Sputtering is a physical vapor deposition (PVD) technique used to deposit thin films onto substrates. It involves creating a plasma of inert gas (typically argon) in a vacuum chamber, where gas ions are accelerated toward a target material. These ions collide with the target, ejecting atoms or molecules that then deposit onto the substrate, forming a thin film. Sputtering is widely used due to its ability to produce uniform, high-quality films with strong adhesion. The process is versatile, applicable to a wide range of materials, and can be enhanced with techniques like magnetron sputtering for better control and efficiency.
Key Points Explained:
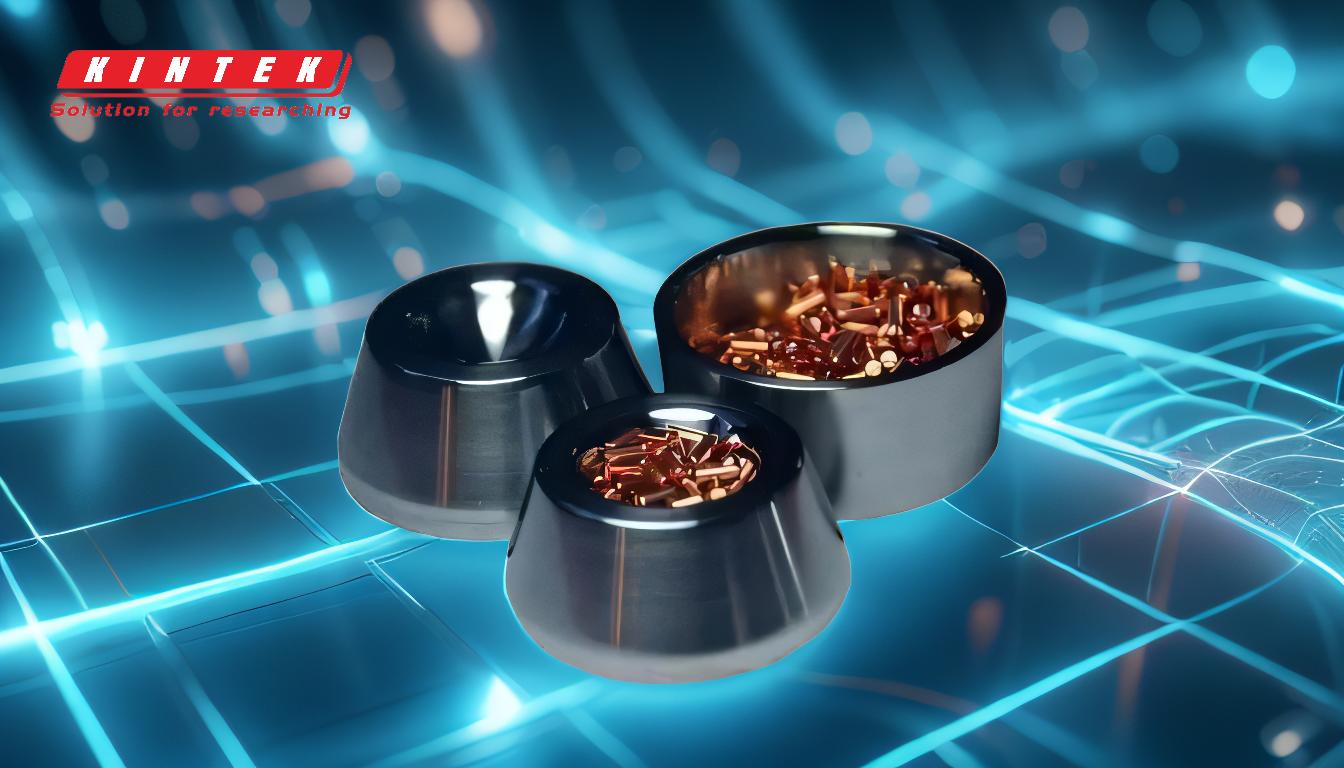
-
Definition of Sputtering:
- Sputtering is a physical vapor deposition (PVD) method where atoms are ejected from a solid target material due to bombardment by energetic ions, typically from an inert gas like argon.
- The ejected atoms then deposit onto a substrate, forming a thin film.
-
Process Overview:
- A vacuum chamber is used to create a low-pressure environment.
- An inert gas (e.g., argon) is introduced into the chamber.
- A high voltage is applied between the target (cathode) and the substrate (anode), generating a plasma.
- Gas ions in the plasma are accelerated toward the target, causing atoms to be ejected through momentum transfer.
- The ejected atoms travel through the chamber and deposit onto the substrate, forming a thin film.
-
Key Components:
- Vacuum Chamber: Ensures a controlled environment free from contaminants.
- Inert Gas: Typically argon, used to create the plasma.
- Target Material: The source of the atoms that will form the thin film.
- Substrate: The surface onto which the thin film is deposited.
- Power Supply: Provides the high voltage needed to generate the plasma.
-
Advantages of Sputtering:
- Uniformity: Produces highly uniform films, even on complex geometries.
- Adhesion: Films have excellent adhesion to the substrate.
- Versatility: Can deposit a wide range of materials, including metals, alloys, and ceramics.
- Control: Parameters like pressure, voltage, and gas flow can be precisely controlled to tailor film properties.
-
Types of Sputtering:
- DC Sputtering: Uses direct current to generate the plasma, suitable for conductive materials.
- RF Sputtering: Uses radio frequency for non-conductive materials.
- Magnetron Sputtering: Enhances efficiency by using magnetic fields to confine the plasma near the target.
- Reactive Sputtering: Introduces reactive gases (e.g., oxygen or nitrogen) to form compound films like oxides or nitrides.
-
Applications:
- Semiconductors: Used in the fabrication of integrated circuits and solar cells.
- Optics: Deposits anti-reflective and reflective coatings on lenses and mirrors.
- Decorative Coatings: Applied to consumer products for aesthetic and protective purposes.
- Hard Coatings: Used in tools and machinery to enhance durability and wear resistance.
-
Comparison with Other Thin-Film Deposition Methods:
- Chemical Vapor Deposition (CVD): Involves chemical reactions to form films, often at higher temperatures. Sputtering, being a physical process, avoids chemical reactions and can deposit films at lower temperatures.
- Thermal Evaporation: Involves heating the target material until it evaporates. Sputtering provides better control over film composition and uniformity.
- Pulsed Laser Deposition (PLD): Uses a laser to ablate the target material. Sputtering is more scalable and suitable for industrial applications.
-
Challenges and Considerations:
- Target Utilization: Sputtering can lead to uneven erosion of the target, requiring careful design to maximize usage.
- Film Stress: The process can introduce stress in the film, affecting its mechanical properties.
- Cost: Sputtering systems can be expensive due to the need for high vacuum and precise control systems.
By understanding these key points, one can appreciate the complexity and versatility of the sputtering method, making it a cornerstone in modern thin-film deposition technologies.
Summary Table:
Aspect | Details |
---|---|
Definition | Physical vapor deposition (PVD) method using energetic ions to eject atoms. |
Key Components | Vacuum chamber, inert gas (argon), target material, substrate, power supply. |
Advantages | Uniform films, strong adhesion, versatile, precise control. |
Types of Sputtering | DC, RF, magnetron, reactive sputtering. |
Applications | Semiconductors, optics, decorative coatings, hard coatings. |
Challenges | Target utilization, film stress, high cost. |
Discover how sputtering can enhance your thin-film processes—contact our experts today!