The rate of electron beam (e-beam) evaporation typically ranges from 0.1 to 100 nanometers (nm) per minute, depending on the material being evaporated, the power of the electron beam, and the specific setup of the system. This method is highly efficient for depositing thin, high-purity coatings, especially for materials with high melting points, such as refractory metals and oxides. E-beam evaporation operates in a high vacuum environment (pressure less than 10^-5 Torr) to minimize collisions between source atoms and background gases, ensuring a clean and uniform deposition process. The deposition rate is influenced by factors such as the vapor pressure of the material (approximately 10 mTorr for reasonable rates) and the thermal energy generated by the electron beam.
Key Points Explained:
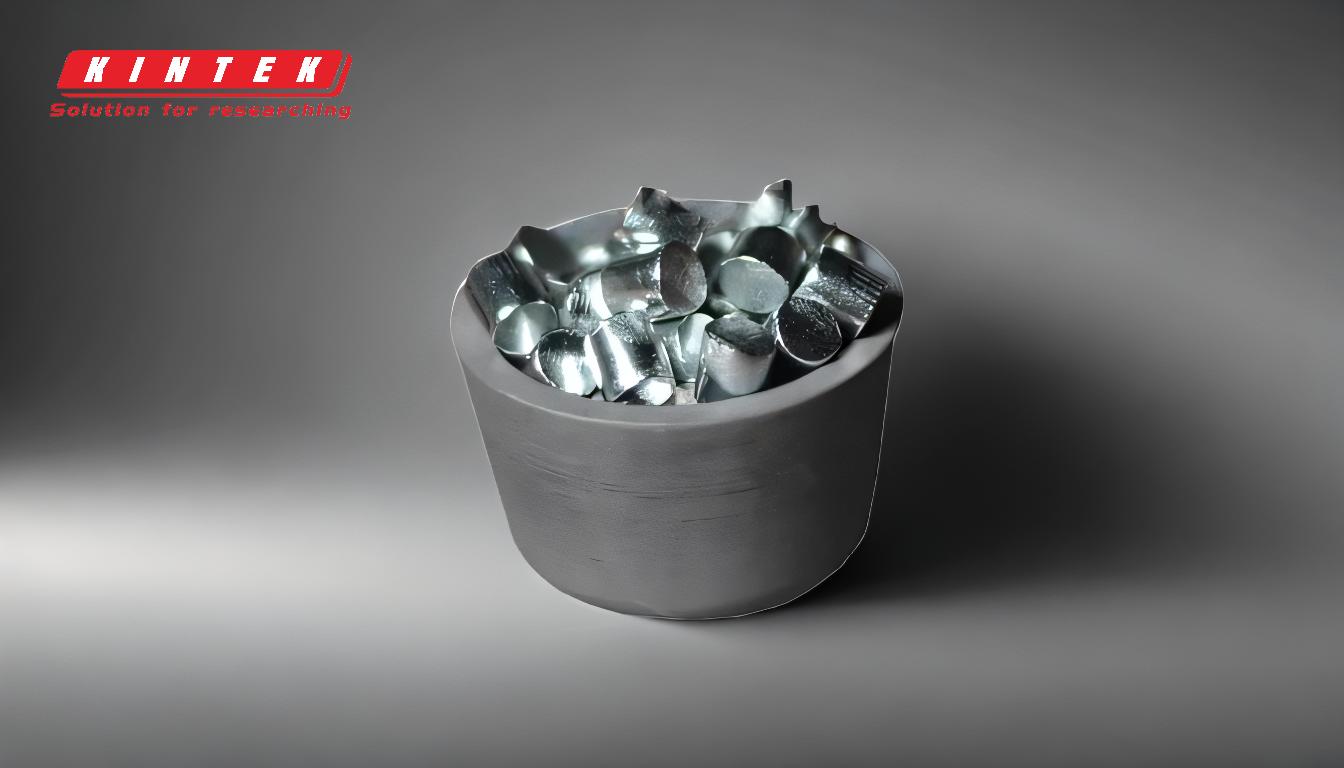
-
Deposition Rate Range:
- The deposition rate for e-beam evaporation typically falls between 0.1 to 100 nanometers (nm) per minute. This range is suitable for applications requiring precise, thin-film coatings.
- The rate depends on the material's properties, the power of the electron beam, and the system's configuration.
-
High Vacuum Environment:
- E-beam evaporation operates in a high vacuum chamber with pressures below 10^-5 Torr. This minimizes collisions between source atoms and background gases, ensuring a clean and efficient deposition process.
- The vacuum environment also helps maintain the purity of the deposited material, reducing the risk of contamination.
-
Vapor Pressure Requirement:
- For reasonable deposition rates, the vapor pressure of the material must be approximately 10 mTorr. This ensures that the material evaporates effectively and deposits uniformly on the substrate.
-
Material Versatility:
- E-beam evaporation is particularly effective for materials with high melting points, such as refractory metals and oxides, which are difficult to evaporate using other methods like thermal evaporation.
- The ability to handle a wide range of materials makes e-beam evaporation suitable for complex applications requiring multiple layers of different materials.
-
Electron Beam Mechanism:
- The process involves directing a high-energy electron beam (5–10 kV) at the target material in a water-cooled crucible. The kinetic energy of the electrons is converted into thermal energy upon impact, heating and evaporating the material.
- The evaporated material disperses in its gaseous phase within the vacuum chamber and deposits onto the substrate.
-
Advantages Over Thermal Evaporation:
- Compared to thermal evaporation, e-beam evaporation offers:
- Higher deposition rates.
- Denser coatings with fewer impurities.
- The ability to handle materials with higher melting temperatures.
- Compared to thermal evaporation, e-beam evaporation offers:
-
Uniformity Challenges:
- E-beam evaporation is an isotropic process, meaning the material evaporates uniformly in all directions. This can lead to non-uniform deposition on flat substrates.
- To address this, spherical wafer holders are often used to improve deposition uniformity.
-
Applications:
- E-beam evaporation is widely used in industries requiring high-purity, thin-film coatings, such as:
- Semiconductor manufacturing.
- Optical coatings.
- Research and development of advanced materials.
- E-beam evaporation is widely used in industries requiring high-purity, thin-film coatings, such as:
By understanding these key points, equipment and consumable purchasers can better evaluate the suitability of e-beam evaporation for their specific applications and ensure optimal system configuration for desired deposition rates and coating quality.
Summary Table:
Key Aspect | Details |
---|---|
Deposition Rate Range | 0.1–100 nanometers (nm) per minute |
Vacuum Environment | Pressure below 10^-5 Torr for clean, uniform deposition |
Vapor Pressure | ~10 mTorr for effective evaporation |
Material Versatility | Ideal for refractory metals, oxides, and high-melting-point materials |
Electron Beam Mechanism | 5–10 kV electron beam heats and evaporates target material |
Applications | Semiconductor manufacturing, optical coatings, R&D of advanced materials |
Optimize your thin-film deposition process with e-beam evaporation—contact our experts today to learn more!