The sputtering cathode method is a physical vapor deposition (PVD) technique used to deposit thin films onto substrates. It involves bombarding a solid target (cathode) with high-energy ions in a vacuum environment, causing atoms from the target to be ejected and deposited onto a substrate. This method is widely used in industries for coating materials due to its ability to produce high-quality, uniform films. The process typically involves a DC field, an inert gas like argon, and a plasma environment to generate ions that sputter the target material. Below, the key aspects of the sputtering cathode method are explained in detail.
Key Points Explained:
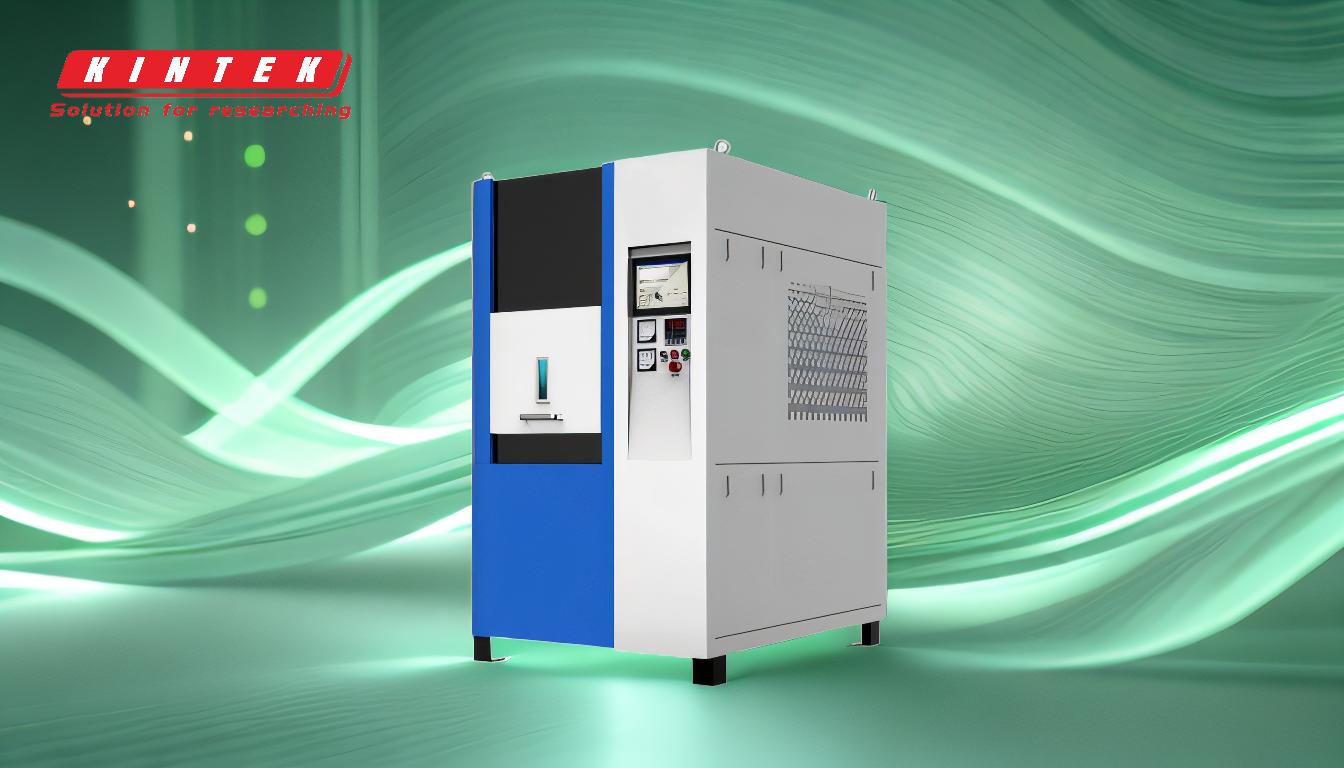
-
Basic Principle of Sputtering Cathode Method:
- The sputtering cathode method relies on the bombardment of a solid target (cathode) with high-energy ions in a vacuum chamber.
- A DC field is applied, with the target at a negative potential (several hundred volts) and the substrate acting as the positive electrode.
- An inert gas, typically argon, is introduced and ionized to create a plasma. Ar+ ions are accelerated toward the target, dislodging atoms from its surface.
- These ejected atoms travel toward the substrate, forming a thin film.
-
Components of the Sputtering System:
- Target (Cathode): The material to be deposited, typically made of metals or alloys.
- Substrate: The surface onto which the thin film is deposited. It can be heat-sensitive materials like plastics due to the low temperature of the sputtered particles.
- Vacuum Chamber: Ensures a controlled environment free from air or unwanted gases, preventing contamination and enabling precise deposition.
- Inert Gas (Argon): Ionized to create a plasma, which generates the high-energy ions needed for sputtering.
- DC Power Supply: Provides the necessary voltage to create the electric field and accelerate ions toward the target.
-
Advantages of the Sputtering Cathode Method:
- Uniformity: Produces highly uniform thin films, making it suitable for applications requiring precise thickness control.
- Material Versatility: Works well for metallic targets and can be adapted for non-conductive materials with modifications.
- Low-Temperature Process: Suitable for heat-sensitive substrates like plastics.
- High-Quality Films: Results in dense, adherent films with excellent mechanical and optical properties.
-
Limitations of the Sputtering Cathode Method:
- Inefficiency with Non-Conductive Materials: Non-conductive targets can become positively charged, preventing ions from reaching the surface and reducing sputtering efficiency.
- Deposition Rate: Generally slower compared to other PVD methods like evaporation.
- Cost and Complexity: Requires a vacuum environment and specialized equipment, increasing operational costs.
-
Applications of the Sputtering Cathode Method:
- Semiconductor Industry: Used for depositing thin films in integrated circuits and microelectronics.
- Optical Coatings: Produces anti-reflective and reflective coatings for lenses, mirrors, and displays.
- Decorative Coatings: Applies durable and aesthetically pleasing coatings on consumer products.
- Magnetic Storage: Deposits thin films for hard drives and other data storage devices.
-
Comparison with Other Sputtering Methods:
- DC Magnetron Sputtering: Utilizes a magnetic field to enhance ionization and increase deposition rates. Suitable for conductive and some non-conductive materials.
- Ion Beam Sputtering: Uses a focused ion beam for precise control over film properties, often used in high-precision applications.
- Reactive Sputtering: Involves chemical reactions during deposition, enabling the formation of compound films like oxides or nitrides.
- HiPIMS (High-Power Impulse Magnetron Sputtering): Operates at very high power densities in short pulses, producing dense, high-quality films.
-
Process Optimization Considerations:
- Gas Pressure and Flow Rate: Affects ionization efficiency and film quality.
- Target Material and Purity: Determines the composition and properties of the deposited film.
- Substrate Preparation: Surface cleanliness and orientation influence film adhesion and uniformity.
- Power Supply Parameters: Voltage and current settings impact sputtering rate and film characteristics.
In summary, the sputtering cathode method is a versatile and widely used technique for depositing thin films with high precision and quality. While it has some limitations, its advantages make it a preferred choice in industries ranging from semiconductors to optics and beyond. Understanding the process components, advantages, and applications is essential for optimizing its use in various technological applications.
Summary Table:
Aspect | Details |
---|---|
Basic Principle | Bombardment of a solid target with high-energy ions in a vacuum environment. |
Key Components | Target (cathode), substrate, vacuum chamber, inert gas (argon), DC power supply. |
Advantages | Uniform films, material versatility, low-temperature process, high-quality results. |
Limitations | Inefficiency with non-conductive materials, slower deposition rate, higher costs. |
Applications | Semiconductors, optical coatings, decorative coatings, magnetic storage. |
Comparison with Methods | DC Magnetron, Ion Beam, Reactive Sputtering, HiPIMS. |
Optimization Factors | Gas pressure, target material, substrate preparation, power supply settings. |
Discover how the sputtering cathode method can enhance your thin film processes—contact our experts today!