The heat treatment process is a critical method used to alter the physical and sometimes chemical properties of materials, primarily metals and alloys, to achieve desired characteristics such as hardness, strength, or ductility. The sequence of heat treatment typically involves three fundamental stages: heating, soaking, and cooling. Each stage plays a crucial role in transforming the material's microstructure to achieve the desired mechanical properties. Heating raises the material to a specific temperature, soaking maintains that temperature to allow uniform structural changes, and cooling solidifies the new structure. The process can vary in temperature, duration, and cooling methods depending on the material and the intended outcome.
Key Points Explained:
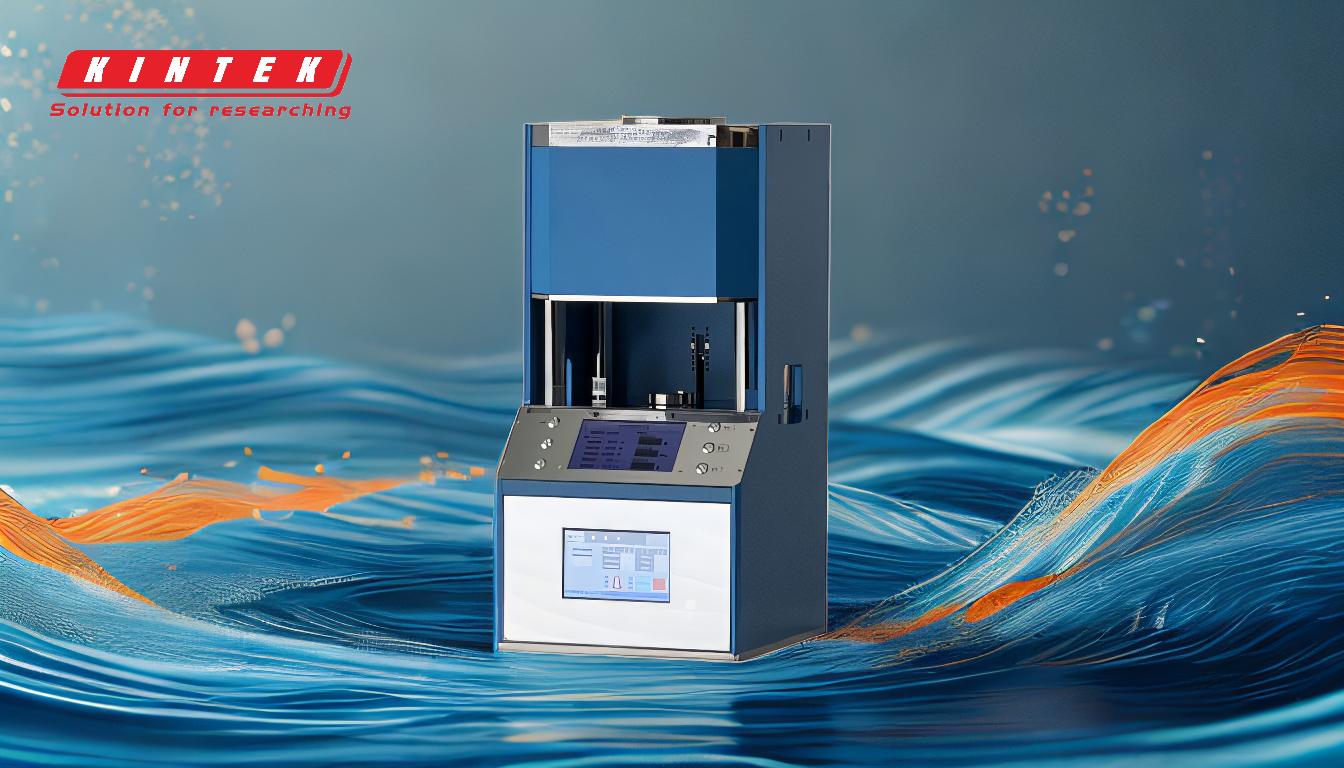
-
Heating:
- Purpose: The first stage involves heating the material to a specific temperature, which can range up to 2,400°F depending on the material and desired outcome.
- Process: The material is gradually heated to avoid thermal shock, which could cause cracking or deformation.
- Importance: Heating ensures that the material reaches a temperature where its internal structure can be altered. This is crucial for processes like annealing, hardening, or stress relief.
-
Soaking:
- Purpose: Soaking involves maintaining the material at the specified temperature for a set period, allowing the internal structure to uniformly change.
- Process: The soaking time can vary from a few seconds to several hours, depending on the material's thickness and the desired transformation.
- Importance: Soaking ensures that the entire material reaches the same temperature, leading to consistent structural changes. This stage is critical for achieving uniform hardness or softening across the material.
-
Cooling:
- Purpose: The final stage involves cooling the material to solidify its new structure. The cooling method can significantly affect the material's final properties.
- Process: Cooling can be done through various methods, such as quenching (rapid cooling in water, oil, or air), air cooling, or controlled cooling in a furnace.
- Importance: The cooling rate determines the material's final properties. Rapid cooling (quenching) typically increases hardness, while slower cooling (annealing) can improve ductility and reduce internal stresses.
-
Variations in Heat Treatment Processes:
- Annealing: Softens the material to improve machinability or ductility.
- Hardening: Increases the material's hardness and strength through rapid cooling.
- Case Hardening: Hardens only the surface layer while keeping the core soft and ductile.
- Stress Relief: Reduces internal stresses caused by machining, forming, or welding.
- Austempering and Marquenching: Specialized processes to add resilience or improve toughness.
-
Applications:
- Aerospace: Heat treatment is used to enhance the strength and durability of aerospace components.
- Automotive: Critical for hardening gears, shafts, and other high-stress parts.
- Manufacturing: Used to improve the performance of tools, dies, and molds.
By following the sequence of heating, soaking, and cooling, heat treatment processes can significantly enhance the mechanical properties of materials, making them suitable for a wide range of industrial applications. The specific parameters of each stage must be carefully controlled to achieve the desired outcomes.
Summary Table:
Stage | Purpose | Process | Importance |
---|---|---|---|
Heating | Raise material to a specific temperature (up to 2,400°F). | Gradually heat to avoid thermal shock. | Alters internal structure for processes like annealing, hardening, or stress relief. |
Soaking | Maintain temperature for uniform structural changes. | Duration varies (seconds to hours) based on material thickness and transformation needs. | Ensures consistent structural changes for uniform hardness or softening. |
Cooling | Solidify new structure. | Methods include quenching (rapid cooling), air cooling, or controlled furnace cooling. | Cooling rate determines final properties—quenching increases hardness, annealing improves ductility. |
Optimize your material properties with expert heat treatment solutions—contact us today!