The sputtering voltage of a magnetron is a critical parameter in the magnetron sputtering process, which directly influences the efficiency and quality of the deposition. It is determined by factors such as the target material, the type of gas used, the magnetic field configuration, and the operating pressure. Typically, the sputtering voltage ranges from a few hundred volts to several thousand volts, depending on the specific application and system setup. Understanding the relationship between the sputtering voltage and the plasma characteristics, target erosion, and deposition efficiency is essential for optimizing the process and achieving high-quality coatings.
Key Points Explained:
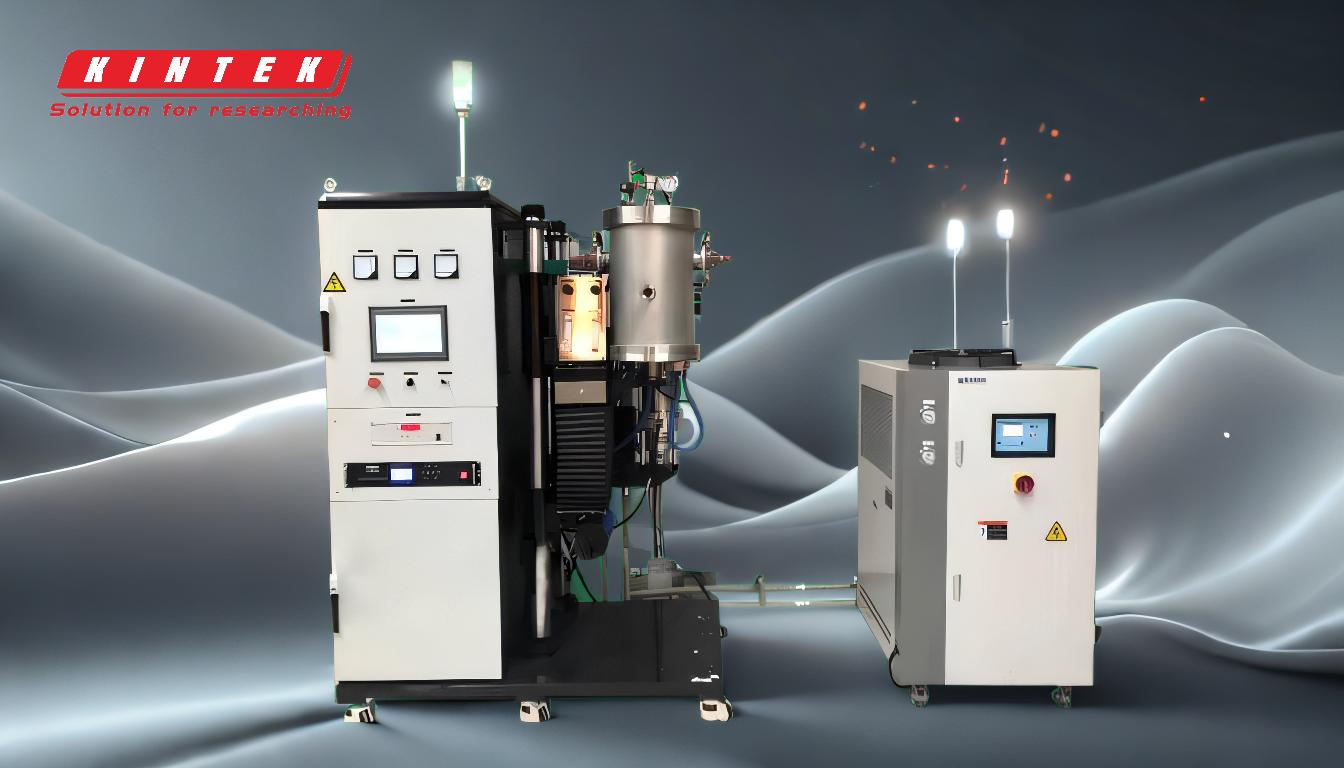
-
Definition of Sputtering Voltage:
- Sputtering voltage refers to the voltage applied between the cathode (target) and the anode in a magnetron sputtering system. This voltage ionizes the inert gas (usually argon) to create a plasma, which then bombards the target material, causing atoms to be ejected and deposited onto the substrate.
-
Factors Influencing Sputtering Voltage:
- Target Material: Different materials have varying sputtering yields, which affect the required voltage. For example, metals with higher sputtering yields may require lower voltages.
- Gas Type and Pressure: The type of gas (e.g., argon, neon, xenon) and its pressure in the chamber influence the ionization efficiency and, consequently, the sputtering voltage. Lower pressures generally require higher voltages to sustain the plasma.
- Magnetic Field Configuration: The magnetic field traps electrons, enhancing ionization efficiency and allowing the plasma to be sustained at lower voltages. The strength and configuration of the magnetic field are critical in determining the sputtering voltage.
-
Typical Voltage Range:
- The sputtering voltage in magnetron systems typically ranges from 300 to 1000 volts. However, this can vary depending on the specific application, target material, and system design. For example, reactive sputtering processes involving gases like oxygen or nitrogen may require different voltage settings.
-
Impact on Deposition Process:
- Plasma Characteristics: The sputtering voltage directly affects the plasma density and energy, which in turn influence the deposition rate and film quality. Higher voltages can lead to higher deposition rates but may also increase the risk of defects in the coating.
- Target Erosion: The voltage affects the rate and uniformity of target erosion. Optimal voltage settings help achieve uniform erosion, reducing particle shedding and improving coating quality.
- Energy of Sputtered Atoms: The voltage influences the energy of the sputtered atoms, which affects the adhesion and microstructure of the deposited film. Higher energy atoms can lead to better adhesion and denser films.
-
System Components and Their Role:
- Vacuum Chamber: Maintains the low-pressure environment necessary for plasma generation.
- Target Material: The material to be deposited, mounted on the cathode.
- Substrate Holder: Holds the substrate where the coating is deposited.
- Magnetron: Generates the magnetic field that traps electrons and enhances ionization.
- Power Supply: Provides the necessary voltage to sustain the plasma and sputtering process.
-
Optimization of Sputtering Voltage:
- Process Control: Adjusting the sputtering voltage is a key aspect of process optimization. It involves balancing the deposition rate, film quality, and target erosion.
- Monitoring and Feedback: Real-time monitoring of the plasma characteristics and deposition rate can help fine-tune the voltage for optimal performance.
Understanding and controlling the sputtering voltage is essential for achieving high-quality coatings in magnetron sputtering. By considering the factors that influence the voltage and its impact on the deposition process, operators can optimize the system for specific applications, ensuring efficient and effective material deposition.
Summary Table:
Aspect | Details |
---|---|
Definition | Voltage applied between cathode and anode to ionize gas and create plasma. |
Typical Range | 300 to 1000 volts, depending on application and system setup. |
Key Influencing Factors | Target material, gas type, pressure, and magnetic field configuration. |
Impact on Deposition | Affects plasma characteristics, target erosion, and film quality. |
Optimization | Adjust voltage to balance deposition rate, film quality, and target erosion. |
Need help optimizing your magnetron sputtering process? Contact our experts today for tailored solutions!