The sintering temperature of zirconia is a critical factor in achieving the desired hardness, strength, and density of the material. Typically, zirconia is sintered at high temperatures ranging from 1400°C to 1600°C, with optimal results often achieved between 1500°C and 1550°C. This temperature range ensures the transformation of zirconia from a monoclinic to a polytetragonal crystalline state, which is essential for maximizing its mechanical properties. Additionally, the sintering process involves careful control of the ramp rate, hold time, and cooling rate, particularly between 900°C and the peak temperature, to avoid defects and ensure uniformity.
Key Points Explained:
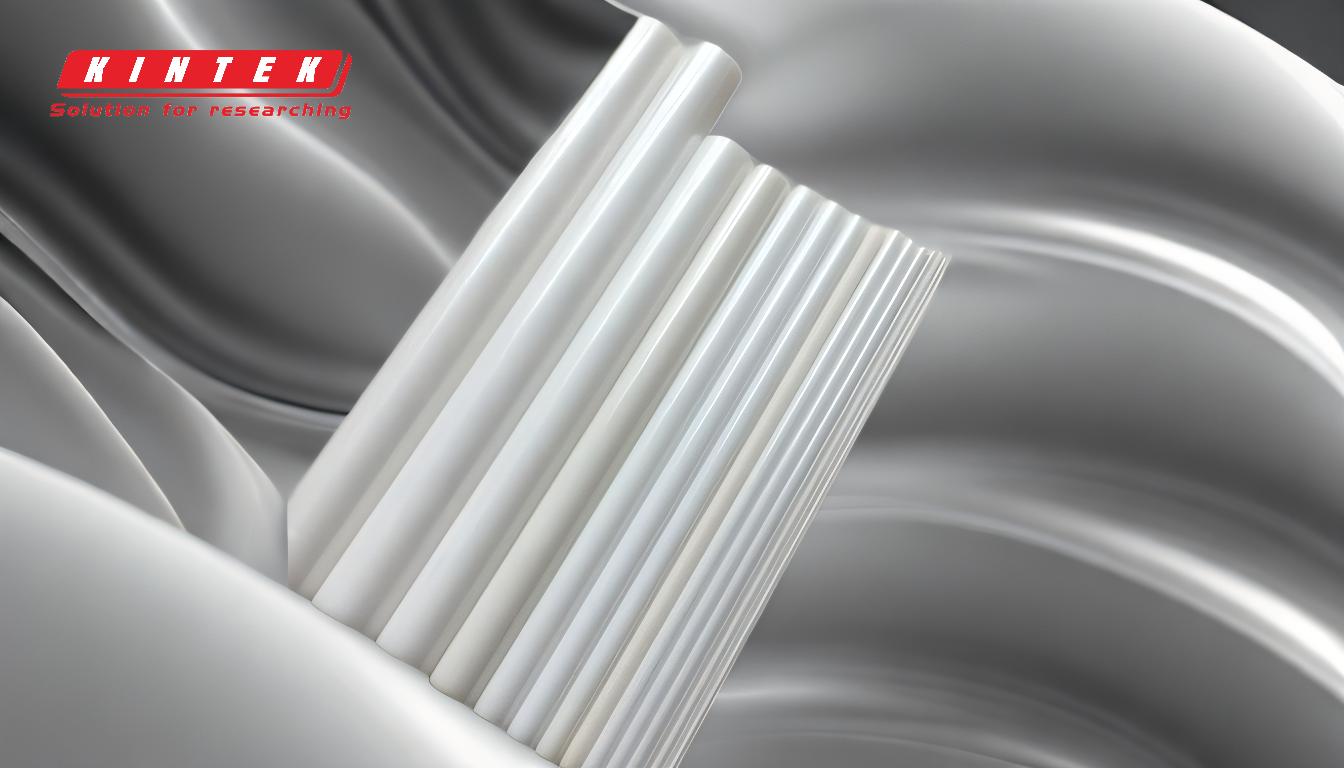
-
Temperature Range for Sintering Zirconia:
- Zirconia is typically sintered at temperatures between 1400°C and 1600°C. This range is necessary to achieve the desired hardness, strength, and density.
- Recent studies suggest that firing at 1500°C to 1550°C produces maximum strength in zirconia, making this range ideal for dental and industrial applications.
-
Crystalline Transformation:
- Zirconia undergoes a phase transformation from a monoclinic to a polytetragonal crystalline state at around 1100°C to 1200°C. However, sintering at higher temperatures (closer to 1500°C) is required to achieve maximum density, often reaching 99% of the theoretical maximum density.
-
Importance of Ramp Rate and Cooling:
- The sintering process is highly sensitive to temperature changes. From room temperature to 900°C, there is little effect on the material. However, the ramp rate from 900°C to the peak temperature, the consistency of temperature during the hold time, and the cooling rate back to 900°C are critical for achieving optimal results.
- Improper control of these parameters can lead to defects such as cracking or uneven density.
-
Dental Applications:
- In dental applications, zirconia is sintered at 1400°C to 1600°C to achieve the required hardness and strength for dental restorations. The precise temperature and process control ensure the material's biocompatibility and durability.
-
Industrial Relevance:
- The high sintering temperatures and precise control required for zirconia make specialized equipment like sintering furnaces essential. These furnaces are designed to maintain consistent temperatures and controlled cooling rates, ensuring the material's mechanical properties are optimized.
By understanding these key points, purchasers of equipment and consumables can make informed decisions about the sintering process for zirconia, ensuring they achieve the desired material properties for their specific applications.
Summary Table:
Key Aspect | Details |
---|---|
Temperature Range | 1400°C to 1600°C (optimal: 1500°C–1550°C) |
Crystalline Transformation | Monoclinic to polytetragonal at 1100°C–1200°C; higher temps for max density |
Critical Parameters | Ramp rate, hold time, and cooling rate (900°C to peak temp) |
Dental Applications | 1400°C–1600°C for biocompatible, durable dental restorations |
Industrial Relevance | Requires specialized sintering furnaces for precise temperature control |
Achieve optimal zirconia sintering results—contact our experts today for tailored solutions!