The substrate in thin film deposition refers to the object or material that is coated with a thin layer of film. It serves as the base upon which the deposition process occurs. Substrates can vary widely depending on the application, including semiconductor wafers, solar cells, optical components, and more. The choice of substrate is critical as it influences the performance, durability, and functionality of the final product. The deposition process involves placing a thin layer of material (such as metals, oxides, or compounds) onto the substrate within a vacuum chamber, using techniques like thermal evaporation, sputtering, ion beam deposition, or chemical vapor deposition. The substrate must be compatible with the deposition material and process to ensure optimal results.
Key Points Explained:
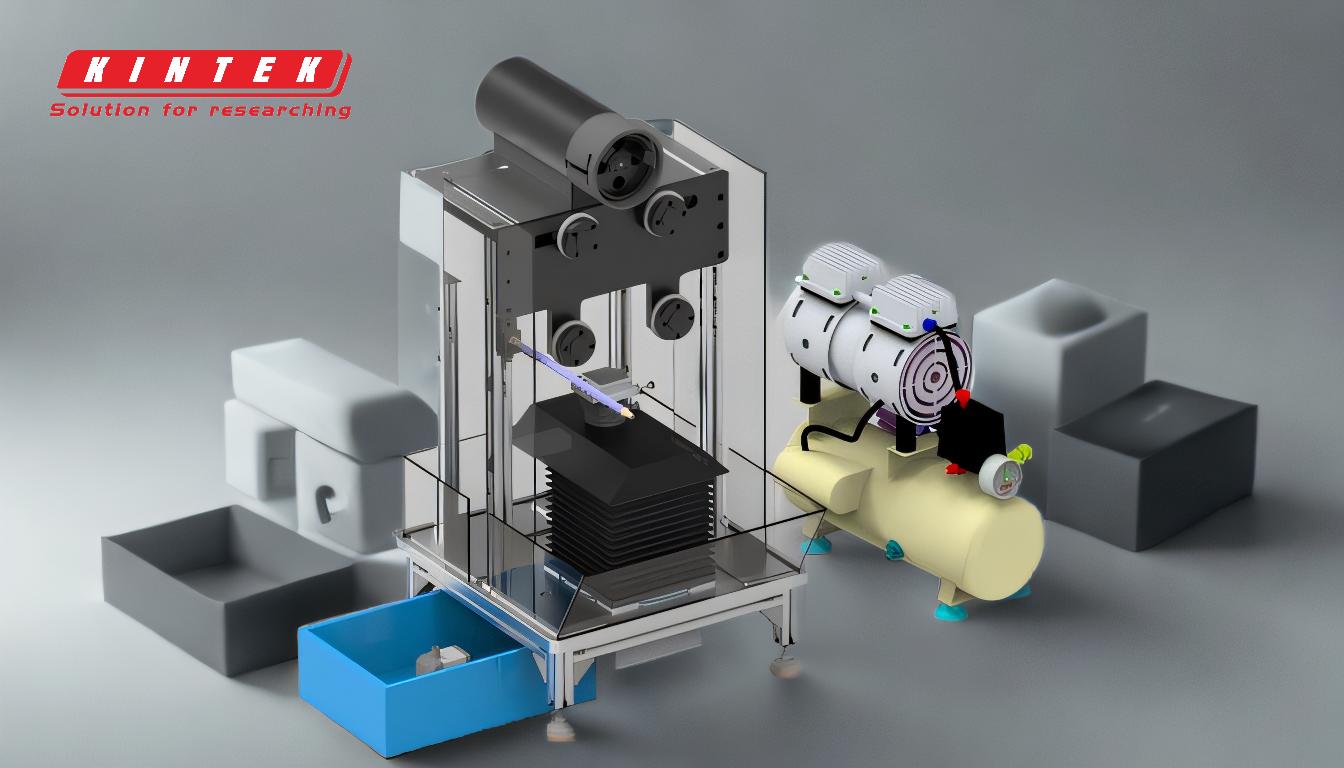
-
Definition of Substrate in Thin Film Deposition:
- The substrate is the base material or object that is coated during the thin film deposition process. It acts as the foundation for the thin film layer.
- Examples of substrates include semiconductor wafers, solar cells, optical components, and other specialized materials depending on the application.
-
Importance of Substrate Selection:
- The substrate must be carefully chosen based on the intended application, as it directly impacts the performance and functionality of the coated product.
- Factors such as thermal stability, mechanical strength, and compatibility with the deposition material must be considered.
-
Types of Substrates:
- Semiconductor Wafers: Commonly used in electronics and microelectronics for creating integrated circuits and other components.
- Solar Cells: Used in photovoltaic applications to enhance energy conversion efficiency.
- Optical Components: Such as lenses or mirrors, where the thin film improves optical properties like reflectivity or anti-reflectivity.
- Other Possibilities: Substrates can also include flexible materials, ceramics, or polymers, depending on the specific requirements of the application.
-
Compatibility with Deposition Materials:
- The substrate must be compatible with the deposition material (e.g., metals, oxides, or compounds) to ensure proper adhesion and performance.
- For example, metals are strong and durable but expensive, oxides are heat-resistant but brittle, and compounds offer a balance of strength and durability but may be challenging to work with.
-
Deposition Process and Techniques:
- The thin film deposition process involves placing a thin layer of material onto the substrate within a vacuum chamber.
- Common techniques include:
- Thermal Evaporation: Heating the material until it vaporizes and condenses onto the substrate.
- Sputtering: Bombarding a target material with ions to eject atoms that deposit onto the substrate.
- Ion Beam Deposition: Using an ion beam to deposit material onto the substrate.
- Chemical Vapor Deposition (CVD): Reacting gaseous precursors to form a solid film on the substrate.
-
Role of Substrate in Application Performance:
- The substrate's properties, such as thermal conductivity, electrical conductivity, and surface roughness, influence the final product's performance.
- For instance, in solar cells, the substrate must support efficient light absorption and electron transport, while in optical components, it must ensure minimal distortion and high clarity.
-
Challenges in Substrate Selection:
- Cost: High-performance substrates, such as semiconductor wafers, can be expensive.
- Material Compatibility: Ensuring the substrate and deposition material work well together without delamination or degradation.
- Processing Conditions: The substrate must withstand the deposition process conditions, such as high temperatures or vacuum environments.
-
Future Trends in Substrate Materials:
- Advances in nanotechnology and material science are leading to the development of new substrate materials with enhanced properties, such as flexibility, transparency, or improved thermal and electrical conductivity.
- For example, flexible substrates are gaining popularity in wearable electronics and foldable devices.
In summary, the substrate is a critical component in thin film deposition, serving as the foundation for the deposited material. Its selection depends on the application, material compatibility, and desired performance characteristics. Understanding the role of the substrate and its interaction with deposition materials and processes is essential for achieving optimal results in thin film applications.
Summary Table:
Aspect | Details |
---|---|
Definition | Base material coated during thin film deposition. |
Examples | Semiconductor wafers, solar cells, optical components, flexible materials. |
Importance | Influences performance, durability, and functionality of the final product. |
Key Factors | Thermal stability, mechanical strength, material compatibility. |
Deposition Techniques | Thermal evaporation, sputtering, ion beam deposition, CVD. |
Challenges | Cost, material compatibility, processing conditions. |
Future Trends | Flexible, transparent, and advanced conductive substrates. |
Need help selecting the right substrate for your thin film application? Contact our experts today!