The sputtering process is a widely used method for depositing thin films onto substrates, commonly employed in industries like semiconductor manufacturing, precision optics, and surface finishing. It involves creating a plasma by ionizing an inert gas, typically argon, within a vacuum chamber. Positively charged ions from the plasma are accelerated towards a negatively charged target material, causing atoms or molecules to be ejected from the target's surface. These ejected particles then travel through the chamber and deposit onto a substrate, forming a thin, uniform, and adherent film. The process requires precise control of vacuum conditions, gas pressure, and energy transfer to ensure high-quality coatings.
Key Points Explained:
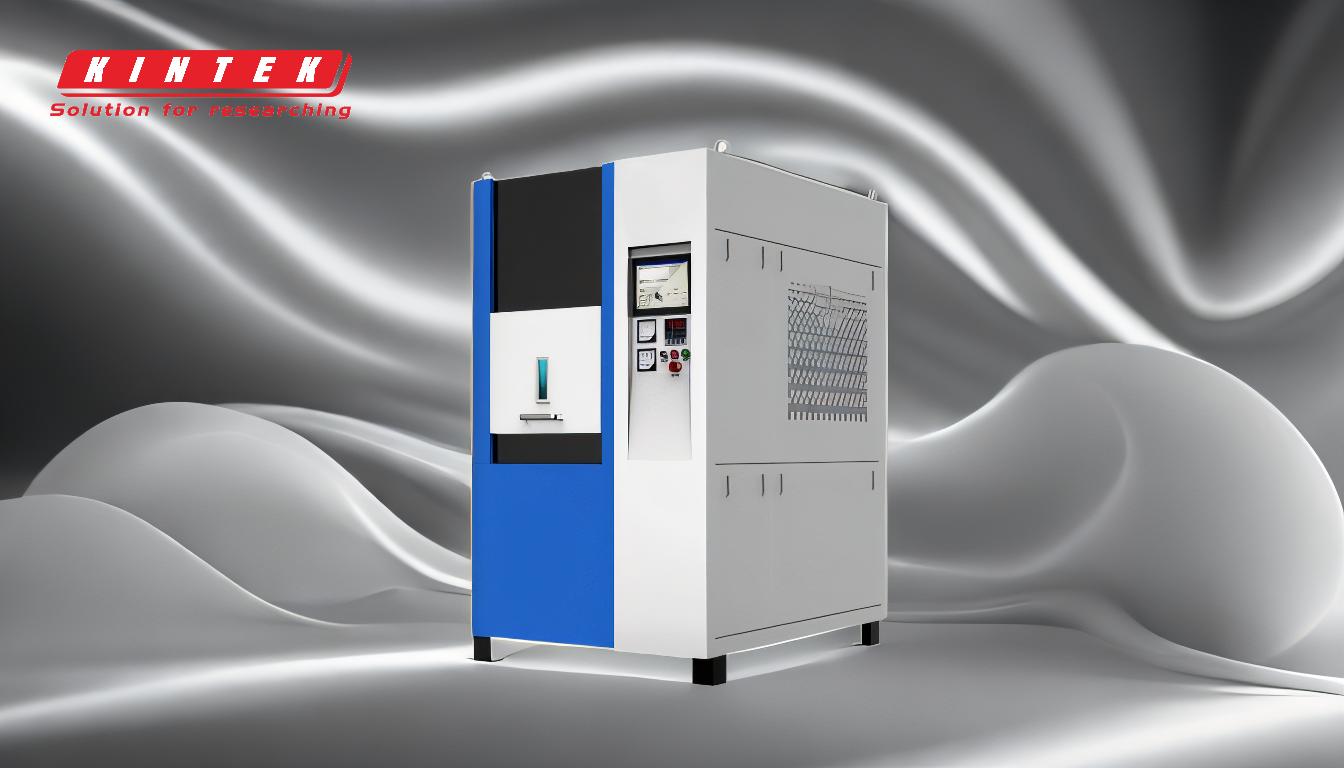
-
Inert Gas Ionization:
- The sputtering process begins with the introduction of an inert gas, such as argon, into a vacuum chamber. The gas is ionized using a high voltage or electromagnetic excitation, creating a plasma composed of positively charged ions (e.g., Ar+).
- The choice of gas depends on the target material. For light elements, neon is preferred, while heavier elements like krypton or xenon are used for heavier targets to ensure efficient momentum transfer.
-
Vacuum Environment:
- The process is performed under vacuum conditions to eliminate contaminants and ensure a clean deposition environment. The chamber pressure is typically reduced to around 1 Pa (0.0000145 psi) before introducing the sputtering gas.
- Lower pressures are maintained initially to remove moisture and impurities, followed by higher pressures (10^-1 to 10^-3 mbar) for the actual sputtering process.
-
Energy Transfer and Ejection of Target Atoms:
- Positively charged ions from the plasma are accelerated towards the negatively charged target material (cathode) due to an applied high voltage (3-5 kV).
- Upon collision, the ions transfer their kinetic energy to the target atoms, causing them to be ejected from the surface. These ejected particles are neutral atoms, clusters, or molecules.
-
Deposition of Thin Film:
- The ejected target atoms travel in straight lines through the vacuum chamber and deposit onto the substrate, forming a thin film.
- The resulting film is characterized by excellent uniformity, density, and adhesion, making it suitable for various applications.
-
Magnetic Field Confinement:
- A magnetic field is often used to confine the plasma around the target, increasing the efficiency of ion bombardment and ensuring a more controlled deposition process.
- This magnetic field is created by placing an electromagnet near the target, which also helps in maintaining a stable plasma.
-
Temperature Control:
- The chamber may be heated to temperatures ranging from 150°C to 750°C (302°F to 1382°F), depending on the material being deposited. This heating step enhances the quality and adhesion of the thin film.
-
Applications of Sputtering:
- Sputtering is widely used in industries such as semiconductor processing, precision optics, and surface finishing due to its ability to produce high-quality thin films with precise control over thickness and composition.
By following these steps, the sputtering process achieves a highly controlled and efficient method for depositing thin films, making it indispensable in modern manufacturing and material science.
Summary Table:
Key Aspect | Details |
---|---|
Inert Gas Ionization | Argon or other inert gases ionized to create plasma for sputtering. |
Vacuum Environment | Chamber pressure reduced to ~1 Pa for clean, contaminant-free deposition. |
Energy Transfer | Ions accelerated at 3-5 kV to eject target atoms for thin film formation. |
Magnetic Field Confinement | Enhances plasma control and ion bombardment efficiency. |
Temperature Control | Chamber heated between 150°C to 750°C for improved film quality and adhesion. |
Applications | Used in semiconductors, precision optics, and surface finishing industries. |
Discover how sputtering can elevate your manufacturing process—contact our experts today!