The sintering temperature of zirconia ceramic typically ranges between 1400°C and 1600°C, with the optimal range being around 1500°C to 1550°C. This temperature range ensures the material achieves the desired hardness, density, and strength. Higher temperatures can lead to excessive grain growth, reducing strength, while lower temperatures may not fully densify the material. The transformation from monoclinic to polytetragonal structure occurs at around 1100°C to 1200°C, but full sintering requires higher temperatures to achieve near-theoretical maximum density. Dental zirconia, in particular, is often sintered at approximately 1550°C to attain ideal physical, mechanical, and esthetic properties.
Key Points Explained:
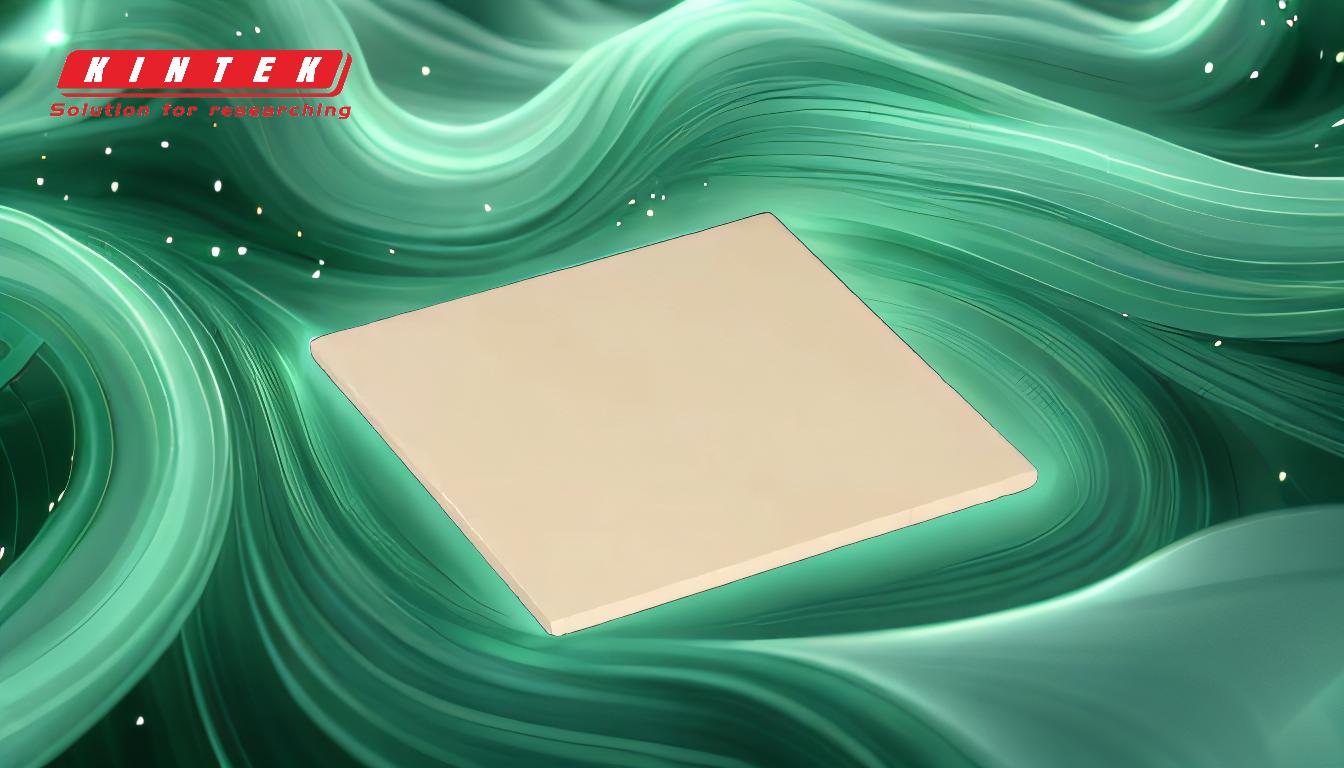
-
Sintering Temperature Range:
- Zirconia ceramics are sintered at high temperatures between 1400°C and 1600°C.
- This range is necessary to achieve the desired hardness, density, and strength in the final product.
-
Optimal Sintering Temperature:
- The optimal sintering temperature for most zirconia materials is 1500°C to 1550°C.
- At this temperature range, zirconia achieves near-theoretical maximum density (close to 99%) and optimal mechanical properties.
-
Transformation Temperature:
- The transformation from the monoclinic to the polytetragonal structure occurs at 1100°C to 1200°C.
- However, this transformation alone is insufficient for full densification, which requires higher sintering temperatures.
-
Effect of Temperature on Strength:
- Firing zirconia at 1500°C to 1550°C produces maximum strength (approximately 1280 MPa).
- Deviating from this range by ±150°C can significantly reduce strength:
- At 1600°C, strength drops to about 980 MPa.
- At 1700°C, strength further decreases to about 600 MPa.
-
Grain Growth and Density:
- Higher sintering temperatures (above 1550°C) can lead to excessive grain growth, which negatively impacts strength.
- Lower temperatures (below 1500°C) may result in incomplete densification, compromising the material's mechanical properties.
-
Dental Zirconia Sintering:
- Dental zirconia is typically sintered at 1550°C to achieve the ideal balance of physical, mechanical, and esthetic properties.
- Dental sintering furnaces are designed to operate within the 1400°C to 1600°C range to ensure optimal results.
-
Heat Rise Rate:
- The recommended heat rise rate during sintering is 4°C to 10°C per minute.
- A controlled heating rate is critical to avoid thermal stress and ensure uniform densification.
-
Manufacturer Recommendations:
- Some manufacturers may recommend slightly lower or higher sintering temperatures depending on the specific zirconia material and its intended application.
- It is essential to follow the manufacturer's guidelines to achieve the desired properties.
-
Importance of Temperature Accuracy:
- The accuracy of the sintering furnace is crucial, as even small deviations from the optimal temperature range can significantly affect the material's performance.
- Furnaces should be calibrated and maintained to ensure consistent and precise temperature control.
By understanding these key points, purchasers and users of zirconia ceramics can make informed decisions about sintering parameters to achieve the desired material properties for their specific applications.
Summary Table:
Key Parameter | Details |
---|---|
Sintering Temperature Range | 1400°C to 1600°C |
Optimal Temperature | 1500°C to 1550°C (near-theoretical maximum density and strength) |
Transformation Temperature | 1100°C to 1200°C (monoclinic to polytetragonal) |
Maximum Strength | ~1280 MPa at 1500°C–1550°C |
Grain Growth Risk | Above 1550°C (excessive grain growth reduces strength) |
Dental Zirconia Sintering | ~1550°C for ideal physical, mechanical, and esthetic properties |
Heat Rise Rate | 4°C to 10°C per minute (critical for uniform densification) |
Need help achieving the perfect sintering temperature for your zirconia ceramics? Contact our experts today for tailored solutions!