Biomass pyrolysis is a thermal decomposition process that occurs in the absence of oxygen, converting biomass into biochar, bio-oil, and syngas. The process is influenced by several factors, including temperature, heating rate, residence time, and the moisture content of the biomass. The yield and quality of the products depend on these parameters, with low temperatures favoring char production, moderate temperatures and high heating rates favoring liquid products, and high temperatures favoring gas production. The process involves pre-treatment, pyrolysis, discharging, and de-dusting stages, each critical for optimizing the efficiency and safety of the pyrolysis furnace. Proper control of operational parameters is essential to achieve the desired end products.
Key Points Explained:
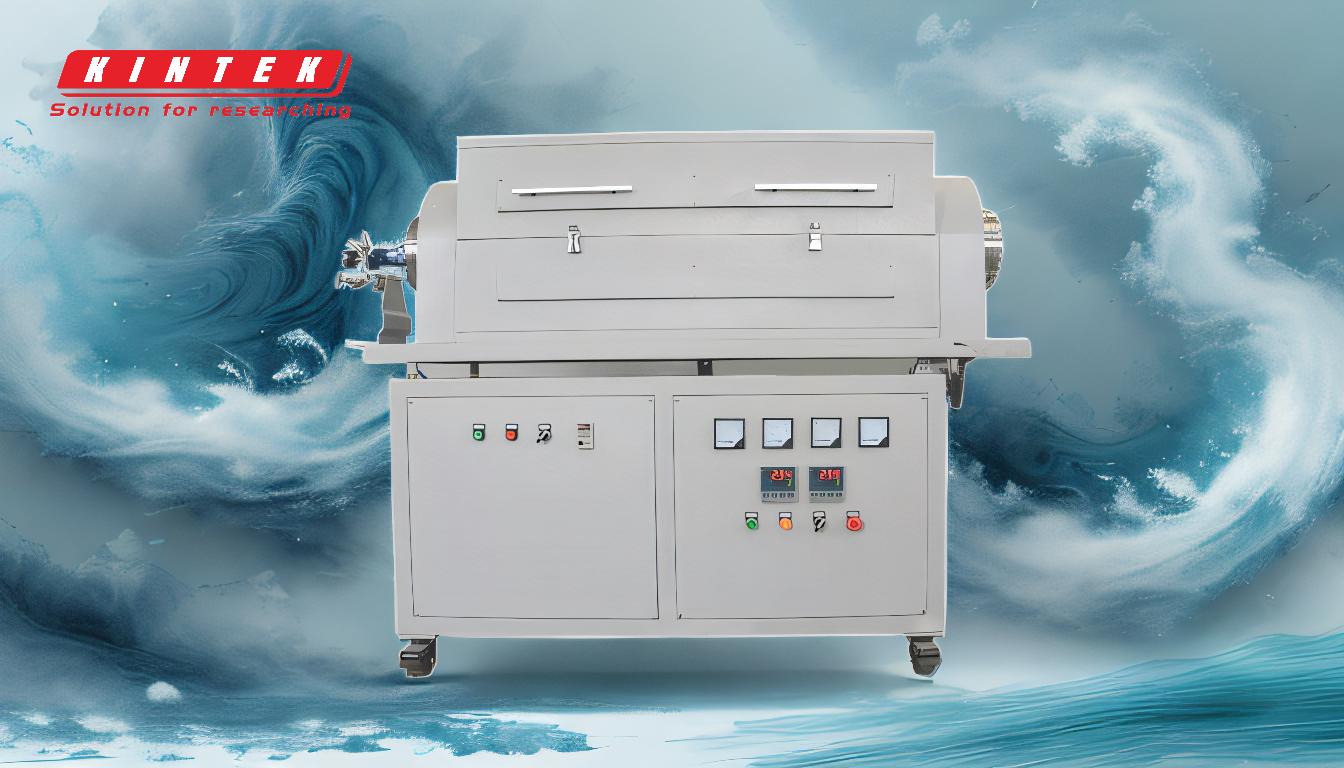
-
Definition of Biomass Pyrolysis:
- Biomass pyrolysis is a thermochemical process where organic materials are decomposed at elevated temperatures in the absence of oxygen. This process breaks down complex organic compounds into simpler molecules, resulting in three main products: biochar (solid), bio-oil (liquid), and syngas (gas).
-
Stages of Biomass Pyrolysis:
- Pre-treatment: This involves drying the biomass to reduce moisture content and crushing it to a suitable size for efficient pyrolysis. High moisture content can hinder the process by requiring more energy to heat the biomass.
- Pyrolysis: The biomass is heated to temperatures typically ranging from 300°C to 800°C, depending on the desired products. During this stage, the biomass undergoes thermal decomposition, producing biochar, bio-oil, and syngas.
- Discharging: After pyrolysis, the biochar is cooled and collected. Proper cooling is essential to prevent further reactions and ensure the stability of the biochar.
- De-dusting: The exhaust gases from the pyrolysis process are cleaned to remove particulate matter and harmful substances, ensuring compliance with environmental regulations.
-
Factors Influencing Pyrolysis:
- Temperature: The temperature is a critical factor that determines the distribution of products. Low temperatures (300°C–400°C) favor the production of biochar, moderate temperatures (400°C–600°C) favor bio-oil, and high temperatures (>600°C) favor syngas production.
- Heating Rate: A high heating rate promotes the formation of liquid products (bio-oil), while a low heating rate favors the production of biochar.
- Residence Time: The time that the biomass spends in the pyrolysis reactor affects the extent of decomposition. Short residence times are preferred for bio-oil production, while longer residence times favor gas production.
- Moisture Content: High moisture content in the biomass can reduce the efficiency of the pyrolysis process by requiring additional energy to evaporate the water. Pre-treatment to reduce moisture is essential for optimal performance.
-
Product Yields and Conditions:
- Biochar: Produced at low temperatures (300°C–400°C) and low heating rates. Biochar is a stable carbon-rich solid used in soil amendment and carbon sequestration.
- Bio-oil: Produced at moderate temperatures (400°C–600°C) with high heating rates and short residence times. Bio-oil is a liquid fuel that can be used for heating or further refined into transportation fuels.
- Syngas: Produced at high temperatures (>600°C) with low heating rates and long residence times. Syngas is a mixture of hydrogen, carbon monoxide, and methane, which can be used as a fuel or chemical feedstock.
-
Operational Efficiency and Control:
- Furnace Temperature: Maintaining the correct temperature is crucial for achieving the desired product distribution. Temperature control ensures that the biomass decomposes efficiently without over-degradation.
- Residence Time: Proper control of residence time ensures that the biomass undergoes complete pyrolysis without excessive gasification or charring.
- Pressure: The pressure inside the pyrolysis furnace affects the reaction kinetics and product yields. Optimal pressure conditions must be maintained to ensure efficient pyrolysis.
-
Importance of Pre-treatment and De-dusting:
- Pre-treatment: Reducing the moisture content and particle size of the biomass improves the efficiency of the pyrolysis process. Dry biomass requires less energy to heat and decomposes more uniformly.
- De-dusting: Cleaning the exhaust gases is essential for environmental compliance and operational safety. Removing particulate matter and harmful substances ensures that the pyrolysis process is environmentally sustainable.
-
Applications of Pyrolysis Products:
- Biochar: Used in agriculture to improve soil fertility and water retention. It also serves as a carbon sink, helping to mitigate climate change.
- Bio-oil: Can be used directly as a fuel or upgraded to produce transportation fuels and chemicals.
- Syngas: Used as a fuel for power generation or as a feedstock for producing synthetic fuels and chemicals.
In conclusion, biomass pyrolysis is a versatile and efficient process for converting organic materials into valuable products. The process is highly dependent on operational parameters such as temperature, heating rate, residence time, and moisture content. Proper control of these factors, along with effective pre-treatment and de-dusting, ensures optimal performance and the production of high-quality biochar, bio-oil, and syngas. These products have diverse applications, making biomass pyrolysis a key technology in sustainable energy and environmental management.
Summary Table:
Key Aspect | Details |
---|---|
Process | Thermal decomposition of biomass in the absence of oxygen. |
Main Products | Biochar (solid), bio-oil (liquid), and syngas (gas). |
Key Factors | Temperature, heating rate, residence time, and moisture content. |
Temperature Ranges | - Biochar: 300°C–400°C - Bio-oil: 400°C–600°C - Syngas: >600°C |
Applications | - Biochar: Soil amendment, carbon sequestration. - Bio-oil: Fuel, chemicals. - Syngas: Power generation, chemical feedstock. |
Discover how biomass pyrolysis can transform your sustainable energy strategy—contact us today for expert guidance!