam evaporation is its ability to handle materials with very high melting temperatures, such as gold, silicon dioxide, and refractory metals. The intense energy of the electron beam allows for the efficient evaporation of these materials, which would be challenging to process using other methods.
-
High Vacuum Environment:
- The process takes place in a high-vacuum chamber, typically at pressures of 10^-5 to 10^-7 Torr. This vacuum environment minimizes contamination and ensures that the vaporized material travels in a straight line to the substrate, resulting in a uniform and high-quality coating.
-
Higher Deposition Rates:
- E-beam evaporation offers significantly higher deposition rates compared to other PVD techniques like sputtering or resistive thermal evaporation. This makes it a preferred choice for applications requiring thick coatings or high throughput.
-
Applications in Optical Components:
- The process is particularly useful in the optical industry, where it is used to deposit thin films that modify the optical properties of substrates. These coatings can enhance reflectivity, reduce glare, or provide anti-reflective properties, depending on the specific requirements.
-
Advantages Over Other PVD Methods:
- Precision and Control: The focused electron beam allows for precise control over the evaporation process, enabling the deposition of very thin and uniform layers.
- Material Versatility: The ability to evaporate high melting point materials expands the range of applications, including those in high-temperature environments.
- Clean Process: The high-vacuum environment ensures a clean deposition process, free from contaminants that could affect the quality of the coating.
-
Challenges and Considerations:
- Equipment Cost: The specialized equipment required for e-beam evaporation, including the high-vacuum chamber and electron beam gun, can be expensive.
- Complexity: The process requires careful control of parameters such as beam current, voltage, and substrate temperature, which can add to the complexity of the operation.
- Material Limitations: While e-beam evaporation is versatile, it may not be suitable for all materials, particularly those that are sensitive to high-energy electron bombardment.
In summary, e-beam evaporation is a highly effective PVD method that offers unique advantages for depositing thin films, especially for materials with high melting points. Its ability to produce high-quality, uniform coatings at relatively high deposition rates makes it a valuable tool in various high-tech industries.
Summary Table:
Key Aspect | Details |
---|---|
Process | High-energy electron beam vaporizes materials, depositing them on substrates. |
Materials | Ideal for high melting point materials like gold, silicon dioxide, and refractory metals. |
Environment | High-vacuum chamber (10^-5 to 10^-7 Torr) ensures clean, contamination-free coatings. |
Deposition Rate | Higher rates compared to sputtering or resistive thermal evaporation. |
Applications | Optics (reflectivity, anti-reflective coatings), electronics, semiconductors. |
Advantages | Precision, material versatility, clean process, and high-quality coatings. |
Challenges | High equipment cost, process complexity, and material limitations. |
Discover how e-beam evaporation can elevate your thin-film deposition process—contact our experts today!